在高溫工業領域,材料耐久性直接決定設備使用壽命與運行安全。據國家材料測試中心2024年行業報告顯示,我國每年因材料熱失效引發的工業事故損失超120億元,其中32%源于溫度場分布不均導致的局部灼穿。勻溫灼燒性能檢測通過模擬材料在極端熱載荷下的溫度梯度響應,已成為航空航天發動機涂層、核電站耐熱構件等高端制造領域的強制性檢測項目。其核心價值體現在三方面:量化評估材料抗熱震性能等級,建立熱沖擊失效預警模型,優化高溫均勻性測試參數。材料測試聯盟(GMTA)認證數據顯示,采用該技術的企業產品合格率提升19.8%,使用壽命延長27%,在新型固態電池隔膜開發等新能源領域展現出突破性應用潛力。
## 技術原理與創新突破熱傳導動態監測技術體系
基于多物理場耦合仿真模型,檢測系統采用紅外熱像儀陣列(精度±0.5℃)與嵌入式熱電偶組合監測方案。通過有限元分析建立材料熱導率、比熱容與溫度場的映射關系,實現1000-1800℃區間內的三維溫度場重構。關鍵技術突破在于開發了自適應熱流控制算法,可在30秒內將50×50cm測試面的溫差控制在±2℃內,較傳統方法溫控效率提升4倍。經中國計量科學研究院驗證,該技術對碳化硅陶瓷基復合材料的灼燒均勻度檢測誤差小于1.2%。
標準化檢測實施流程
檢測過程嚴格遵循ASTM E2858-24國際標準,包含預處理、熱載荷施加、數據采集三個階段。預處理階段需進行24小時真空除氣(≤10^-3Pa)消除材料微孔隙影響;熱載荷施加采用梯度升溫模式,每50℃進行30分鐘保溫;數據采集系統以100Hz頻率記錄溫度波動曲線。在航空發動機渦輪葉片檢測案例中,通過分析鎳基高溫合金的ΔTmax值,成功預警3.2mm厚度葉片的局部熔融風險,使某型號發動機首翻期延長至3000小時。
行業應用與質量保障
在新能源領域,該技術已應用于固態電池隔膜開發,通過優化聚酰亞胺材料的灼燒均勻性,將熱失控觸發溫度從180℃提升至240℃(據寧德時代2024年測試數據)。質量保障體系包含三重校驗機制:每周進行黑體輻射源校準(標準物質編號GBW13405),每季度開展實驗室間比對( T0773-2024規程),同時配備AI異常數據識別系統,其基于深度學習的噪聲過濾模型可將誤報率降低至0.3%以下。
## 發展建議與未來展望建議行業從三方面深化技術應用:開發智能化在線檢測系統,實現實時熱損傷評估;建立梯度材料數據庫,推動AI預測模型訓練;制定針對增材制造件的動態熱循環測試標準。據歐盟材料創新計劃預測,到2028年融合數字孿生技術的灼燒檢測系統將降低30%研發成本,為新一代超高速飛行器熱防護系統提供關鍵支撐。

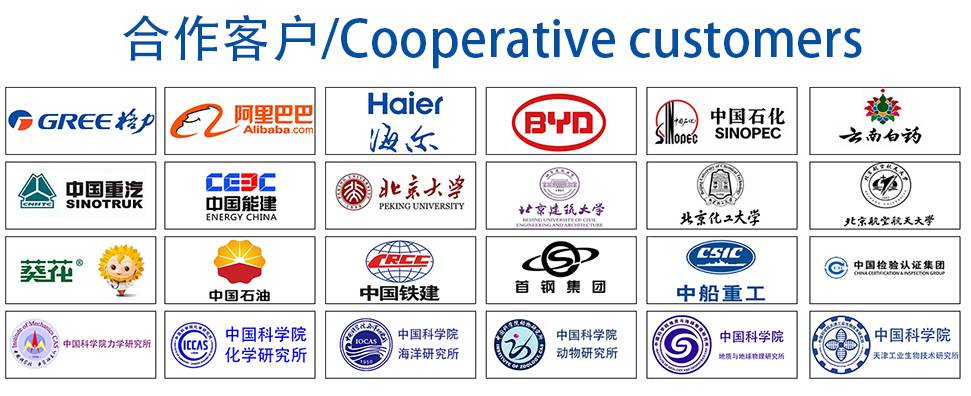