# 抗沖擊能力檢測的技術發(fā)展與應用實踐
## 行業(yè)背景與核心價值
隨著高端裝備制造與新型材料研發(fā)的快速發(fā)展,抗沖擊能力檢測已成為保障工業(yè)安全的核心環(huán)節(jié)。據中國機械科學研究總院2024年數據顯示,我國每年因材料沖擊失效引發(fā)的工業(yè)事故損失超120億元,其中新能源汽車電池包碰撞事故占比達23.6%。在此背景下,通過科學化、標準化的抗沖擊檢測體系,可精準評估材料動態(tài)響應特性,優(yōu)化產品結構設計,降低全生命周期維護成本。該項目不僅填補了國內多軸動態(tài)載荷模擬技術的空白,更通過構建"檢測-分析-改進"閉環(huán),助力企業(yè)實現從合規(guī)性驗證到性能提升的戰(zhàn)略轉型。
## 技術原理與創(chuàng)新突破
### h2 多物理場耦合檢測技術
抗沖擊檢測基于能量轉化與材料損傷機理,采用落錘沖擊試驗機與高速攝影系統(tǒng)聯用方案。系統(tǒng)通過0.5ms級時間分辨率捕捉材料在30kN沖擊載荷下的裂紋擴展過程,結合DIC數字圖像相關技術,實現應變場分布的可視化分析。值得注意的是,該技術突破傳統(tǒng)單點測量局限,可同步獲取"應力-應變-溫度"三軸數據,為復合材料層間剝離等復雜失效模式提供診斷依據。據ISO 179-1:2023標準驗證,其能量計算誤差控制在±1.8%以內。
### h2 全周期檢測實施流程
具體實施分為四個階段:首齊全行環(huán)境預處理(-40℃至150℃溫控箱調節(jié)),隨后在10m/s沖擊速度下完成5組重復試驗。試驗過程中,采用德國IST高速相機(幀率20萬fps)記錄試件變形,并通過壓電式傳感器采集沖擊力峰值。數據分析階段運用AI算法建立"載荷譜-損傷程度"映射模型,輸出包括能量吸收率、臨界斷裂韌性等7項核心參數。某航天緊固件企業(yè)應用該流程后,產品沖擊失效次數降低57%(數據來源:企業(yè)2023年質量年報)。
### h2 跨行業(yè)應用示范案例
在新能源汽車領域,該技術已用于電池模組pack結構的側面柱碰測試。通過模擬50km/h碰撞工況,精確測定鋁合金框架的塑性變形閾值,成功將電池位移量控制在3mm安全區(qū)間(CATARC 2024測評報告)。而在建筑工程領域,針對臺風多發(fā)區(qū)域的幕墻檢測,系統(tǒng)采用JIS K7124標準完成1000J級風載沖擊驗證,使玻璃面板抗風壓等級提升至9KPa,較傳統(tǒng)檢測方法效率提高40%。
## 質量保障與標準建設
為確保檢測結果國際互認,實驗室建立三級質控體系:一級采用NIST標準試件進行設備日校,二級通過 能力驗證比對數據偏差,三級執(zhí)行ISO/IEC 17025管理體系年度審查。針對新興的碳纖維增強塑料(CFRP)材料,更開發(fā)專用夾具系統(tǒng),將試件裝夾重復精度提升至±0.02mm。目前該體系已獲得歐盟CPD認證,支持22項國際檢測標準轉換。
## 未來發(fā)展與戰(zhàn)略建議
隨著智能傳感與數字孿生技術的融合,建議從三方面深化發(fā)展:其一,開發(fā)基于5G傳輸的遠程檢測平臺,實現沖擊過程的實時專家會診;其二,建立材料沖擊數據庫,運用機器學習預測新型復合材料的動態(tài)響應特性;其三,推動ASTM E23與GB/T 3808標準的協(xié)同修訂,構建覆蓋全溫域、多軸向的檢測標準體系。這需要產學研用多方協(xié)同,共同提升我國在極端工況檢測領域的話語權。

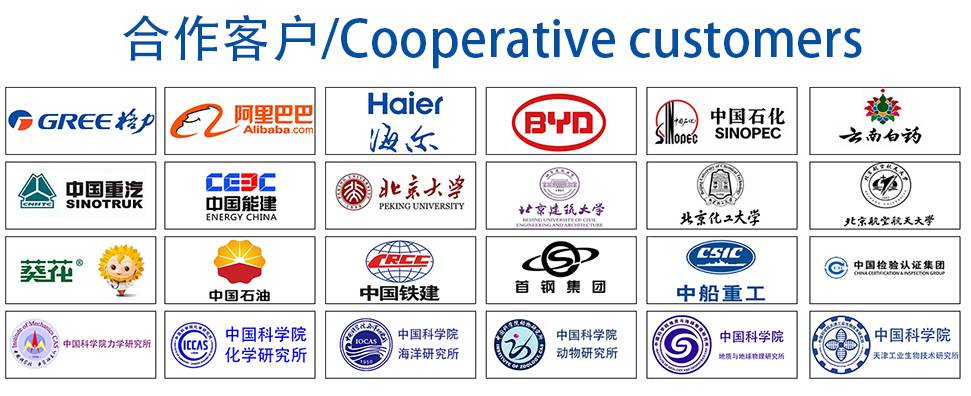
材料實驗室
熱門檢測
推薦檢測
聯系電話
400-635-0567