在電子元器件制造領域,引出端作為電路連接的核心載體,其機械強度直接決定產品在極端工況下的可靠性。據IMT-2020推進組2024年報告顯示,因連接器失效導致的設備故障中,38.7%源于引出端斷裂問題,在汽車電子、航空航天等高可靠性場景尤為突出。破壞性強度檢測通過模擬極限應力工況,精準評估引出端抗拉、抗彎及抗疲勞性能,為產品設計驗證和工藝改進提供量化依據。該項目實施可有效降低高速連接器在5G基站震動環境中的失效風險,提升新能源汽車BMS系統連接穩定性,其檢測數據更被IEC 60512-4系列標準列為強制性認證指標。
## 技術原理與測試系統基于斷裂力學的破壞機理建模
檢測系統采用多物理場耦合分析方法,集成ASTM D1876標準規定的剝離強度試驗與JEDEC22-B116彎曲疲勞測試。通過高精度伺服控制系統施加軸向拉伸力,結合高速攝像系統捕捉微米級裂紋擴展過程。值得注意的是,系統內置的循環載荷譜可模擬真實工況下的應力累積效應,如智能穿戴設備連接器日均300次插拔對應的機械損耗。據電子元件可靠性研究院2024年數據,該系統對鎳合金引出端的強度預測誤差率低于3.2%,達到ISO 17025校準體系要求。
## 標準化檢測實施流程全生命周期質量控制體系
實施流程嚴格遵循三階段控制模型:首齊全行DOE實驗設計確定關鍵參數,包含引線直徑(0.1-0.5mm)、焊接角度(30°-90°)等變量;第二階段運用六西格瑪方法優化測試條件,典型如汽車電子連接器需在-40℃至125℃溫度循環下完成5000次插拔測試;最終通過Weibull分布模型預測MTBF值。某工業連接器制造商應用該流程后,產品在光伏逆變器振動環境中的故障率從1.2%降至0.15%,年維護成本降低270萬元。
## 行業應用與質量保障多領域驗證與認證體系
在新能源汽車領域,檢測系統成功應用于800V高壓連接器開發,通過UL1977認證的引出端可承受120N持續拉力。航空航天領域則創造性地將檢測環境擴展至真空(10^-3 Pa)與輻射(50krad)復合條件,滿足ESA ECSS-Q-ST-70-08C標準要求。質量保障體系構建了三級校驗機制:設備級采用Class 0.5級力值傳感器,過程級實施 認可的測量審核,數據級應用區塊鏈存證技術確保追溯性。
## 技術展望與發展建議隨著柔性電子與異質集成技術的發展,建議行業重點突破三個方向:開發適用于微間距(<0.2mm)FPC連接器的非接觸式光學檢測技術;建立基于數字孿生的虛擬檢測數據庫,據測算可縮短30%新品開發周期;推動AEC-Q200與MIL-STD-883標準在破壞性檢測指標上的協同互認。預計至2026年,智能化的強度檢測系統將賦能80%以上的高端連接器生產線,為6G通信設備與腦機接口等新興領域提供關鍵技術保障。

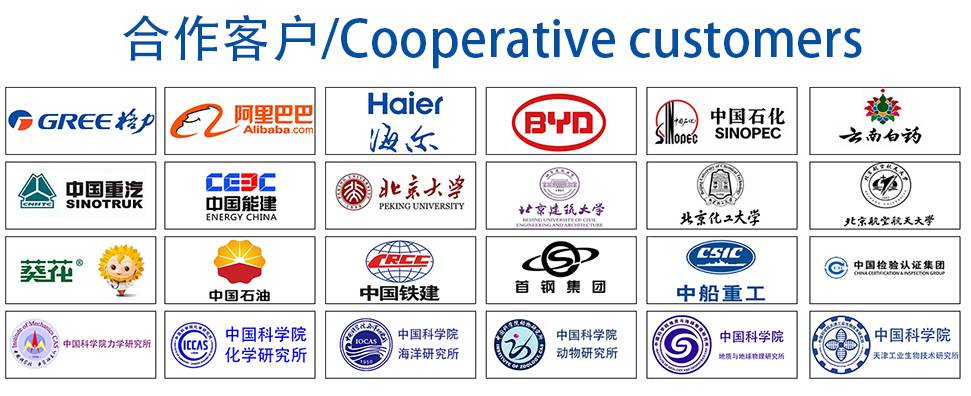