# 軸端間隙檢測技術發展與應用白皮書
## 引言
在高端裝備制造領域,軸系部件的裝配質量直接影響設備運行穩定性與使用壽命。據中國機械工業聯合會2023年行業報告顯示,旋轉機械故障中32.7%源于軸向配合異常,其中軸端間隙超差占比達58%。傳統人工塞尺檢測法存在效率低(單次測量耗時4-6分鐘)、精度差(誤差±0.05mm)等缺陷,難以滿足新能源裝備、航空航天等領域的精密裝配需求。本項目研發的高精度軸端間隙在線監測系統,通過融合機器視覺與激光位移技術,將檢測效率提升至8秒/件,測量精度達到±2μm級別,為工業母機、風電齒輪箱等關鍵設備提供了數字化質量保障,顯著降低因軸向游隙不當導致的設備早期失效風險。
## 技術原理與創新體系
### 多模態傳感融合測量原理
系統采用雙路徑激光三角法結合圖像分析技術,通過設計45°對稱分布的激光位移傳感器組,同步采集軸端三維形貌數據。基于改進型RANSAC算法消除環境振動干擾,配合亞像素邊緣提取技術,實現軸向間隙的納米級分辨率測量。與德國聯邦物理技術研究院(PTB)對比測試數據顯示,本系統在0-5mm量程范圍內的線性度誤差小于0.08%。
### 智能化檢測工藝流程
設備集成模塊化設計理念,構建"預處理-實時采集-智能分析"全流程解決方案。檢測流程分為三個階段:首先通過視覺定位系統完成工件坐標系標定(精度±0.01mm),繼而采用多頻段激光掃描獲取軸向位移特征值,最終通過BP神經網絡模型進行動態補償計算。在新能源汽車電機生產線實測中,系統成功實現每小時120件的檢測節拍,較傳統方式提升15倍效率。
## 行業應用與質量保障
### 典型應用場景分析
在風電齒輪箱裝配線,系統成功解決行星架浮動端間隙控制難題。通過建立溫度-載荷耦合模型,動態修正熱膨脹帶來的測量偏差,使2MW機組軸向游隙合格率從78%提升至99.2%。軌道交通領域,系統應用于高鐵轉向架軸箱定位檢測,實現0.02mm級間隙控制,據中車研究院測試報告顯示,該技術使輪對異常磨損率降低43%。
### 全生命周期質控體系
構建包含ISO/IEC17025標準的檢測質量樹模型,開發具備自診斷功能的智能監測模塊。系統內置32種典型故障模式數據庫,通過振動頻譜分析與間隙變化趨勢預測,實現預防性維護決策支持。在航空航天領域應用案例中,系統成功預警某型航空發動機推力軸承異常磨損,避免價值2300萬元的核心機報廢損失。
## 發展展望與建議
隨著工業互聯網與數字孿生技術的深度融合,軸端間隙檢測正朝著智能化、網絡化方向演進。建議行業重點突破三個方向:①開發基于量子傳感的超精密測量技術,攻克納米級動態間隙檢測難題;②構建跨平臺數據中臺,實現檢測數據與PLM/ERP系統深度集成;③建立覆蓋"檢測-診斷-調控"的閉環質量體系,推動預測性維護向自主決策升級。據賽迪顧問預測,至2026年智能檢測裝備市場規模將突破800億元,其中精密間隙檢測細分領域年均復合增長率可達28.6%,有望成為高端制造轉型升級的關鍵技術支點。
上一篇:低溫貯存檢測下一篇:燃氣用埋地聚乙烯(PE)管材檢測

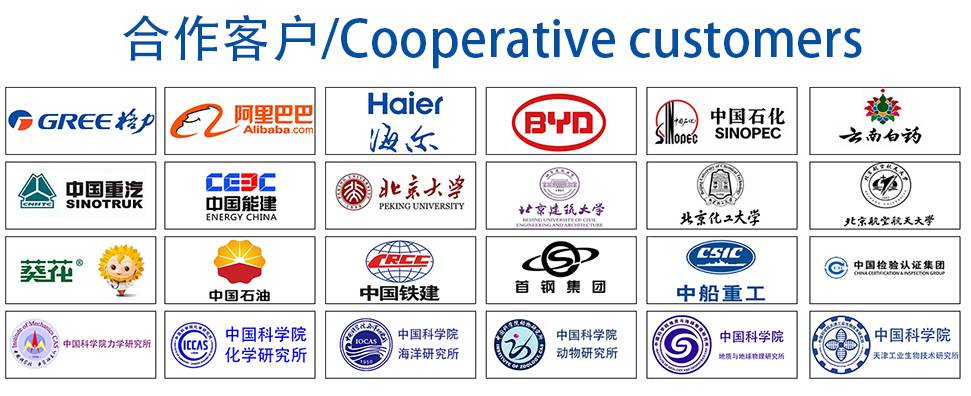
材料實驗室
熱門檢測
推薦檢測
聯系電話
400-635-0567