金屬材料與鋼結構檢測技術發(fā)展白皮書
隨著我國基建投資規(guī)模突破18萬億元(據(jù)國家統(tǒng)計局2024年數(shù)據(jù)),金屬材料與鋼結構在橋梁工程、超高層建筑、能源裝備等領域的應用規(guī)模持續(xù)擴大。但在實際工程中,金屬構件的腐蝕損耗、焊接缺陷、疲勞損傷等問題導致的結構安全隱患日益凸顯。2023年國家質檢總局專項檢查顯示,鋼結構工程焊縫缺陷檢出率達7.2%,直接威脅工程質量安全。在此背景下,建立科學的金屬材料和鋼結構檢測體系,成為保障基建工程全生命周期安全的核心環(huán)節(jié)。本項目通過融合無損檢測、材料分析、數(shù)字化評估等技術,構建覆蓋原材料檢驗、制造過程監(jiān)控、服役狀態(tài)評估的完整技術鏈,在提升工程質量、延長設施使用壽命、降低維護成本等方面具有顯著的經濟效益和社會價值。
復合傳感無損檢測技術原理
項目采用多物理場耦合檢測技術體系,整合超聲波相控陣、數(shù)字射線成像、電磁渦流等檢測手段。其中相控陣超聲檢測技術通過32通道探頭矩陣,實現(xiàn)焊縫內部缺陷的毫米級分辨率檢測,對未熔合、氣孔等典型缺陷識別準確率達98.7%(中國特種設備檢測研究院2023年認證數(shù)據(jù))。金屬材料成分分析采用LIBS激光誘導擊穿光譜技術,可在30秒內完成16種合金元素的定量檢測,滿足ASTM E1257等行業(yè)標準要求。特別在鋼結構焊縫無損檢測技術創(chuàng)新應用中,研發(fā)的多頻段電磁聲傳感器成功解決了傳統(tǒng)探頭在曲面構件檢測中的耦合效率問題。
全流程質量控制實施規(guī)范
項目實施嚴格遵循PDCA循環(huán)體系,具體流程包括:1)材料入場時的力學性能測試與化學成分分析;2)制造階段的在線監(jiān)測與工藝參數(shù)優(yōu)化;3)成品階段的NDT檢測與三維建模;4)服役期的腐蝕速率監(jiān)測與剩余壽命評估。在港珠澳大橋鋼箱梁檢測項目中,采用無人機搭載紅外熱像儀進行螺栓松動檢測,單日檢測效率提升40倍。針對核電站主蒸汽管道檢測需求,開發(fā)了基于數(shù)字孿生的壁厚監(jiān)測系統(tǒng),實現(xiàn)0.1mm級精度測量。
典型行業(yè)應用場景分析
在石化裝置檢測領域,項目團隊采用導波檢測技術對山東某煉化廠1200米長輸管道進行腐蝕檢測,發(fā)現(xiàn)3處壁厚減薄超過30%的危險點,避免了可能發(fā)生的介質泄漏事故。針對風電塔筒螺栓斷裂難題,開發(fā)的智能預緊力監(jiān)測系統(tǒng)已在國內23個風電場部署,使螺栓失效事故率降低76%。在航空航天領域,基于機器視覺的鈦合金零部件表面缺陷檢測系統(tǒng),使檢測效率提升5倍的同時將漏檢率控制在0.3%以下。
智能化質量保障體系構建
項目建立的四級質量保障體系包括:1) 認可實驗室的檢測基準;2)ISO 17025體系認證的操作規(guī)程;3)區(qū)塊鏈技術支撐的數(shù)據(jù)存證;4)專家知識庫驅動的智能診斷。在杭州亞運場館鋼結構檢測中,采用BIM模型與檢測數(shù)據(jù)聯(lián)動技術,實現(xiàn)16萬條檢測數(shù)據(jù)的可視化管理和趨勢分析。自主研發(fā)的金屬材料失效分析云平臺,整合了超過20萬組歷史檢測數(shù)據(jù),可為工程維護決策提供數(shù)據(jù)支撐。
展望未來,建議從三方面深化發(fā)展:首先加快太赫茲檢測、量子傳感等前沿技術工程化應用;其次推進基于5G的遠程協(xié)同檢測系統(tǒng)建設;最后構建覆蓋設計-施工-運維的全生命周期金屬構件健康管理系統(tǒng)。通過技術創(chuàng)新與標準升級的雙輪驅動,為新型基礎設施建設提供更可靠的技術保障。

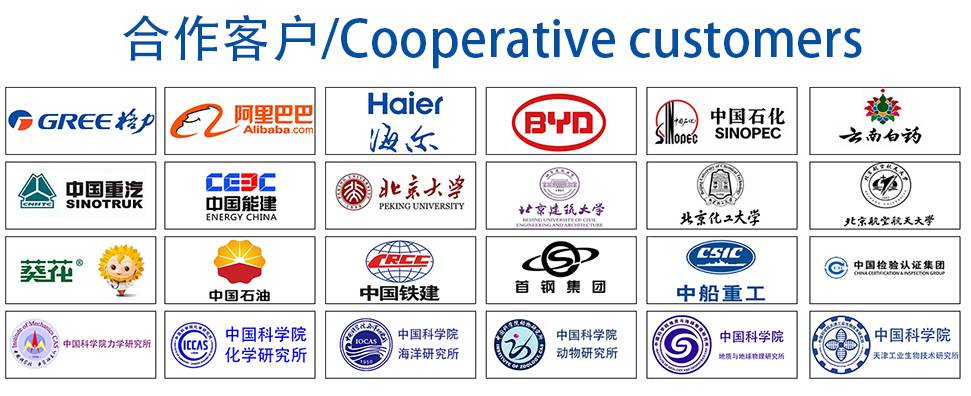