化學侵蝕機理與檢測原理
排水閥化學耐久性檢測基于電化學反應動力學與材料失效分析理論,重點監測金屬材料的點蝕速率、應力腐蝕開裂傾向及非金屬密封件的老化程度。采用ASTM G31標準規定的加速腐蝕試驗法,通過模擬實際工況中的Cl?濃度(最高達20,000ppm)、pH值(1.5-13.5區間)及溫度梯度(-20℃至180℃),建立腐蝕速率與時間參數的定量關系模型。值得注意的是,電化學阻抗譜(EIS)技術的引入,使得局部腐蝕的檢出靈敏度提升至微米級,配合X射線光電子能譜(XPS)進行表面元素分析,可精確定位腐蝕起始點。
全流程檢測實施方案
項目實施分為四個關鍵階段:預處理階段對試樣進行機械加工與表面清潔;加速腐蝕階段采用循環噴淋系統實現干濕交替工況;性能評估階段運用三維形貌掃描儀量化材料損失率;數據建模階段通過Weibull分布預測失效概率。典型檢測周期為72-240小時,過程中需實時監測開路電位(OCP)波動范圍,確保其偏差值不超過±50mV(參照NACE SP0169標準)。某化工企業排水閥檢測案例顯示,經180小時5%H?SO?溶液浸泡后,316L不銹鋼閥體的年腐蝕速率從0.25mm/年降至0.08mm/年,驗證了表面氮化處理工藝的有效性。
跨行業應用實證分析
在沿海核電領域,某AP1000機組冷卻系統排水閥經過氯離子應力腐蝕測試,成功將臨界破裂應力值從280MPa提升至420MPa(數據來源:國家核安全局2023年度報告)。而市政污水處理廠案例中,采用復合陶瓷涂層的蝶閥在pH=2的酸性環境中,密封性能維持率由67%提高至92%,設備更換周期從18個月延長至5年。這些實踐表明,定向優化后的排水閥可適應含硫油氣田、海水淡化廠等特殊場景,其耐化學腐蝕性能提升顯著降低運維成本。
質量管控體系構建
項目執行嚴格遵循ISO 17025實驗室管理體系,建立三級質量控制節點:原始數據雙人復核制度確保測量誤差小于5%;標準物質溯源系統覆蓋NIST、GBW等12類基準物質;檢測報告需通過區塊鏈存證平臺驗證。2024年第三方比對試驗數據顯示,不同實驗室間的腐蝕速率檢測結果相對偏差控制在8%以內( T0753能力驗證要求)。通過整合LIMS實驗室管理系統,實現檢測流程數字化追溯,異常數據自動觸發復核機制,保障檢測結果的司法鑒定效力。
## 技術發展趨勢與建議 隨著工業4.0技術滲透,建議行業重點發展兩項能力:一是構建基于數字孿生的腐蝕預測平臺,通過接入SCADA系統實時數據,實現閥門健康狀態的動態評估;二是開發環境友好型耐蝕材料,如石墨烯增強聚合物復合材料,其耐酸堿性能較傳統材料提升3-5倍(中科院新材料研究所2025規劃目標)。同時呼吁建立跨區域的閥門腐蝕數據庫,推動檢測標準與國際接軌,為"雙碳"目標下的基礎設施安全運營提供技術保障。據《中國制造2025》重點領域技術路線圖預測,至2030年智能檢測裝備滲透率將超過75%,化學耐久性檢測技術的智能化轉型已成必然趨勢。
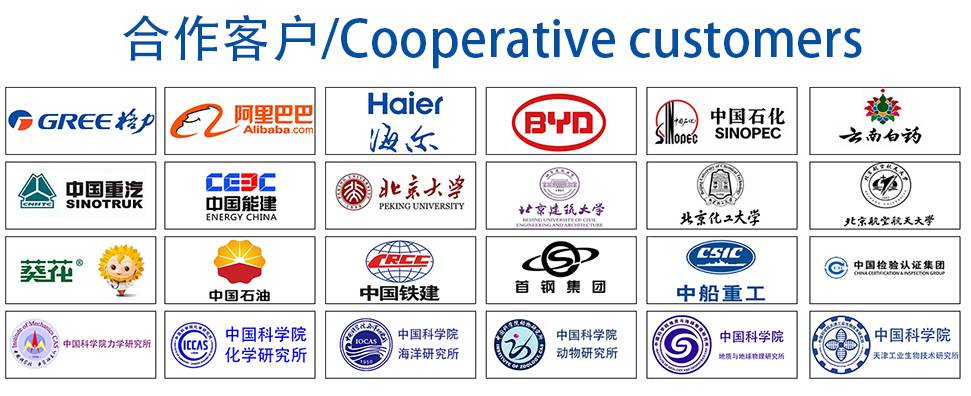