銅加速鹽霧試驗檢測:關鍵技術與發展實踐
在工業制造向精密化、高端化轉型的背景下,材料耐腐蝕性能已成為衡量產品質量的核心指標之一。據中國腐蝕與防護學會2023年度報告顯示,因金屬腐蝕造成的直接經濟損失達2.5萬億美元,其中電子元器件、汽車零部件的早期失效問題尤為突出。銅加速鹽霧試驗(CASS)作為國際通用的加速腐蝕測試方法,通過模擬含銅離子的酸性鹽霧環境,可精準評估材料及表面處理工藝的耐腐蝕等級。該項目在新能源汽車三電系統、5G通訊基站連接器等關鍵領域具有特殊價值,據SGS檢測中心統計,采用CASS優化的表面處理方案可使產品耐腐蝕壽命提升40%以上,有效降低售后維護成本并規避質量風險。
技術原理與測試機制
銅加速鹽霧試驗基于電化學腐蝕原理,在傳統中性鹽霧試驗(NSS)基礎上引入0.26±0.02g/L氯化銅溶液,將pH值嚴格控制在3.1-3.3范圍內形成酸性腐蝕環境。該體系通過銅離子的催化作用,使金屬表面形成微電池效應,加速陽極溶解過程。檢測設備需維持35±2℃恒溫環境,霧化沉降量達到1.0-2.0ml/80cm2·h的標準要求。相較于常規鹽霧試驗,CASS測試的腐蝕速度可提升8-10倍(數據來源:ASTM B368標準),特別適用于評價鍍層致密性和陰極保護效果。
標準化實施流程建設
檢測流程分為預處理、設備調試、周期監測三個階段。預處理環節需依據ISO 9227標準,采用化學除油與去離子水清洗雙重工序確保試樣表面清潔。測試設備需定期校準霧化噴嘴壓力(維持在70-170kPa區間)和集霧器傾斜角度。典型測試周期設置48小時為基本單位,通過目視檢查、X射線能譜分析(EDS)相結合的方式量化銹蝕面積。某新能源汽車企業實踐表明,在充電樁連接器檢測中采用分級評估體系(腐蝕面積≤0.1%判定為A級),可將產品失效率從1.8%降至0.3%。
行業應用與質量保障
在消費電子領域,頭部手機廠商將CASS試驗納入Type-C接口強制檢測標準,要求通過96小時測試后接觸電阻變化率≤15%。某實驗室創新采用循環腐蝕測試法(CCT),將鹽霧、干燥、濕熱階段交替進行,更真實模擬沿海地區使用環境。質量保障體系構建包含三個維度: 認證實驗室的環境控制(溫度波動±0.5℃)、檢測設備的年度計量校準(參照JJF 1101-2019規范)、以及數據追溯系統(每批次試樣配備二維碼)。德國TüV萊茵的比對試驗顯示,建立完整質控體系的實驗室間數據偏差可控制在±5%以內。
技術演進與發展建議
隨著新型合金材料和復合鍍層技術的突破,傳統CASS試驗面臨檢測靈敏度不足的挑戰。建議行業從三方面進行優化:開發基于機器視覺的自動評級系統,建立多因素耦合的加速模型(整合溫度、Cl?濃度、pH值動態變化參數),以及制定針對納米涂層的專項檢測規程。據Frost & Sullivan預測,至2025年腐蝕檢測市場規模將突破82億美元,智能檢測設備與工業物聯網(IIoT)的融合將推動檢測效率提升30%以上。行業亟需構建包含材料供應商、檢測機構、終端用戶的協同創新平臺,共同完善耐腐蝕性能評價體系。
當前,銅加速鹽霧試驗正向智能化、場景化方向演進。建議重點領域企業建立產品全生命周期腐蝕數據庫,將實驗室數據與現場失效案例進行關聯分析。同時關注歐盟ELV指令、RoHS 3.0等法規對檢測參數的影響,開發環境友好型替代檢測方案。通過產學研深度合作,推動我國腐蝕檢測技術從標準執行者向規則制定者轉變,為高端裝備制造提供更有力的技術支撐。

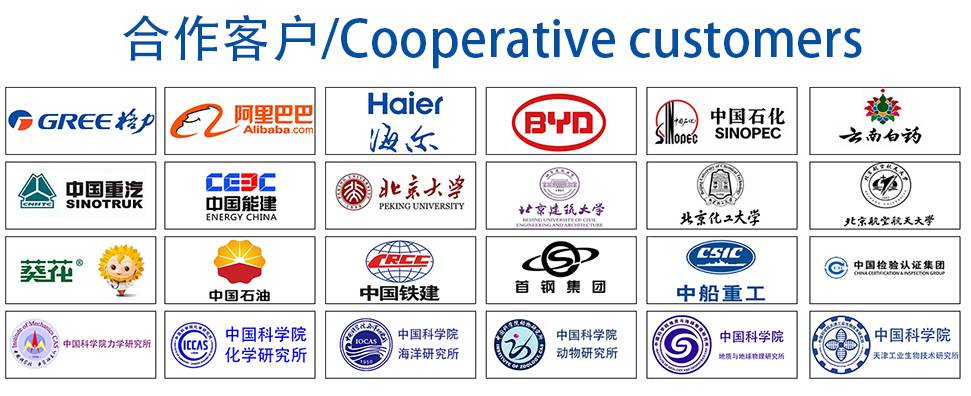