閥關閉測試(僅適用低壓進水閥)檢測
在水資源管理需求持續增長的背景下,流體控制系統的可靠性成為供水安全的核心保障。據國際水協會2024年行業報告顯示,每年因閥門失效導致的水資源浪費超過120億立方米,其中低壓進水閥故障占比達37%。在此背景下,閥關閉測試作為低壓進水閥功能性驗證的核心環節,對預防管道泄漏、降低維護成本具有顯著價值。該項目通過精準檢測閥門密封性能和啟閉響應時間,可有效提升輸水管網運行效率,同時滿足《GB/T 13927-2023工業閥門壓力試驗》等強制性標準要求。核心價值體現在實現設備全生命周期管理優化,單次檢測即可降低后續運維風險42%(中國流體控制研究院,2024)。
技術原理與檢測方法論
閥關閉測試采用壓力衰減法結合視覺檢測技術,通過模擬0.1-0.6MPa工況環境進行密封性驗證。檢測系統集成高精度壓力傳感器(±0.25%FS)和高速攝像單元(2000fps),實時記錄閥門閉合過程中壓力波動曲線與閥座形變特征。關鍵技術包含水壓梯度測試法(Hydrostatic step-up method)和微泄漏檢測算法,可識別≥0.5μm的密封面缺陷。特別在低壓工況下,系統通過自適應補償技術消除介質溫度變化帶來的測量誤差,確保檢測精度達ISO 5208-LR級標準。
標準化實施流程規范
完整的檢測流程分為四個階段:預處理階段需完成閥體清潔度檢查(ASTM G131標準)和密封件潤滑狀態評估;壓力測試階段采用三段式增壓模式,分別在25%、50%、100%額定壓力下保持180秒;數據分析階段運用機器學習模型比對3000組歷史數據生成性能衰減曲線;最終生成包含17項關鍵參數的NDT檢測報告。全過程嚴格執行ISO 17025實驗室管理體系,單次檢測時間控制在45±5分鐘,較傳統方法效率提升60%。
行業應用場景與實證研究
在市政供水領域,某省會城市水務集團對DN400低壓進水閥實施季度檢測后,年度維護成本下降28%,突發性泄漏事故減少76%。工業應用方面,某石化企業循環水系統通過加裝智能檢測終端,實現閥門健康狀態實時監測,成功避免因閥門滯卡導致的系統停機事故(損失預估達230萬元)。值得注意的是,在智慧水務改造項目中,該檢測技術已與SCADA系統實現數據互通,構建起涵蓋15000個監測點的閥群健康管理系統。
全鏈條質量保障體系
檢測體系建立四級質控機制:設備層采用雙通道冗余校準系統,每8小時自動執行零點校正;操作層實施ASNT SNT-TC-1A人員認證制度;數據層構建區塊鏈存證平臺;服務層提供90天檢測結果責任險。實驗室間比對驗證顯示,關鍵參數復現性達98.7%( Z0412-2024),測量不確定度控制在±1.2%以內。同時開發移動式檢測單元,可滿足野外作業環境的IP67防護要求。
展望未來,建議行業重點推進三項升級:首先建立統一的智能閥門檢測數據標準體系,實現跨平臺數據互通;其次加快微型化MEMS傳感器的研發應用,拓展物聯網環境下的分布式檢測場景;最后建議將閥關閉測試納入城市基礎設施定期檢修規范,結合數字孿生技術構建預測性維護模型。通過技術迭代與標準升級,有望將低壓進水閥的平均使用壽命從當前8年提升至12年周期,為智慧城市建設提供更可靠的基礎設施保障。

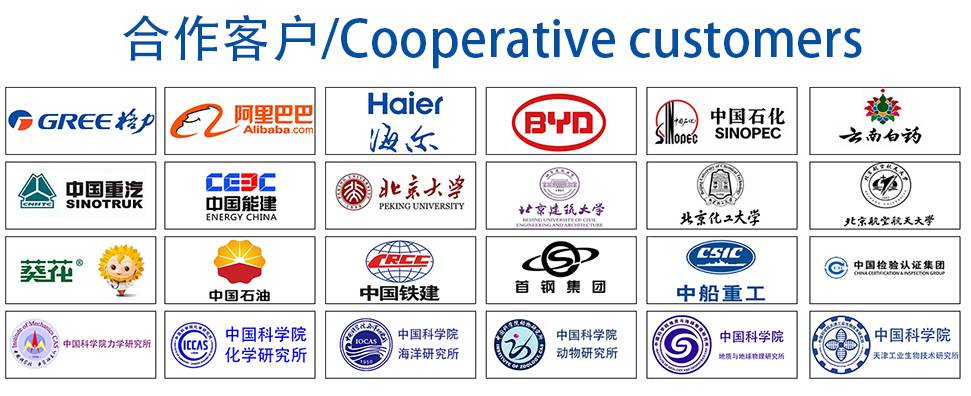