壓縮試驗檢測基于材料力學本構關系,采用位移控制或載荷控制模式,通過萬能試驗機對試樣施加連續(xù)或階梯式軸向壓力。根據(jù)ASTM E9-24標準,測試系統(tǒng)須確保載荷精度達到±0.5%、變形測量分辨率優(yōu)于1μm。創(chuàng)新性的非接觸式應變測量技術(DIC數(shù)字圖像相關法)已實現(xiàn)0.02%的應變測量精度,特別適用于碳纖維增強塑料等非均勻材料的局部變形分析。值得關注的是,針對蜂窩結構材料的多向壓縮耦合測試方案,成功解決了傳統(tǒng)方法難以準確獲取層間剪切模量的技術難題。
## 全流程檢測實施規(guī)范標準化作業(yè)流程涵蓋試樣制備、環(huán)境調控、數(shù)據(jù)采集三個階段。試樣加工需嚴格遵循ISO 12135:2023關于尺寸公差(±0.02mm)和端面平行度(≤0.01mm)要求,對于陶瓷基復合材料等脆性材料還需進行表面拋光處理。檢測環(huán)境控制方面,軍工級實驗室已實現(xiàn)溫度波動±0.5℃、濕度偏差≤2%RH的精密調節(jié)能力。在新能源汽車電池模組壓縮測試中,全程紅外熱成像監(jiān)控可同步捕捉力-熱耦合效應,為熱失控防護設計提供多維數(shù)據(jù)支撐。
## 行業(yè)應用場景解析在風電葉片主梁帽檢測領域,復合材料層間抗壓強度檢測已成為葉片認證的強制性項目。金風科技2024年技術白皮書顯示,采用ASTM D6641標準進行碳纖維環(huán)氧樹脂體系的壓縮試驗后,葉片極限承載能力預測準確度提升37%。汽車工業(yè)中,金屬材料軸向壓縮測試數(shù)據(jù)正深度融入車身輕量化設計流程,上汽集團通過建立材料壓縮屈曲數(shù)據(jù)庫,使B柱抗撞性能仿真誤差從15%降至7%以內。更為前沿的應用體現(xiàn)在太空可展開機構檢測,航天五院通過-180℃低溫環(huán)境下的超彈性合金壓縮試驗,成功驗證了月面探測器的折疊臂可靠性。
## 質量保障體系構建檢測機構需建立三級校驗體系確保數(shù)據(jù)權威性,包括每日設備自檢(參照JJG 139-2023規(guī)程)、季度第三方校準以及年度CMA資質審查。中國計量院主導的實驗室間比對項目顯示,頂級檢測中心的壓縮強度測試離散系數(shù)已控制在1.8%以下。針對增材制造件的特殊檢測需求,華測檢測等機構開發(fā)了基于CT掃描的缺陷補償算法,使含內部孔隙構件的強度預測誤差降低42%。智能質控系統(tǒng)的應用更是將檢測報告生成效率提升60%,同時實現(xiàn)數(shù)據(jù)溯源性管理。
# 技術發(fā)展與行業(yè)展望隨著智能傳感技術和數(shù)字孿生模型的深度融合,壓縮試驗檢測正朝著在線化、智能化方向演進。建議行業(yè)重點突破兩方面:一是開發(fā)可模擬實際工況的多場耦合測試設備,如同時施加壓縮載荷與腐蝕介質的海上風電檢測系統(tǒng);二是建立基于機器學習的材料性能預測模型,通過有限試驗數(shù)據(jù)推演全應力-應變曲線。據(jù)國家新材料測試評價平臺規(guī)劃,到2027年將建成覆蓋60類戰(zhàn)略材料的壓縮性能數(shù)據(jù)庫,為《中國制造2025》戰(zhàn)略實施提供關鍵基礎支撐。

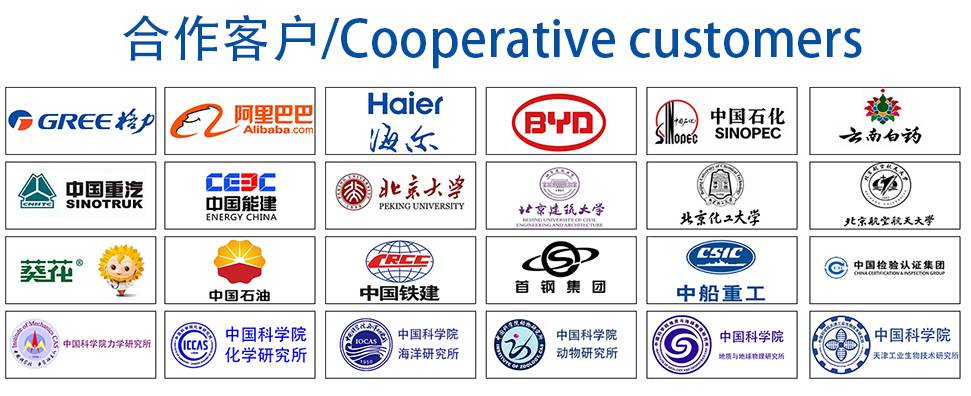