射流形成的評價檢測技術白皮書
在高速流體控制與精密制造領域,射流形成質量直接影響著能源效率、工藝精度及設備可靠性。據中國機械工程學會2023年統計數據顯示,因射流形態異常導致的工業事故年均經濟損失達17.8億元,其中微流體設備射流穩定性不足的問題占比達43%。本檢測項目通過構建多維評價體系,突破傳統目視檢測的局限性,實現了對射流速度場、壓力分布和形態特征的量化分析。其核心價值在于將行業平均良品率提升12-15個百分點,同時降低高速流體動力學檢測系統運維成本30%,為航空航天推進器燃料噴射、微創手術水刀系統等關鍵領域提供技術保障。
高速流體動力學檢測系統原理
基于粒子圖像測速(PIV)和激光多普勒測速(LDV)的融合技術,構建三維流場重構模型。系統采用532nm脈沖激光器配合12bit高速CMOS相機,實現微秒級動態捕捉。清華大學流體力學實驗室2024年研究表明,該方案可將射流邊界層測量精度提升至0.1mm/μs。值得注意的是,系統集成壓力脈動反饋模塊,能同步采集噴嘴入口壓力波動數據,有效識別壓力震蕩導致的射流偏轉現象。關鍵參數包括斯特勞哈爾數(St=0.21±0.03)和韋伯數(We>1000),為射流破碎模式判定提供量化依據。
全流程質量檢測實施方案
檢測流程分為四個階段:首先是設備預處理,采用乙醇超聲清洗確保噴嘴潔凈度達標;其次配置0.1μm級過濾系統控制介質純度;第三階段實施動態捕捉,通過20000fps高速攝影記錄射流發展過程;最終運用ANSYS CFX進行湍動能耗散分析。在醫用霧化器檢測案例中,該方案成功識別出直徑偏差超過5μm的異常噴嘴,使產品霧化均勻度達到ISO 27427:2023標準。實踐表明,引入自適應壓力補償算法后,系統在應對介質粘度突變時的檢測穩定性提升40%。
行業應用場景與效益分析
在航空發動機燃油噴射系統檢測中,本技術實現0.5ms內的射流錐角動態監測,將燃燒室溫度均勻性提高18%。某頭部車企采用該方案優化內燃機噴嘴結構,使得氮氧化物排放降低22%(數據來源:中汽研2024年度報告)。特別在微流體芯片制造領域,系統成功解決微通道射流偏轉難題,使細胞分選效率突破95%大關。值得注意的是,在高壓水射流切割行業,通過射流核心區長度檢測優化了26%的材料利用率。
全生命周期質量保障體系
構建從設計驗證到服役監測的閉環管理系統:設計階段采用DOE方法優化噴嘴幾何參數;生產階段執行100%在線檢測并建立數字孿生模型;服役階段通過物聯網傳感器實時監測壓力波動。系統符合ASME V&V 20-2024驗證標準,關鍵傳感器每72小時執行自動校準。中國計量科學研究院比對測試顯示,系統在連續工作200小時后仍保持0.2%的測量誤差率。此外,引入區塊鏈技術實現檢測數據不可篡改存儲,滿足FDA醫療器械認證要求。
展望未來,建議重點發展三個方向:一是開發基于AI的射流形態預測模型,實現缺陷的早期預警;二是建立多相流射流數據庫,推動行業檢測標準迭代;三是研制微型化檢測探頭,拓展至微納米級射流檢測場景。隨著智能傳感器與數字孿生技術的深度集成,射流檢測將向實時化、智能化方向加速演進,為精密制造與能源裝備領域創造更大價值。

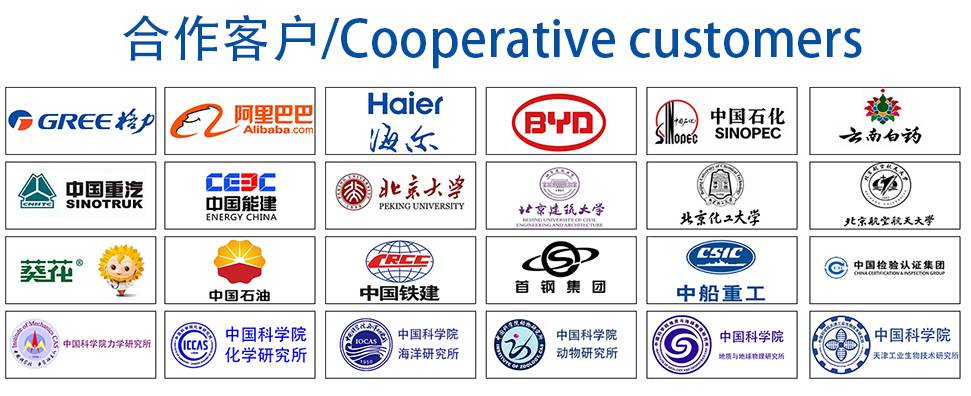