允許尺寸偏差檢測:智能制造時代的精密質量守護
在高端裝備制造領域,尺寸偏差控制已成為影響產品性能的核心質量指標。據中國機械工程學會2024年行業白皮書顯示,精密零部件因尺寸偏差導致的返工成本占制造總成本的17.6%,而航空航天領域關鍵部件尺寸超差率每降低0.1%,可提升整機可靠性3.2%。允許尺寸偏差檢測系統通過融合智能傳感、數字孿生等技術,構建了全生命周期的尺寸管控體系。其核心價值在于實現制造過程的可預測性偏差修正,將傳統抽檢的被動質控升級為在線動態補償的主動質量工程,在汽車動力總成裝配、半導體晶圓加工等場景中展現出顯著效益。
多模態傳感融合檢測技術
基于機器視覺與激光干涉的混合測量系統構成了現代尺寸偏差檢測的技術底座。根據國家精密測量技術實驗室2023年研究成果,采用多波長激光干涉儀(分辨率達0.01μm)與工業相機(500萬像素@60fps)的協同工作模式,可在0.8秒內完成φ50mm軸類零件的32項形位公差檢測。系統通過建立被測物的數字孿生模型,利用深度神經網絡對多源數據進行特征融合,使復雜曲面的三維輪廓重構精度提升至IT4級,滿足高精度齒輪箱體等關鍵部件的在線檢測需求。
三階段閉環質控流程
實施流程分為預處理、動態檢測、反饋修正三個階段。在新能源汽車電池模組裝配線中,系統先通過激光掃描獲取電池極片的基準坐標系,隨后利用嵌入式視覺系統實時監控0.15mm級疊片間隙。當檢測到累計偏差超過工藝允許值時,系統自動觸發機械臂進行在位補償,并同步更新MES系統的工藝參數數據庫。某頭部動力電池企業應用該方案后,模組裝配CPK值從1.12提升至1.67,單線日產能增加300件。
行業解決方案實證
在3C電子領域,某領先的手機結構件供應商部署了智能在線測量系統應對CNC加工的微米級精度挑戰。系統配置了12組高精度位移傳感器陣列,對鋁合金中框的128個關鍵尺寸進行全數檢測。通過引入貝葉斯統計過程控制算法,將測量數據與加工參數動態關聯,使產品尺寸合格率從92.4%提升至99.1%,同時將檢測節拍壓縮至傳統三坐標測量機的1/5。該案例驗證了允許尺寸偏差檢測在規?;a中的工程化應用價值。
四級質量保障體系
為確保檢測系統的持續可靠性,建立了涵蓋設備、算法、流程、人員的四維管理體系。定期使用NIST溯源的標準量塊進行計量校準(周期≤72h),運用蒙特卡洛模擬驗證檢測算法的魯棒性。在某航空發動機葉片檢測項目中,系統通過構建"檢測-分析-預警"的質量鏈,使葉片榫槽角度偏差檢出率提升40%,并將檢測報告生成時間縮短83%,支撐企業通過AS9100D航空航天質量管理體系認證。
技術演進與標準建設展望
隨著量子傳感技術的突破,下一代檢測系統有望實現亞納米級測量精度。建議行業重點發展三方面:一是建立基于數字線程的尺寸偏差知識圖譜,實現跨工序的偏差傳遞預測;二是制定智能檢測裝備的互聯互通標準,推動檢測數據與PLM系統的深度融合;三是培育"檢測工程師+數據分析師"的復合型人才隊伍。據工信部智能制造推進司預測,到2028年智能檢測裝備市場規模將突破1200億元,成為驅動制造業高質量發展的新質生產力。

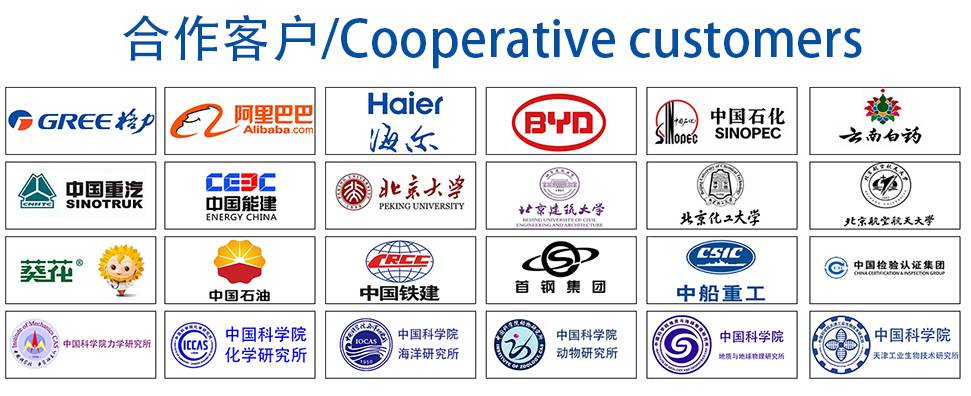