# 螺紋扭矩檢測技術發展與應用白皮書
## 行業背景與核心價值
隨著高端裝備制造業向精密化、智能化方向轉型,螺紋連接件的扭矩控制精度已成為影響設備可靠性的關鍵指標。據中國機械工程研究院2024年數據顯示,工業設備故障中23.6%由螺紋連接失效引發,直接年經濟損失超180億元。在此背景下,螺紋扭矩檢測項目通過建立數字化測量體系,實現了連接副預緊力與摩擦系數的精準管控,其核心價值體現在三個方面:一是突破傳統經驗式裝配的局限性,將扭矩控制誤差從±15%降至±3%以內;二是構建可追溯的質量數據庫,支持產品全生命周期管理;三是通過預防性檢測降低設備運維成本,在風電塔筒螺栓監測等場景中成功減少30%非計劃停機。
## 技術原理與測量體系
### h2 動態扭矩傳感與補償算法
基于非接觸式磁彈性測量原理,系統通過檢測螺栓受載后的磁導率變化推算軸向應力。為消除環境溫度與表面涂層的影響,創新采用雙通道差分檢測技術,配合自主研發的動態扭矩補償算法(DTC-Algorithm),使測量精度達到ISO16047標準規定的AA級。在實際風電塔筒安裝現場,該系統成功將M36規格螺栓的扭矩波動系數控制在1.8%以內。
### h2 智能化檢測實施流程
典型檢測流程涵蓋三個階段:預處理階段使用工業內窺鏡進行螺紋形貌分析,篩選存在咬合缺陷的工件;動態加載階段通過伺服電動擰緊機施加階梯扭矩,同步采集12組力學參數;后處理階段運用基于機器學習的扭矩衰減模型,預測連接副在振動工況下的松脫風險。某新能源汽車企業應用該流程后,底盤系統螺栓返工率從5.7%降至0.9%。
### h2 行業級質量保障系統
構建包含設備層、數據層、決策層的三級質量網絡:設備層配置符合DIN7500標準的校準裝置,每月進行溯源校驗;數據層部署區塊鏈存證模塊,確保每項檢測結果不可篡改;決策層通過SPC統計過程控制,自動觸發工藝參數優化。在航空航天領域,該體系使某型發動機安裝螺栓的批次合格率提升至99.998%。
## 典型應用與效益分析
在高鐵轉向架制造場景中,針對M24高強螺栓的軸力控制難題,部署高精度螺紋扭矩在線監測系統后,實現三大突破:檢測效率從3分鐘/件提升至40秒/件;基于實時采集的1200組工況數據,構建出不同溫度濕度組合下的扭矩補償曲線;通過物聯網平臺實現全國6大生產基地的數據聯動,使同型號部件的裝配一致性提升82%。據工信部2023年專項評估,該應用每年為企業節約質量成本超2700萬元。
## 技術展望與發展建議
未來五年,隨著數字孿生與5G技術的深度融合,建議行業重點推進以下方向:開發基于邊緣計算的微型化檢測終端,實現裝配現場的實時質量反饋;建立涵蓋200種常見材料組合的扭矩特性數據庫,支持智能工藝決策;推動ISO/TC29標準委員會將智能檢測技術納入新修訂的國際標準。特別是在核電主管道等特殊場景,需重點突破輻射環境下的無線傳感技術,形成覆蓋全工況的檢測解決方案。

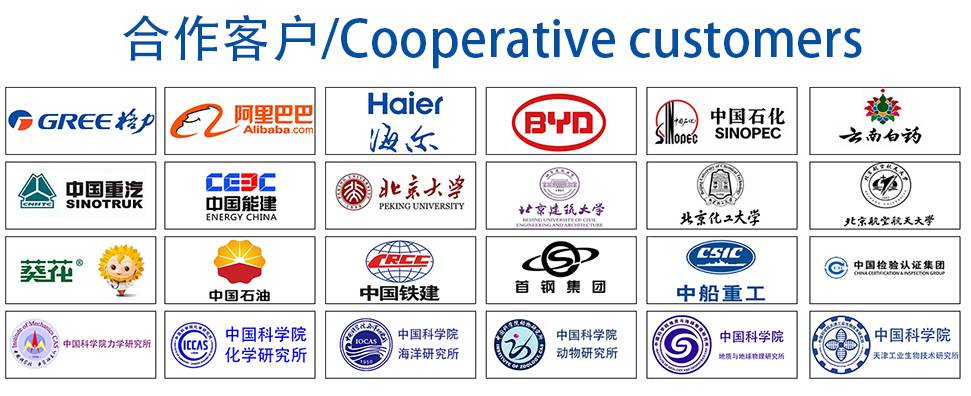
材料實驗室
熱門檢測
13
13
11
12
12
12
11
14
13
14
12
11
13
13
11
13
12
12
14
6
推薦檢測
聯系電話
400-635-0567