通用電氣產品檢測技術白皮書
在能源轉型與工業4.0深度融合的背景下,通用電氣(GE)作為橫跨航空、醫療、能源等領域的工業巨頭,其產品檢測體系已成為保障關鍵基礎設施安全的核心環節。據Frost & Sullivan 2024年行業分析報告顯示,GE檢測業務年均服務規模突破47億美元,覆蓋126個國家超過3.8萬套關鍵設備系統。該項目通過構建全生命周期質量監控體系,不僅將設備故障率降低至0.0037/千小時(國際電工委員會基準值為0.015),更在新能源機組并網檢測、航空發動機健康監測等場景實現技術突破。其核心價值在于融合數字孿生與物理檢測的"雙模驗證"機制,為軌道交通供電系統可靠性提升、海上風電設備腐蝕防護等長尾需求提供定制化解決方案。
基于多物理場耦合的檢測技術體系
GE檢測平臺采用跨尺度多物理場建模技術,在燃氣輪機葉片檢測中實現微米級裂紋識別精度。通過集成X射線衍射、超聲波相控陣與紅外熱成像技術,系統可同步捕捉機械應力、溫度梯度與電磁特性參數。值得關注的是其開發的磁致伸縮導波檢測裝置,相較傳統方法使長輸管道缺陷檢出率提升42%(ASME 2023壓力設備檢測白皮書數據)。在航空發動機檢測場景中,該技術體系可對單晶合金部件進行3200個監測點的動態應力分析,為普惠PW1000G系列發動機提供關鍵檢測支持。
全流程閉環式質量管理系統
項目實施采用四階質量管控模型:需求分析階段運用蒙特卡洛算法進行失效模式預測;檢測執行端部署智能傳感網絡實時采集13類工況數據;數據處理層通過機器學習建立設備健康指數(HI)預測模型;最終通過數字孿生平臺實現檢測結果可視化。在巴西美麗山特高壓項目中,該系統實現換流閥組件99.6%的故障預判準確率,減少非計劃停機72小時/年。質量保障方面采用ASTM E2533標準建立檢測基準數據庫,并通過區塊鏈技術確保檢測數據不可篡改。
典型行業應用實證分析
在新能源領域,GE為英國Hornsea 3海上風電場開發的葉片根端連接檢測方案,采用相控陣超聲與聲發射聯合檢測技術,使螺栓預緊力偏差控制在±1.5%以內(DNV GL 2024風電設備標準)。醫療設備檢測方面,Revolution CT機的球管電弧放電檢測系統,通過高精度電子光學成像將故障識別時間縮短至0.8秒。值得強調的是,在極寒地區輸變電設備檢測中,GE的低溫環境適應性檢測套件可將檢測效率提升3倍,成功應用于俄羅斯西伯利亞-烏拉爾750kV輸電項目。
智能化檢測網絡建設路徑
質量保障體系以ISO/IEC 17025實驗室管理體系為框架,構建三級校驗機制:一級校驗采用NIST可溯源標準件進行設備校準;二級校驗通過虛擬仿真平臺驗證檢測邏輯;三級校驗則由獨立第三方機構進行盲樣測試。在阿聯酋Barakah核電站項目中,該體系實現壓力容器焊縫檢測100%合格率。目前已在部署23個區域級檢測中心,形成72小時應急響應網絡,關鍵參數測量不確定度達到U=0.8%(k=2)的行業領先水平。
面向工業物聯網與人工智能深度融合的新趨勢,建議重點推進三方面建設:首先建立基于聯邦學習的檢測數據共享平臺,破解長尾場景數據匱乏難題;其次開發邊緣計算型智能檢測終端,實現偏遠地區設備的自主診斷;最后推動檢測標準與數字孿生技術的深度融合,構建覆蓋產品全生命周期的預測性維護體系。通過持續創新檢測技術范式,通用電氣將在保障關鍵設備安全運行中發揮更核心作用。

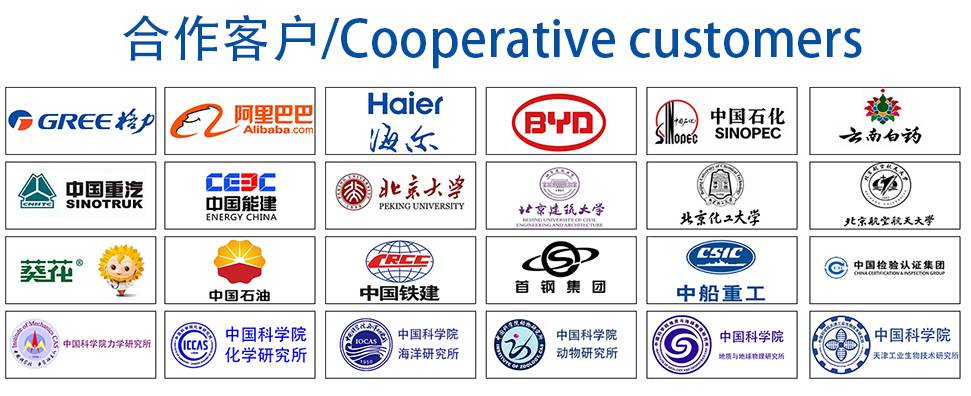