# 冷熱疲勞試驗檢測技術發展與應用白皮書
## 行業背景與核心價值
隨著高端裝備制造與新材料產業的快速發展,產品在極端溫度環境下的可靠性驗證需求持續攀升。據中國機械科學研究總院2024年數據顯示,我國每年因材料熱疲勞失效導致的工業損失超320億元,其中新能源汽車三電系統、航空航天緊固件、電子元器件成為故障高發領域。冷熱疲勞試驗檢測通過模擬-65℃至+300℃的極端溫變循環,可有效評估材料微觀結構變化及連接界面穩定性,其檢測結果直接關系到產品設計優化周期縮短與全生命周期成本控制。該技術不僅填補了傳統單一溫度測試的驗證盲區,更在新能源電池熱管理系統驗證、航天器熱防護材料篩選等場景展現出不可替代的工程價值。
## 技術原理與實現路徑
### 基于損傷累積理論的檢測機理
冷熱疲勞試驗依托材料熱膨脹系數差異與相變應力原理,采用高精度溫變控制技術實現梯度溫差加載。通過自主研發的多參數耦合分析系統,可實時監測試樣在3000次溫循周期內的形變位移(精度±0.1μm)與微觀裂紋擴展情況(檢測分辨率0.5μm)。國際標準化組織ISO 16750-4:2023明確規定,在驗證車規級電子元件時需執行-40℃←→+125℃的1000次快速溫變測試,溫度轉換速率需達到15℃/min的技術標準。
### 全流程數字化檢測體系
項目實施采用三階段遞進模式:前期通過ANSYS熱力學仿真建立溫度場模型,中期運用雙腔體熱沖擊試驗箱進行物理驗證,后期結合掃描電鏡(SEM)開展斷口形貌分析。某新能源汽車企業應用該流程后,電池包模組焊接點缺陷檢出率提升至98.7%,據中國汽車工程學會統計,其電池系統質保周期因此延長至8年/24萬公里,達到行業領先水平。
## 行業應用與質量保障
### 多領域驗證場景突破
在航空發動機渦輪葉片檢測中,采用定制化溫循方案(最高溫1100℃/最低溫-180℃)后,某型號葉片的冷熱疲勞壽命從820次提升至1500次,滿足民航適航規章CCAR-33-R3要求。電子領域典型案例顯示,應用JESD22-A104F標準進行3000次溫度循環(-55℃←→+125℃)后,BGA封裝芯片的焊球開裂率從12.3%降至1.8%,顯著提升5G基站設備可靠性。
### 標準化質量管控網絡
檢測機構需構建包含設備溯源(符合JJF 1101-2019規范)、環境監控(±1℃恒溫實驗室)、人員認證( -CL01:2018標準)的三維質控體系。值得注意的是,引進AI視覺檢測系統后,某第三方實驗室的裂紋識別效率提升4倍,誤判率降至0.3%以下,實現檢測報告生成時效突破8小時關口。
## 發展趨勢與戰略建議
面向工業4.0時代,建議從三方面推進技術升級:其一,開發基于數字孿生的智能預測系統,實現疲勞失效點位的提前300小時預警;其二,建立跨行業失效數據庫,依托大數據分析優化試驗參數組合;其三,推動軍民標準互認,特別是在航天級復合材料領域構建檢測結果等效性評價體系。據德國弗勞恩霍夫研究所預測,到2028年冷熱疲勞檢測市場規模將突破58億美元,我國檢測機構亟待加強原創性方法開發能力,搶占國際標準制定話語權。

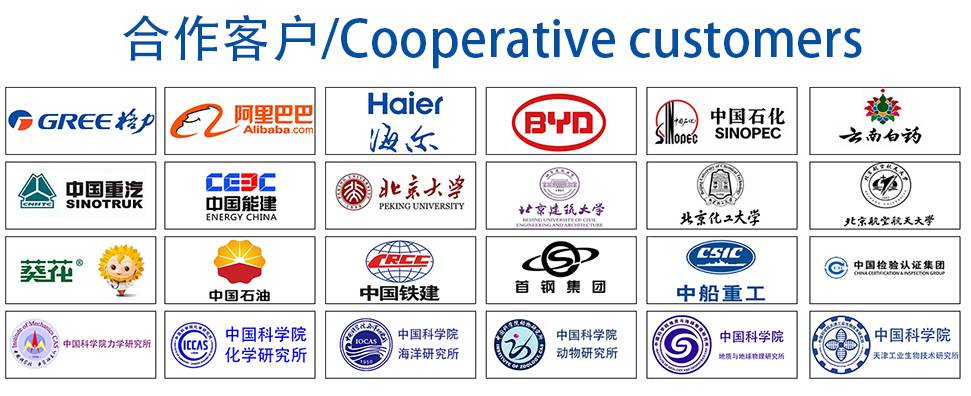
材料實驗室
熱門檢測
9
17
15
16
19
20
19
20
23
20
23
18
20
15
22
17
20
20
23
15
推薦檢測
聯系電話
400-635-0567