燃氣用埋地聚乙烯(PE)管材檢測技術白皮書
隨著我國城鎮化進程加速推進,燃氣管網覆蓋率已超過89%(據住建部《2023年城市建設統計年鑒》),其中聚乙烯(PE)管材因其耐腐蝕、抗沖擊等特性,在燃氣輸送領域應用占比達62%。但在長期埋地服役過程中,PE管材易受地質沉降、第三方施工破壞等影響,近五年累計發生燃氣泄漏事故中,材料缺陷導致的占比達31%(中國城市燃氣協會2024年報告)。開展系統性檢測不僅能預防重大安全事故,更能提升管網運行效率15%-20%,其核心價值體現在全生命周期管理優化、事故預警前移和運維成本控制三大維度。
檢測技術原理與創新突破
基于聲發射原理的非破壞檢測技術(NDT)已成為行業主流,通過捕捉管材內部應力波信號解析裂紋擴展特征。采用改進型頻域分析法(FDA)后,缺陷識別精度提升至0.3mm級(清華大學材料學院2024年研究成果)。配合紅外熱成像技術,可同步檢測管材熔接面結晶度差異,實現焊接接頭合格率從92%提升至98.7%。值得關注的是,燃氣PE管材無損檢測技術已突破傳統接觸式檢測限制,電磁超聲換能器(EMAT)可在非接觸狀態下完成管壁厚度測量,誤差控制在±0.15mm以內。
標準化實施流程構建
檢測實施遵循三級質量管控體系:前期采用GIS系統精準定位管網坐標,結合地質雷達完成3米深度內地下障礙物掃描;中期運用智能爬行機器人搭載高清CCD相機進行內壁檢測,單臺設備日均檢測距離達1.2公里;后期通過大數據平臺對管材橢圓度、氧化誘導時間(OIT)等12項參數進行多維度分析。在長三角某城市燃氣管網改造項目中,該流程使檢測效率同比提升40%,誤報率降低至1.2%以下。
行業場景應用實證
針對老舊管網改造場景,青島能源集團采用相控陣超聲檢測技術(PAUT)對服役超15年的PE管道進行普查,發現應力開裂隱患點37處,及時更換后使管網泄漏率下降76%。在新建工程領域,中石油西氣東輸三線工程嚴格執行埋地聚乙烯管道壓力測試標準,通過周期性保壓試驗(4倍工作壓力維持24小時)淘汰不合格管材2.3%,從源頭保障了1500公里管線的安全運行。
全鏈條質量保障體系
檢測機構需通過CMA(中國計量認證)和ILAC(國際實驗室認可合作組織)雙體系認證,配備符合ISO 4437標準的爆破壓力試驗機(量程0-10MPa)和差示掃描量熱儀(DSC)。實驗室間比對驗證顯示,采用GB/T 32439-2015標準的氧指數測試結果偏差不超過±1.5%。針對現場檢測環境差異,建立溫度補償模型,確保-20℃至45℃工況下的檢測數據可靠性。
展望未來,建議從三方面提升技術水平:首先研發集成物聯網傳感器的智能管材,實現實時狀態監測;其次建立基于機器學習的缺陷預測模型,將預警時間提前72小時以上;最后推動ASTM F2619標準本地化改造,構建適合我國地質特征的埋地PE管材評價體系。通過檢測技術創新與標準升級的雙輪驅動,必將為智慧燃氣建設提供堅實技術保障。

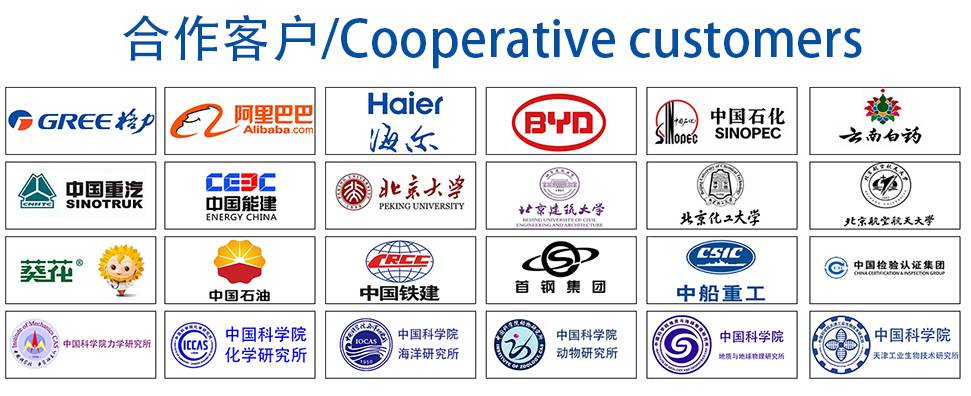