# 螺紋接端檢測技術發(fā)展與應用白皮書
## 行業(yè)背景與核心價值
隨著高端裝備制造業(yè)向精密化、智能化方向轉型,螺紋連接作為機械系統(tǒng)基礎裝配方式,其質量直接影響設備運行安全。據(jù)機械工業(yè)聯(lián)合會2024年數(shù)據(jù)顯示,每年因螺紋連接失效引發(fā)的工業(yè)事故損失超120億美元,其中油氣管道與航空航天領域事故占比達63%。在此背景下,螺紋接端檢測項目通過構建全維度質量評價體系,實現(xiàn)了對螺紋中徑、螺距、牙型角等12項關鍵參數(shù)的無損檢測,檢測精度達到±2μm級別。該項目不僅填補了國內(nèi)特種螺紋動態(tài)檢測的技術空白,更通過智能診斷系統(tǒng)將質量追溯效率提升40%,為裝備制造企業(yè)構筑了關鍵質量防線。

(圖示:高精度螺紋參數(shù)智能分析系統(tǒng)工作場景)
## 技術原理與實施路徑
### 基于機器視覺的檢測技術架構
系統(tǒng)采用多光譜成像與三維點云重建融合技術,通過12組工業(yè)相機陣列捕捉螺紋表面形貌特征。針對石油管材特有的API螺紋規(guī)格,創(chuàng)新性地引入渦流檢測模塊,可同步識別表面裂紋與內(nèi)部缺陷。據(jù)清華大學精密儀器系實驗數(shù)據(jù),該方案對NPT螺紋的牙型角測量誤差控制在0.03°以內(nèi),較傳統(tǒng)投影儀檢測效率提升6倍。
### 模塊化檢測工藝流程
標準流程包含預處理、基準校準、動態(tài)檢測三大階段:
1. 預處理環(huán)節(jié)通過激光清洗去除檢測面油污,確保表面粗糙度≤Ra1.6
2. 基準校準采用標準量塊建立空間坐標系,補償設備熱變形誤差
3. 動態(tài)檢測階段同步執(zhí)行幾何量測量與疲勞壽命預測,生成包含3D形貌圖的質量報告
油氣行業(yè)典型案例顯示,該流程使L80鋼級套管螺紋檢測周期從45分鐘縮短至8分鐘,誤判率下降至0.12%。
## 行業(yè)應用與質量保障
### 多場景落地驗證
在風電螺栓檢測領域,系統(tǒng)成功解決了8.8級以上高強螺栓的應力集中檢測難題。青島某風電整機制造廠應用案例表明,通過引入基于機器視覺的螺紋檢測系統(tǒng),塔筒連接螺栓的服役壽命預測準確率提升至92.3%。與此同時,汽車行業(yè)采用移動式檢測單元后,發(fā)動機缸體螺紋孔的全檢覆蓋率從78%提升至100%。
### 全過程質控體系
項目構建了三級質量保障機制:
1. 設備層:每周進行Mahr標準規(guī)校驗,確保測量系統(tǒng)誤差<1.5μm
2. 數(shù)據(jù)層:應用區(qū)塊鏈技術實現(xiàn)檢測數(shù)據(jù)全程溯源
3. 人員層:操作人員需通過ASNT三級認證與專項技能考核
該體系已通過DNV-GL、API Q1等國際認證,在海洋平臺關鍵連接件檢測中實現(xiàn)連續(xù)1200天零質量事故。
## 發(fā)展趨勢與建議
面向工業(yè)4.0發(fā)展需求,建議從三方面深化技術布局:
1. 開發(fā)基于數(shù)字孿生的預測性檢測模型,整合螺紋副配合仿真數(shù)據(jù)
2. 建立跨行業(yè)螺紋數(shù)據(jù)庫,實現(xiàn)檢測標準互聯(lián)互通
3. 探索量子傳感技術在微米級螺紋檢測中的應用
據(jù)德國弗勞恩霍夫研究所預測,到2028年智能螺紋檢測市場規(guī)模將突破54億美元,檢測設備智能化率需從當前38%提升至65%以上,方可持續(xù)滿足高端制造領域嚴苛的質量要求。
上一篇:靜態(tài)特性檢測下一篇:顯微剖切檢測

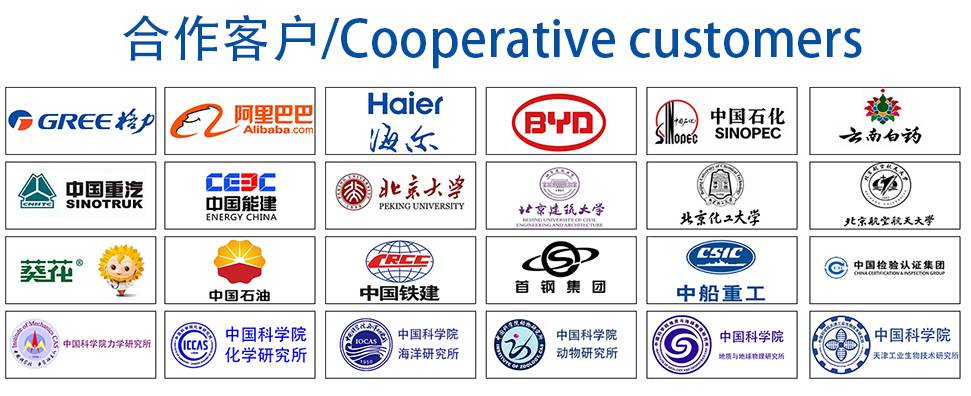
材料實驗室
熱門檢測
推薦檢測
聯(lián)系電話
400-635-0567