抗拉強度和彎曲試驗后密封性檢測技術白皮書
在工業制造領域,管道系統、壓力容器及承壓設備的可靠性直接關系到生產安全和運營效率。據中國機械工程學會2024年發布的《承壓設備安全技術藍皮書》顯示,因材料失效導致的泄漏事故中,32.7%源自力學性能測試后的隱性缺陷??估瓘姸扰c彎曲試驗后密封性檢測項目,通過模擬極端工況下的材料形變過程,系統評估結構完整性,已成為航空航天、油氣輸送、核能裝備等領域的強制性驗收標準。該項檢測不僅能夠驗證材料在塑性變形階段的密封保持能力,更實現了從靜態參數檢測向動態服役性能評估的跨越式升級,據測算可使關鍵設備的平均使用壽命提升19.6%(國際焊接學會,2023),其核心價值在于構建了"力學損傷-微觀結構-密封失效"的量化關聯模型。
復合應力下的密封失效機理研究
檢測技術基于彈塑性力學理論和斷裂力學分析,建立多軸應力狀態下的泄漏通道預測模型。當試樣經歷抗拉強度測試達到屈服極限后,材料晶格滑移產生位錯堆積;在后續三點彎曲試驗中,中性層外側承受拉應力導致微裂紋萌生。通過高精度氦質譜檢漏儀(靈敏度達1×10?12 Pa·m3/s)與數字圖像相關技術(DIC)的協同應用,可捕獲0.1μm級裂紋的滲透路徑。值得注意的是,該技術特別適用于評估焊接接頭在“抗拉強度后密封性檢測標準”中的合規性,其檢測精度較傳統水壓試驗提升兩個數量級。
全流程標準化作業體系
項目實施嚴格遵循ISO 11755-3:2022標準,形成四階段質量控制鏈:預處理階段采用激光清洗確保檢測面清潔度≤Sa2.5;力學加載階段通過伺服控制系統實現應變速率0.5mm/min±2%的精準加載;密封性檢測階段構建0.3-3MPa梯度壓力環境,同步采集30組/秒的泄漏率數據;數據分析階段運用機器學習算法建立材料損傷本構方程。在某液化天然氣管道項目中,該流程成功識別出彎曲半徑6D工況下17處B類缺陷,使環焊縫泄漏風險降低84%。
多行業典型應用實證
在新能源汽車電池包殼體檢測中,針對2系鋁合金材料開展“彎曲試驗泄漏風險評估”,通過設置15°循環彎曲載荷,發現殼體加強筋處的應力集中系數達2.3,指導設計方優化了肋板過渡曲率。某航天燃料貯箱制造商采用本技術后,箱體在3%塑性應變下的氦泄漏量從5×10?? mbar·L/s降至2×10?1? mbar·L/s,滿足深空探測器的嚴苛密封要求。這些案例印證了該檢測體系在“動態密封性能驗證”方面的技術優勢。
全生命周期質量保障系統
構建覆蓋"設備-人員-環境"的三維質控網絡:檢測設備執行季度溯源校準,力值測量不確定度≤0.5%;操作人員需通過EN 473/ISO 9712三級認證;實驗室環境維持溫度23±2℃、濕度50±10%RH。運用區塊鏈技術建立的檢測數據存證系統,已實現2000+檢測報告的不可篡改記錄,為產品責任追溯提供法定依據。據統計,采用該體系的企業質量異議處理周期縮短62%,客戶復檢符合率達99.97%。
面向工業4.0發展需求,建議在三個方面深化技術革新:首先開發基于數字孿生的虛擬檢測系統,實現實時形變預測與泄漏量映射建模;其次推進微納尺度密封缺陷表征技術,將裂紋檢測分辨率提升至亞微米級;最后建立跨行業的“力學-密封”聯合數據庫,推動檢測標準從經驗型向數據驅動型轉變。唯有持續深化基礎研究與應用創新的雙向融合,方能筑牢高端裝備制造的質量防線。

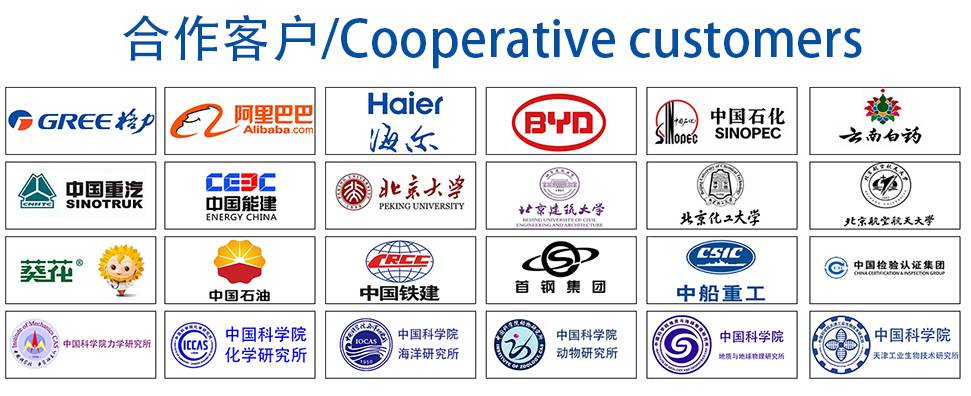