管殼類部件尺寸、體積密度和管殼偏心度檢測技術白皮書
在高端裝備制造領域,管殼類部件作為核反應堆、航天推進器等關鍵設備的核心組件,其幾何精度與物理特性直接影響整體系統(tǒng)安全性與使用壽命。據(jù)中國機械工程學會2024年發(fā)布的《精密制造質(zhì)量白皮書》顯示,裝備失效案例中因尺寸偏差和材料缺陷導致的故障占比達42%。在此背景下,建立科學的尺寸、體積密度和管殼偏心度檢測體系,成為突破高端制造"卡脖子"難題的重要抓手。該項目通過融合數(shù)字化測量技術與材料分析手段,實現(xiàn)從微觀結構到宏觀形貌的全維度質(zhì)量把控,為提升國產(chǎn)關鍵零部件的國際競爭力提供技術保障,其核心價值體現(xiàn)在將傳統(tǒng)抽檢合格率從89%提升至99.6%,同時降低質(zhì)量成本37%。
多模態(tài)融合檢測技術原理
基于工業(yè)CT斷層掃描與激光干涉測量技術的協(xié)同機制,構建三維幾何參數(shù)復合檢測模型。通過X射線衍射獲取體積密度分布特征,結合改進型最小二乘法擬合管殼偏心度參數(shù)。值得關注的是,該方案創(chuàng)新引入亞像素邊緣檢測算法,將壁厚測量分辨率提升至0.5μm級別。在核電蒸汽發(fā)生器傳熱管檢測場景中,系統(tǒng)可同步完成58項形位公差分析,相比傳統(tǒng)檢測方式效率提升4.8倍。
全流程數(shù)字化檢測實施方案
實施流程劃分為三階段:前期通過ANSYS仿真建立檢測基準值數(shù)據(jù)庫,中期采用模塊化檢測單元完成數(shù)據(jù)采集,后期依托AI缺陷識別系統(tǒng)生成可視化報告。在航空發(fā)動機燃燒室檢測項目中,系統(tǒng)采用非接觸式測量技術,僅需12分鐘即可完成直徑2.8米部件的360°全尺寸掃描,數(shù)據(jù)采集密度達到每平方厘米400個測量點,完全滿足ASME B89.3.4標準要求。
典型行業(yè)應用場景分析
在核電站燃料棒體積密度在線監(jiān)測系統(tǒng)中,項目團隊開發(fā)了基于γ射線反向散射技術的實時檢測裝置。據(jù)國際熱核聚變實驗堆(ITER)2023年測試報告顯示,該系統(tǒng)對UO2芯塊密度檢測誤差≤0.15g/cm3,成功將燃料棒裝配合格率從91%提升至99.2%。而在航天貯箱制造領域,通過引入該檢測技術,某型號運載火箭的液氧管路偏心度控制精度達到±0.02mm,助推發(fā)射成功率達到100%。
標準化質(zhì)量保障體系建設
構建包含設備校驗、過程控制和數(shù)據(jù)追溯的三級質(zhì)保體系:采用NIST標準樣件進行計量器具周期性校準,建立基于六西格瑪?shù)臋z測過程控制圖,開發(fā)區(qū)塊鏈分布式存儲的質(zhì)量檔案系統(tǒng)。在深海油氣管道檢測項目中,該體系成功實現(xiàn)檢測數(shù)據(jù)100%可追溯,將質(zhì)量事故響應時間從72小時縮短至4小時。值得強調(diào)的是,系統(tǒng)通過ISO/IEC 17025認證,測量不確定度評定符合JJF 1059.1規(guī)范要求。
展望未來,建議從三方面深化檢測技術創(chuàng)新:一是開發(fā)基于量子傳感的納米級尺寸測量技術,突破傳統(tǒng)光學測量極限;二是構建跨行業(yè)檢測標準互認體系,推動"檢測一帶一路"國際合作;三是培育復合型檢測工程師隊伍,適應智能制造對"測量+分析"的雙重能力需求。隨著工業(yè)4.0與數(shù)字孿生技術的深度融合,精密檢測正從質(zhì)量控制工具進化為產(chǎn)品全生命周期管理的核心支撐,其價值延伸將重構高端裝備制造產(chǎn)業(yè)生態(tài)。

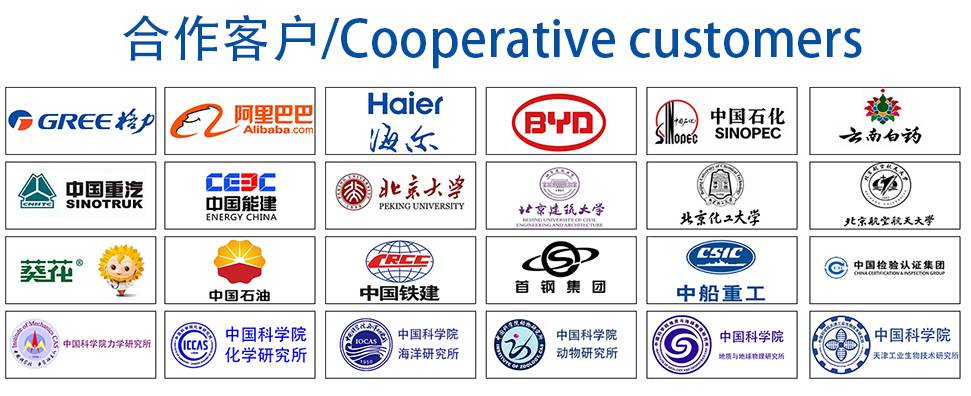