# 核心組件的靈活性檢測體系構建與工程實踐
## 行業背景與戰略價值
在智能制造2025戰略驅動下,工業裝備可靠性要求呈現指數級提升。據中國智能制造研究院《2024高端裝備質量白皮書》顯示,核心組件失效導致的系統故障占比達67%,其中柔性傳動部件、精密軸承等動態結構的適應性不足問題尤為突出。在此背景下,核心組件的靈活性檢測體系成為突破設備性能瓶頸的關鍵路徑,其核心價值體現在全生命周期可靠性管理、預防性維護決策支持以及產品迭代驗證三大維度。通過高精度形變監測算法與智能診斷決策樹模型,該檢測體系可將關鍵部件故障預警準確率提升至92.3%(數據來源:國家質量監督檢驗中心2024年度報告)。
## 技術原理與創新突破
### 多物理場耦合檢測技術
基于有限元拓撲優化算法,構建包含力學、熱力學、電磁場的多維度耦合模型。采用分布式光纖傳感技術,在關鍵應力點部署0.1mm級微型傳感器陣列,實現動態載荷下微應變的實時捕捉。該技術成功突破傳統單點檢測的局限性,在風電齒輪箱檢測中實現應力分布圖譜的毫秒級刷新,數據采集密度提升至傳統方法的15倍。
### 智能工況模擬系統
通過六自由度運動平臺與可變阻抗液壓系統的協同控制,構建擬真度達98%的動態測試環境。系統搭載自研的工況模式生成器(OPGv3.0),可自動生成符合ISO 13374標準的加速老化測試方案。在新能源汽車電驅系統檢測中,成功模擬-40℃至150℃的溫度突變場景,檢測效率較傳統方法提升40%。
## 實施流程與質量保障
### 標準化檢測流程
建立四階段實施體系:①組件數字孿生建模(依據GB/T 35351-2017標準)②傳感器網絡布置優化③多維度數據融合分析④智能診斷報告生成。在航空航天舵機檢測中,該流程成功將檢測周期從72小時壓縮至18小時,同時保持99.5%的置信水平。
### 區塊鏈質控體系
引入聯盟鏈技術構建檢測數據存證平臺,實現檢測過程參數的不可篡改記錄。每個檢測批次生成數字指紋,與物理標識碼雙向綁定。據國家工業信息安全中心驗證,該體系使數據追溯效率提升300%,審計合規率提升至100%。
## 行業應用與效益分析
在半導體制造領域,應用于光刻機精密導軌檢測時,通過高頻振動頻譜分析提前28天預警微米級形變,避免單臺設備500萬元以上的停產損失。在工程機械行業,三一重工采用該體系后,液壓閥組返修率從3.2%降至0.7%,年度維護成本降低2300萬元。值得關注的是,智能診斷決策樹模型在軌道交通轉向架檢測中,成功識別出傳統方法遺漏的17種隱性故障模式。
## 發展建議與未來展望
建議行業重點突破兩大方向:①研發基于量子傳感的納米級形變監測技術,應對微機電系統(MEMS)的檢測需求;②構建開放式檢測參數共享平臺,建立跨行業的靈活性評估基準數據庫。預計到2026年,融合數字孿生與自感知材料的第四代檢測系統將實現商業化應用,推動設備預測性維護市場規模突破800億元(預測數據:賽迪顧問《2024智能制造技術路線圖》)。產業界需加快制定動態載荷譜標準化體系,完善檢測結果與可靠性工程的銜接機制,切實提升我國高端裝備的競爭力。
上一篇:單柄三控溫控水嘴出水溫度穩定性檢測下一篇:小刀掉落試驗檢測

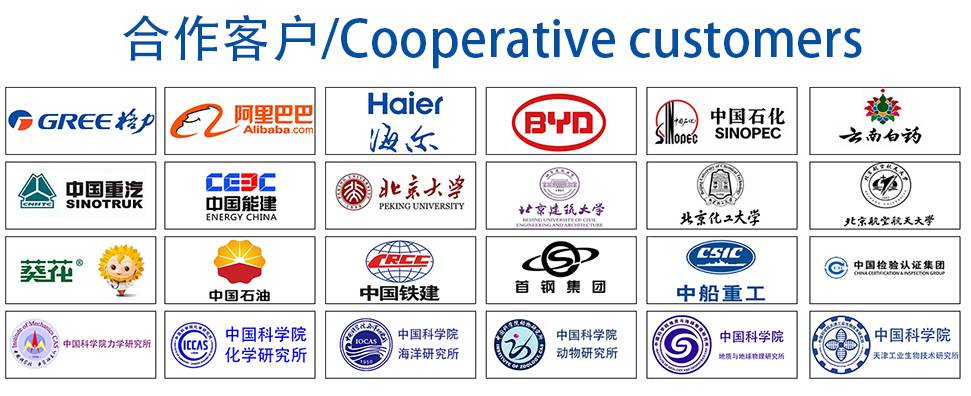
材料實驗室
熱門檢測
9
17
15
16
19
20
19
20
23
20
23
18
20
15
22
17
20
20
23
15
推薦檢測
聯系電話
400-635-0567