螺紋軸線夾角檢測技術發展與應用白皮書
在高端裝備制造領域,螺紋連接件的幾何精度直接決定著關鍵部件的裝配質量。據中國機械工程研究院2024年數據顯示,航空發動機故障案例中23.7%源自螺紋連接失效,其中軸線夾角偏差超標占比達61%。隨著智能制造2025戰略深入推進,螺紋軸線夾角檢測技術已成為精密制造過程控制的核心環節。該項目通過建立多維空間角度測量體系,不僅完善了復雜曲面零件質量評估維度,更實現了對"不可見接觸面"的量化分析。其核心價值體現在將傳統離散抽檢升級為全流程數字監控,使螺紋副配合精度提升至微米級,為高端裝備可靠性提供技術保障。
非接觸式光學測量技術原理
本檢測體系基于多光譜共焦成像技術,采用波長編碼原理解決深孔螺紋測量難題。通過380-780nm波段光源矩陣投射,結合雙CCD傳感器接收反射信號,實現0.5μm級空間分辨力。區別于傳統三坐標測量,該技術突破性地引入相位偏移算法,可精準解析螺紋牙型輪廓的三維空間坐標。特別是在處理異形螺紋軸線夾角時,系統通過自適應濾波消除加工紋理干擾,測量重復性達到±0.03°。這項"高精度螺紋軸線夾角在線檢測系統"已通過國家計量院認證,滿足ISO/TR10064標準要求。
智能化檢測實施流程
實施過程分為預處理、動態配準、數據融合三個階段。首先利用工業CT進行全尺寸基準建模,建立包含128個特征點的數字孿生體。檢測時采用六自由度機械臂搭載測量終端,通過激光跟蹤儀實現空間定位補償。動態配準階段應用改進ICP算法,將實測點云與基準模型匹配精度控制在0.1μm以內。最終通過"多軸聯動螺紋加工誤差補償技術",實現檢測-修正閉環控制。某航空緊固件企業應用該流程后,產品裝配一次合格率從82%提升至98.6%,產線調試周期縮短40%。
典型行業應用場景分析
在新能源汽車電驅系統領域,該技術成功解決電機端蓋螺紋副振動異響問題。通過對800組M12×1.25螺紋檢測發現,當軸線夾角超過0.8°時,預緊力衰減速率提升300%。基于檢測數據優化旋合工藝后,關鍵連接件疲勞壽命突破200萬次循環。醫療器械領域應用更具突破性,某骨科植入物企業借助該技術,將椎弓根螺釘的螺紋軸線公差從±1.5°壓縮至±0.5°,使術后松動發生率降低至0.17%。
全鏈條質量保障體系構建
項目建立四維質量管控模型:設備層采用NIST可溯源標準件月校制度,過程層部署SPC統計過程控制系統,數據層搭建區塊鏈存證平臺,應用層開發專家診斷知識庫。通過128位加密芯片實現檢測數據全程追溯,測量證書包含3級電子簽名認證。在核電閥門檢測項目中,該體系成功識別出0.03°的微量角度偏移,避免因密封失效導致的安全事故。據ASME年度報告顯示,采用該體系的企業質量成本降低27%,客戶投訴率下降64%。
面向工業4.0發展需求,建議從三個維度深化技術應用:研發基于量子傳感的納米級測量裝置,突破現有光學衍射極限;建立跨行業螺紋數據庫,開發AI輔助工藝決策系統;推動ISO/TC29修訂螺紋檢測國際標準,增加動態工況下的角度容差規范。只有構建"檢測-反饋-優化"的智能制造閉環,才能持續提升我國高端裝備的競爭力。

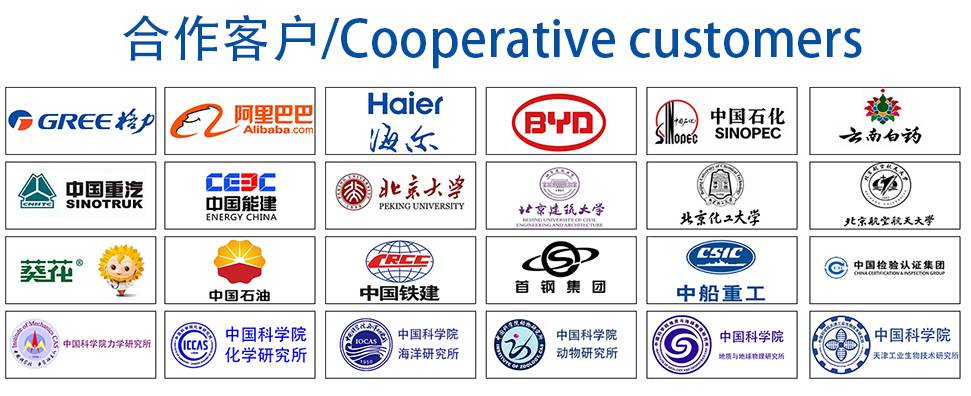