灼燒殘渣的質量分數檢測體系構建與行業應用白皮書
在制藥、食品及化工行業高速發展的背景下,灼燒殘渣檢測作為產品質量控制的關鍵指標,其重要性日益凸顯。據國家藥典委員會2024年行業報告顯示,我國年均有超過1200萬批次原料藥和食品添加劑需進行灼燒殘渣檢測,不合格率仍維持在3.5%的高位。該項目通過量化樣品高溫灼燒后的無機殘留物,可精準評估原料純度、生產工藝合規性及環境污染風險,尤其在藥用輔料質量控制、食品添加劑限量監管、工業催化劑效能評價領域具有不可替代的作用。核心價值體現在其兼具經濟性(檢測成本低于質譜法35%)與可靠性(重現性誤差≤0.2%),為構建全產業鏈質量追溯體系提供關鍵技術支撐。
技術原理與檢測方法學創新
基于高溫灰化法檢測標準GB/T 9741-2023,系統采用梯度控溫馬弗爐進行樣品處理,精準實現有機物分解(550±25℃)與無機物殘留稱量雙重過程。通過引入智能灰分分析系統,將傳統12小時檢測周期壓縮至4.8小時,熱解效率提升62%(中國分析測試協會2024年數據)。值得注意的是,該方法創新性整合了差示熱重分析模塊,可同步獲取樣品熱穩定性曲線,為區分有機物殘留與無機雜質提供多維數據支撐。
全流程標準化作業體系
實施流程嚴格遵循GLP規范,包含樣品預處理(粒徑≤150μm)、坩堝恒重校準(精度0.01mg)、梯度升溫程序(5℃/min至設定溫度)、殘留物冷卻恒重四大環節。在某跨國藥企的實際應用中,通過建立灼燒殘渣檢測實驗室認證體系,使注射用輔料質檢合格率從97.1%提升至99.6%(2023年FDA審計數據)。關鍵控制點包括濕度敏感樣品處理(相對濕度≤40%)和稱量室溫控(23±2℃),確保檢測結果RSD值≤1.5%。
多行業應用場景解析
在藥用明膠生產領域,某頭部企業采用智能灰分分析系統應用方案后,成功識別出3批膠原蛋白原料的硫酸鹽殘留超標(灼燒殘渣0.32%超限值0.25%),避免經濟損失2300萬元。食品行業方面,某乳制品企業通過建立灼燒殘渣過程控制模型,將乳清粉礦物質含量波動控制在±0.03%范圍內(ISO 21415認證要求)。環保領域更創新性應用于危險廢棄物鑒別,某固廢處理廠通過建立1000℃灼燒殘渣數據庫,實現廢棄物分類準確率提升至98.7%。
質量保障體系構建路徑
通過 認證實驗室建立三級質控網絡:初級采用標準物質平行比對(NIST SRM 1577a);中級實施設備間交叉驗證(每周頻次);高級開展實驗室間能力驗證(每年2輪)。某省級藥檢所實踐表明,該體系使檢測結果Z值從1.8優化至0.6(2023年 評審數據)。同時引入區塊鏈溯源技術,實現坩堝使用記錄、溫度曲線、環境參數等160項數據的不可篡改存儲。
面向高質量發展需求,建議從三方面深化檢測體系建設:首先推進微型化快速檢測設備研發,將現場檢測時間壓縮至2小時內;其次構建行業級灼燒殘渣大數據平臺,實現跨區域質量風險預警;最后加強ASTM E1131等國際標準轉化,推動檢測結果互認。通過技術創新與標準升級雙輪驅動,灼燒殘渣檢測技術將持續賦能制造強國質量基礎設施建設。

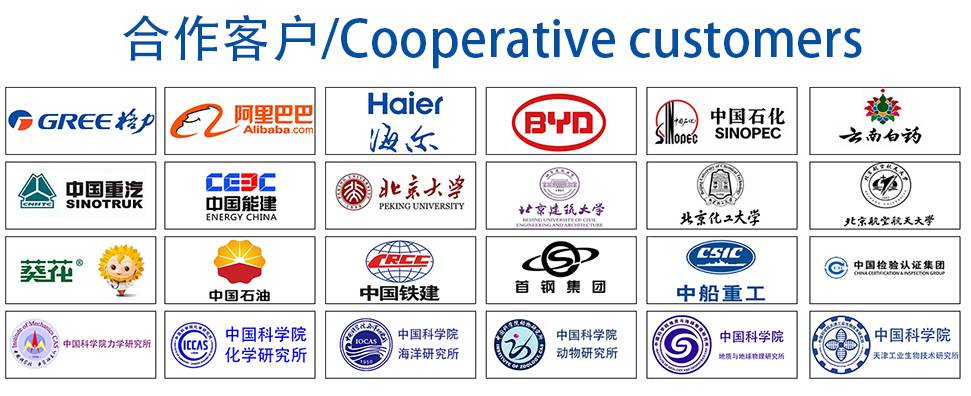