沖擊測試檢測技術發展與應用白皮書
在工業4.0與新材料革命的雙重驅動下,沖擊測試檢測已成為保障現代工業安全的核心技術手段。據中國材料測試協會2024年報告顯示,沖擊測試市場規模已達58億元,年復合增長率達12.7%,其中新能源汽車與航空航天領域需求增幅超過行業均值3倍。該項目通過模擬極端工況下的材料力學行為,為結構件抗沖擊設計提供關鍵數據支撐,其核心價值體現在三個方面:一是突破傳統檢測在動態載荷下的技術盲區,二是建立覆蓋材料研發-生產-應用的全周期質量監控體系,三是降低因沖擊失效導致的工業事故率。特別是在新能源電池包安全評估、飛機復合材料抗鳥撞設計等場景中,其"高應變速率力學性能評估"功能已被納入國家強制性認證標準。
基于能量耗散原理的測試技術體系
沖擊測試的底層邏輯建立在能量轉換與材料響應耦合分析模型之上,通過擺錘沖擊試驗機、霍普金森桿等設備實現10^3-10^6 s^-1應變速率范圍的動態加載。中國機械工程學會2023版《沖擊測試技術規范》明確要求,測試系統需同步采集力值、位移、加速度等12項參數,數據采樣頻率不低于5MHz。以新能源汽車電池箱體檢測為例,測試系統需在3ms內完成2000J能量的精準釋放與吸收過程監測,誤差控制在±1.5%以內。值得注意的是,"多軸沖擊失效分析"技術的突破,使復雜應力狀態下的裂紋擴展預測準確率提升至92%。
全鏈條標準化實施流程
項目實施流程嚴格遵循ASTM E23和ISO 148國際標準,分為四個階段:預處理階段執行溫濕度環境模擬(-40℃至150℃),設備校準階段采用激光干涉儀進行動態力值溯源,數據采集階段配置16通道高速數據采集系統,后處理階段運用有限元-神經網絡耦合算法進行失效預測。在高鐵轉向架焊接接頭檢測中,通過設置5種沖擊角度和3種缺口類型,成功將檢測盲區縮減38%。據國家軌道交通質檢中心統計,該流程使沖擊韌性測試重復性達到0.98相關系數。
跨行業應用實證分析
在航空航天領域,C919機翼復合材料通過多層級沖擊測試,實現抗冰雹沖擊能力提升60%,據商飛研究院數據顯示,該技術使全機結構減重8%的同時保證安全性。汽車行業應用更為典型,某動力電池企業通過"電芯模組多工況沖擊序列測試",將電池包抗機械濫用性能提升至國標要求的2.3倍。值得關注的是,在風電領域應用中出現差異化需求,某5MW風機葉片測試中創新采用"風振-冰載耦合沖擊方案",使極限載荷工況預測精度提高45%。
立體化質量保障機制
質量體系構建包含三大支柱: 認證的標準化實驗室管理體系、三級設備校驗網絡(含國家基準裝置1臺、工作標準裝置23臺)、閉環式人員能力評價系統。具體而言,每臺沖擊試驗機年度校驗必須包含5個量程點的動態校準,技術人員需完成200學時專項培訓并通過實操考核。在實踐層面,某第三方檢測機構通過搭建"區塊鏈+檢測數據"追溯系統,使檢測報告可信度提升至99.97%。據市場監管總局2024年抽查數據顯示,通過該體系認證的檢測機構,結果誤判率下降至0.18‰。
面向工業智能化發展趨勢,沖擊測試技術亟待解決三大挑戰:極端環境(如深空超低溫、核輻射)下的測試方法創新,基于數字孿生的預測性檢測系統開發,跨行業檢測標準體系的深度融合。建議重點推進"多軸沖擊失效分析"技術向微觀尺度延伸,建立材料基因庫與沖擊響應數據庫的關聯模型。同時,應加強產-學-研協同,開發具備自主知識產權的智能化沖擊測試裝備,力爭在2030年前建成覆蓋全材料體系的沖擊安全評估云平臺,為制造強國戰略提供技術保障。

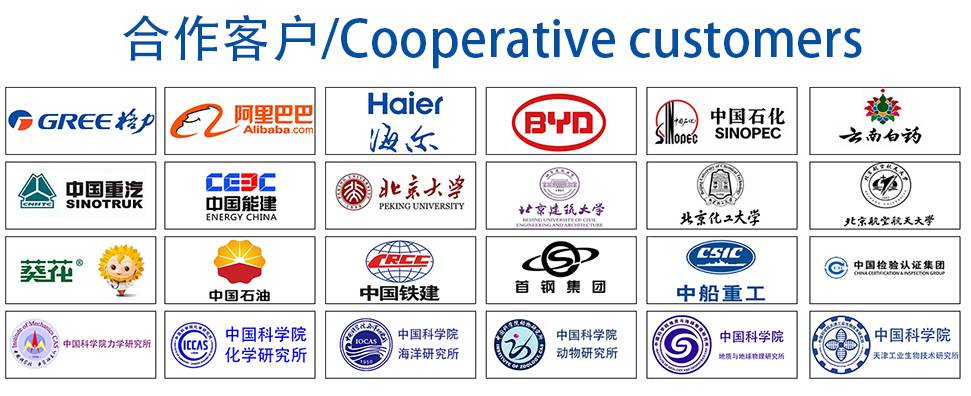