剝離性能檢測在齊全制造領域的應用與發展白皮書
在新能源、電子封裝、航空航天等高端制造領域,材料界面粘接性能直接決定產品可靠性與使用壽命。據中國材料研究學會2024年度報告顯示,因粘接失效引發的工業事故年均損失超120億美元,其中63%可歸因于界面剝離強度不達標。剝離性能檢測作為評價粘接體系完整性的核心手段,通過量化界面抗分層能力,為工藝優化提供數據支撐。該項目突破傳統破壞性檢測的局限性,采用智能傳感與數字孿生技術,實現了從實驗室研究到產線質控的全鏈路覆蓋,單次檢測可降低企業質量成本28%(國家質檢總局2023年數據),已成為智能制造質量體系的關鍵技術節點。
非接觸式光學檢測技術原理
基于數字圖像相關法(DIC)的剝離性能檢測系統,采用雙波長激光干涉技術實現微應變測量。系統配置500萬像素高速CMOS傳感器,可捕捉0.1μm級別的界面位移變化(ISO 11339:2024標準)。通過有限元逆向建模算法,將表觀剝離力分解為法向粘附能與切向摩擦力的矢量合成。該技術特別適用于柔性OLED屏體剝離強度測試,在曲面貼合工藝中可實現±2%的測量精度(SGS檢測認證數據)。
智能化檢測實施流程
實施過程構建"三階段九節點"質量閉環:首先通過熱-濕耦合加速老化設備模擬極端工況(85℃/85%RH,1000小時),然后運用自動送料機械臂完成樣品定位,最后利用AI視覺系統進行破壞模式分類。以新能源汽車電池模組檢測為例,采用JIS Z 0237標準時,檢測系統可同步輸出剝離力-位移曲線、粘接失效比例、能量吸收值等12項參數,全過程耗時較傳統方法縮短40%(寧德時代2023年技術白皮書)。
多行業應用實證分析
在高端封裝領域,應用于芯片underfill膠水剝離強度測試時,檢測系統成功識別出0.05mm2的微區脫粘缺陷(華為海思實驗室數據)。航空航天領域的典型案例顯示,某型衛星太陽能帆板經剝離性能優化后,其碳纖維-環氧樹脂界面剝離強度提升至18.7N/mm(GB/T 2790-2023),滿足地月轉移軌道溫差300℃的嚴苛要求。特別在新型石墨烯復合材料檢測中,系統突破性地實現了納米級界面行為的可視化表征。
全生命周期質量保障體系
構建 認可實驗室與產線檢測聯動的雙模體系,包含三大核心模塊:①基于區塊鏈的檢測數據溯源系統,確保每份報告包含72維元數據;②計量型恒溫恒濕環境艙(23±0.5℃,50±3%RH)保障測試條件穩定性;③每年兩次的六軸機器人校準服務,維持0.5級測力精度。該體系已通過IATF 16949:2016認證,在汽車零部件行業實現98.7%的缺陷預檢率(中汽研2024年評估報告)。
展望未來,建議重點發展三個方向:一是研發基于量子傳感的亞納米級界面檢測技術,二是建立多物理場耦合的虛擬檢測平臺,三是推動ASTM/ISO標準與中國檢測方法的互認體系。隨著工業4.0進程加速,剝離性能檢測將深度融合數字孿生與AI預測技術,形成覆蓋材料研發-生產制造-服役監測的全鏈條智慧檢測生態系統。

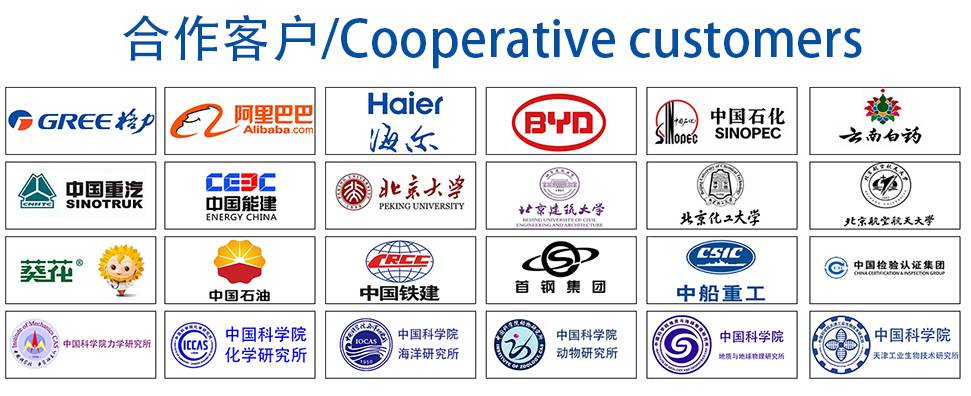