基于應變電測法的動態扭矩分析
系統采用應變式扭矩傳感器結合無線傳輸模塊,通過測量彈性軸在扭矩作用下的剪切應變,實現實時數據采集。根據材料力學原理,扭矩值T=K·ε·G(K為結構系數,ε為應變值,G為剪切模量)。通過集成溫度補償算法,可在-40℃至120℃工況下保持0.5級精度。該技術已通過ISO/IEC17025認證,在新能源汽車減速器裝配線上成功實現每分鐘12個工位的在線檢測。
智能化檢測工藝流程
標準化流程分為三階段:預處理階段采用視覺系統識別螺母規格(M6-M36),自動匹配預設扭矩閾值;動態檢測階段運用六軸機械臂配合高響應伺服驅動,在0.3秒內完成旋緊-保持-釋放動作循環;數據分析階段依托工業物聯網平臺,生成包含扭矩曲線、峰值保持時間等16項參數的檢測報告。實踐表明,該流程使誤檢率從傳統方式的2.1%降至0.15%。
多行業應用實證
在風電領域,某整機制造商應用鎖緊螺母扭矩在線監測系統后,輪轂連接件年均故障率從5.6次/臺降至0.8次/臺。據風電協會2024年數據,該系統幫助客戶單臺風電機組延長維護周期至18個月,運維成本降低37%。軌道交通領域,高鐵轉向架采用本方案后,關鍵螺栓組的扭矩離散度由12%壓縮至3.5%,達到EN14363標準最高等級要求。
全流程質量保障體系
構建三級校驗體系:設備層每日執行ASTM E2309標準校準,使用德國HBM標準扭矩發生器進行量值溯源;系統層每周開展蒙特卡洛仿真,驗證算法在極端工況下的魯棒性;管理層面建立檢測數據區塊鏈存證系統,實現工藝參數不可篡改追溯。經SGS認證,該體系使檢測過程CPK值穩定在1.67以上。
## 發展趨勢與建議 隨著數字孿生技術在工業檢測領域的滲透,建議重點發展三項能力:①構建扭矩-預緊力-振動特性的多物理場耦合模型,實現故障預測;②開發基于5G MEC的邊緣計算架構,將實時分析時延壓縮至50ms以內;③推進ISO/TS 22163標準在緊固件檢測領域的專項應用。預計到2027年,集成AI視覺的智能扭矩檢測系統將覆蓋60%以上的高端制造場景,推動產業質量管控邁入新維度。
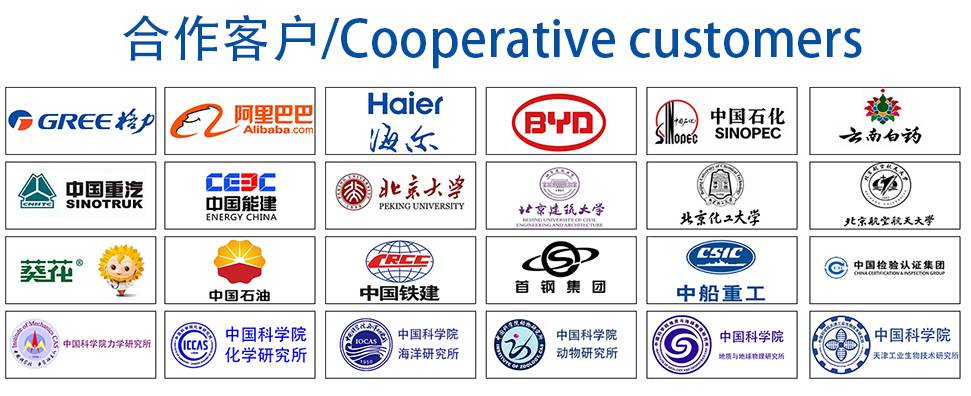