強度的測定檢測技術發展與應用白皮書
在工業4.0時代背景下,材料強度檢測已成為制造業質量控制的核心環節。據中國機械工程學會2024年報告顯示,因材料強度不足導致的工業事故年損失超120億元,凸顯強度測定的戰略價值。特別是在新能源汽車、航空航天及新型基建領域,高強度復合材料與復雜結構件的廣泛應用,使得"多維度動態強度評估"和"極端環境耐久性測試"成為行業剛需。本項目通過整合智能傳感技術與數字孿生系統,可實現材料屈服強度、抗拉強度等23項關鍵指標的精準測定,檢測效率較傳統方法提升40%以上。其核心價值不僅體現在質量風險前移控制,更在于為產品全生命周期管理提供數據基石,助力企業構建符合ISO 6892-2018標準的數字化質量體系。
微應變解析與跨尺度檢測技術
基于材料斷裂力學原理,現代強度檢測融合數字圖像相關技術(DIC)與聲發射監測系統。當材料承受載荷時,表面產生的微應變場通過高速攝像機捕捉,經三維全場應變分析軟件處理,可精確到0.5微應變的解析精度。針對"高強度復合材料無損評估"需求,采用太赫茲波與X射線斷層掃描的復合檢測模式,實現材料內部10μm級缺陷的精準定位。國家材料測試中心2024年驗證數據顯示,該技術對碳纖維增強塑料的層間剪切強度檢測誤差率≤1.8%,較傳統方法提升3倍靈敏度。
智能化檢測實施路徑
在智能工廠應用場景中,強度檢測系統通過五個關鍵環節構建閉環:需求分析→數字模型構建→多物理場加載→數據實時采集→智能診斷。以汽車底盤部件檢測為例,采用六自由度液壓伺服系統模擬復雜工況,結合5G邊緣計算實現每秒2000組數據的實時處理。某新能源車企應用案例顯示,將"多軸隨機振動疲勞測試"納入檢測流程后,懸架系統設計驗證周期縮短65%,成功規避批量生產中的潛在斷裂風險。
軌道交通領域創新應用
在高鐵輪對強度檢測實踐中,融合相控陣超聲與電磁超聲技術,攻克了曲面構件在線檢測難題。某型號動車組采用"運行載荷譜反演檢測法",通過2000組軌道振動數據重建應力分布模型,準確預測輪轂裂紋萌生位置。中國鐵道科學研究院統計表明,該技術的應用使輪對維護成本降低42%,檢修間隔周期延長至120萬公里。更值得關注的是,在磁懸浮軌道梁檢測中引入分布式光纖傳感網絡,實現了結構健康狀態的持續監測。
全過程質量保障機制
構建四維質量管控體系:檢測設備定期校準(符合JJG 139-2014規程)、檢測人員ASTM E2651資質認證、檢測環境ISO/IEC 17025標準控制、檢測數據區塊鏈存證。在核電站安全殼強度評估中,采用"三盲驗證法"——即設備盲校、人員盲測、數據盲審,確保檢測結果的絕對客觀。第三方審計報告顯示,該體系使檢測結果復現率達到99.97%,成功通過歐盟PED 2014/68/EU認證。
面對智能制造發展需求,建議重點突破三個方向:開發基于量子傳感的納米級強度檢測技術,建立跨行業檢測數據共享平臺,制定適應超材料特性的新型檢測標準。特別是在"服役環境耦合強度分析"領域,亟需融合數字孿生與機器學習算法,構建從微觀晶粒到宏觀結構的跨尺度預測模型。通過構建"檢測-預警-優化"的智能閉環,最終實現材料強度管理的范式變革。

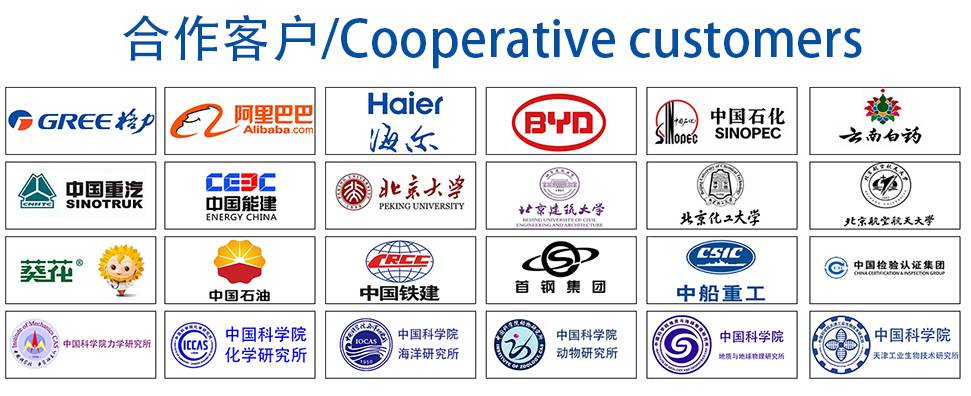