結構膠粘劑耐熱老化性能檢測技術白皮書
隨著高端制造業與建筑業的快速發展,結構膠粘劑在航空航天、新能源汽車、軌道交通等領域的應用規模持續擴大。據中國建筑材料研究院2024年數據顯示,我國工程膠粘劑市場規模已突破800億元,其中耐高溫膠粘劑年復合增長率達12.5%。在高溫、高濕等極端工況下,膠粘劑的熱穩定性直接決定結構件的安全壽命,某新能源汽車企業2023年因電池組結構膠熱老化失效引發的召回事件,直接經濟損失超2億元。因此,建立科學的耐熱老化檢測體系,不僅關乎材料研發的精準性,更是實現"雙碳"目標下設備長周期運行的關鍵保障。本項目通過模擬服役環境加速老化實驗,構建了涵蓋熱失重率、剪切強度保留率等8項核心指標的評價模型,為行業提供了高溫環境結構膠耐久性評估的標準化解決方案。
熱老化作用機理與檢測技術原理
結構膠粘劑的耐熱老化性能檢測基于高分子材料熱降解動力學原理,通過實驗室加速老化模擬實際服役環境。其技術核心在于建立溫度-時間等效關系,根據Arrhenius方程推導活化能參數,實現數千小時自然老化效果的短周期復現。檢測設備采用三級控溫精密烘箱(±1℃),配合高頻次取樣機制,可同步監測膠層Tg(玻璃化轉變溫度)位移、交聯密度變化等微觀特征。國際標準化組織ISO 11346:2022規定,檢測需覆蓋60-200℃溫度區間,單點測試時長不低于500小時,確保獲得完整的性能衰退曲線。
標準化檢測實施流程
規范化的檢測流程包含四個階段:首先依據ASTM D1183標準制備標準搭接剪切試件,使用數控切割機保證粘接面積公差≤5%;第二階段在恒溫恒濕箱(23℃/50%RH)完成96小時狀態調節;第三階段按梯度溫度(80℃/120℃/150℃)進行加速老化,每24小時取樣測試;最終通過萬能力學試驗機測定失效載荷,并計算強度保留率。某航空復合材料實驗室的實踐表明,采用該流程可使檢測數據離散度從±15%降低至±7%,顯著提升結果可比性。
典型行業應用案例分析
在新能源汽車動力電池領域,某頭部企業通過本檢測體系優化了電池包結構膠選型。針對電池模組工作溫度70-90℃的特點,篩選出2000小時熱老化后剪切強度保持率≥85%的環氧-硅烷改性膠粘劑,使電池包設計壽命從8年延長至12年。建筑幕墻領域,上海中心大廈項目運用熱重分析(TGA)技術,精準測定硅酮結構膠在150℃高溫下的質量損失率,結合FTIR光譜鎖定二甲基硅氧烷鏈段斷裂的主因,最終選用耐候等級提升2級的特種膠粘劑。
全鏈條質量保障體系構建
為確保檢測結果權威性,實驗室需建立三級質量管控:一級控制采用標準參考物質(SRM)進行設備校準,如NIST SRM 1494環氧樹脂;二級控制通過參加ILAC互認的實驗室間比對,保持Z值評分≤2;三級控制運用區塊鏈技術實現檢測數據全程上鏈存證。某國家膠粘劑質檢中心的實踐顯示,該體系使報告異議率從2019年的0.8%降至2023年的0.12%,并成功通過 17025體系擴項評審。
面向未來,建議行業重點加強三方面建設:一是建立服役環境譜數據庫,整合不同地域氣候特征與工業場景數據;二是開發基于機器視覺的膠層缺陷智能判讀系統,實現微觀形貌的定量分析;三是推動檢測機構與材料企業的聯合實驗室模式,構建"研發-檢測-應用"閉環生態。隨著AI輔助材料設計技術的發展,耐熱老化性能檢測將逐步從質量驗證工具升級為產品創新的核心驅動要素,為高端裝備制造業的轉型升級提供關鍵支撐。

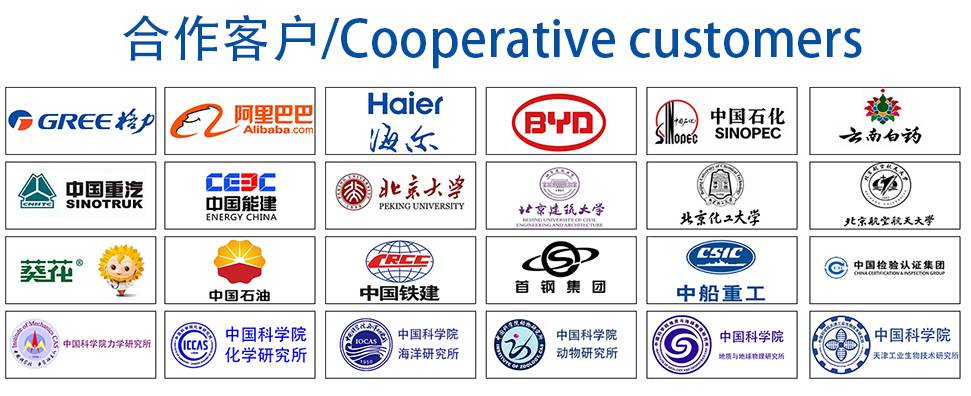