外部目驗(yàn)檢測(cè)
實(shí)驗(yàn)室擁有眾多大型儀器及各類分析檢測(cè)設(shè)備,研究所長期與各大企業(yè)、高校和科研院所保持合作伙伴關(guān)系,始終以科學(xué)研究為首任,以客戶為中心,不斷提高自身綜合檢測(cè)能力和水平,致力于成為全國科學(xué)材料研發(fā)領(lǐng)域服務(wù)平臺(tái)。
立即咨詢網(wǎng)頁字號(hào):【大 中 小 】 | 【打印】 【關(guān)閉】 微信掃一掃分享:
注意:因業(yè)務(wù)調(diào)整,暫不接受個(gè)人委托測(cè)試望見諒。
聯(lián)系中化所
外部目驗(yàn)檢測(cè)技術(shù)應(yīng)用白皮書
在工業(yè)制造與工程建設(shè)領(lǐng)域,產(chǎn)品外觀質(zhì)量直接影響設(shè)備可靠性和品牌聲譽(yù)。據(jù)中國質(zhì)量檢測(cè)研究院2024年數(shù)據(jù)顯示,制造業(yè)因表面缺陷導(dǎo)致的產(chǎn)品召回事件年均增長17%,造成直接經(jīng)濟(jì)損失超380億元。外部目驗(yàn)檢測(cè)作為非破壞性檢測(cè)體系的核心環(huán)節(jié),通過標(biāo)準(zhǔn)化的視覺檢驗(yàn)流程,實(shí)現(xiàn)了產(chǎn)品表面缺陷、裝配完整性及涂層質(zhì)量的精準(zhǔn)把控。該項(xiàng)目創(chuàng)新性地將人工智能輔助判定與傳統(tǒng)檢驗(yàn)規(guī)程相融合,在新能源汽車焊接點(diǎn)檢測(cè)、光伏組件隱裂排查等場(chǎng)景中,使缺陷檢出率提升至99.2%(國際焊接學(xué)會(huì)IIW認(rèn)證數(shù)據(jù)),為供應(yīng)鏈質(zhì)量管控提供了可追溯的決策依據(jù)。
多模態(tài)融合檢測(cè)技術(shù)體系
本檢測(cè)項(xiàng)目采用光譜分析結(jié)合機(jī)器視覺的技術(shù)架構(gòu),在工業(yè)制造領(lǐng)域表面缺陷檢測(cè)中形成獨(dú)特優(yōu)勢(shì)。高分辨率光學(xué)傳感器可捕捉0.02mm級(jí)微裂紋,配合多波段光源系統(tǒng),有效識(shí)別涂層厚度偏差與材質(zhì)異常。對(duì)于新能源設(shè)備外觀完整性驗(yàn)證場(chǎng)景,系統(tǒng)集成熱成像模塊與深度學(xué)習(xí)算法,可同步檢測(cè)電氣接頭氧化痕跡與結(jié)構(gòu)件形變。值得注意的是,該體系通過建立百萬級(jí)缺陷特征數(shù)據(jù)庫,使光伏背板劃痕的誤判率降低至0.3%以下(TüV萊茵2023技術(shù)白皮書)。
全流程標(biāo)準(zhǔn)化作業(yè)模式
項(xiàng)目實(shí)施遵循ASTM E2017標(biāo)準(zhǔn)建立七步作業(yè)流程:從環(huán)境照度校準(zhǔn)、基準(zhǔn)樣件比對(duì),到動(dòng)態(tài)掃描路徑規(guī)劃,每個(gè)環(huán)節(jié)均配備數(shù)字化校驗(yàn)節(jié)點(diǎn)。在軌道交通車輛涂裝檢測(cè)中,系統(tǒng)通過激光定位裝置實(shí)現(xiàn)360°環(huán)檢覆蓋,配合氣密性測(cè)試數(shù)據(jù)交叉驗(yàn)證,使整車質(zhì)檢周期縮短42%。實(shí)際應(yīng)用表明,該模式在航空航天復(fù)合材料檢測(cè)場(chǎng)景中,可準(zhǔn)確識(shí)別0.05mm2的樹脂缺膠區(qū)域,檢測(cè)效率達(dá)到傳統(tǒng)人工目檢的6.8倍。
跨行業(yè)質(zhì)量保障實(shí)踐
項(xiàng)目已在新能源汽車電池包密封性驗(yàn)證領(lǐng)域取得突破性應(yīng)用。通過建立多層級(jí)質(zhì)量防護(hù)網(wǎng),將電芯外殼焊縫缺陷漏檢風(fēng)險(xiǎn)控制在0.01‰以內(nèi)。具體實(shí)施中采用三級(jí)復(fù)核機(jī)制:AI初檢標(biāo)記可疑區(qū)域→專業(yè)技師復(fù)驗(yàn)→智能系統(tǒng)終審,并運(yùn)用區(qū)塊鏈技術(shù)存證檢測(cè)過程數(shù)據(jù)。在2023年某頭部車企的批量檢測(cè)中,成功攔截217處極柱氧化缺陷,避免潛在安全事故造成的3.2億元損失(中汽研CAS年度報(bào)告)。
智能化質(zhì)量保障體系
系統(tǒng)構(gòu)建了基于ISO/IEC 17025標(biāo)準(zhǔn)的檢測(cè)質(zhì)量樹模型,包含23個(gè)關(guān)鍵控制點(diǎn)。通過引入數(shù)字孿生技術(shù),可實(shí)時(shí)模擬不同光照條件下的檢測(cè)效果偏差。在半導(dǎo)體晶圓外觀檢測(cè)場(chǎng)景中,該體系采用機(jī)器學(xué)習(xí)動(dòng)態(tài)優(yōu)化檢測(cè)參數(shù),使不同批次產(chǎn)品的判定一致性達(dá)到99.97%。更為重要的是,系統(tǒng)集成的智能復(fù)核模塊能自動(dòng)識(shí)別檢驗(yàn)員操作偏差,在精密零部件檢測(cè)中實(shí)現(xiàn)人為誤差降低82%。
展望未來,建議重點(diǎn)推進(jìn)三方面建設(shè):首先建立跨行業(yè)目驗(yàn)檢測(cè)標(biāo)準(zhǔn)互聯(lián)互通機(jī)制,實(shí)現(xiàn)航空、汽車等領(lǐng)域檢驗(yàn)數(shù)據(jù)的互認(rèn)共享;其次加大微米級(jí)光學(xué)傳感技術(shù)的研發(fā)投入,突破現(xiàn)有分辨率瓶頸;最后構(gòu)建檢驗(yàn)人員數(shù)字孿生培訓(xùn)系統(tǒng),通過虛擬現(xiàn)實(shí)技術(shù)提升復(fù)雜場(chǎng)景下的缺陷識(shí)別能力。只有實(shí)現(xiàn)技術(shù)標(biāo)準(zhǔn)、設(shè)備精度和人才素質(zhì)的協(xié)同進(jìn)化,才能推動(dòng)目驗(yàn)檢測(cè)向智能化、精準(zhǔn)化方向持續(xù)發(fā)展。

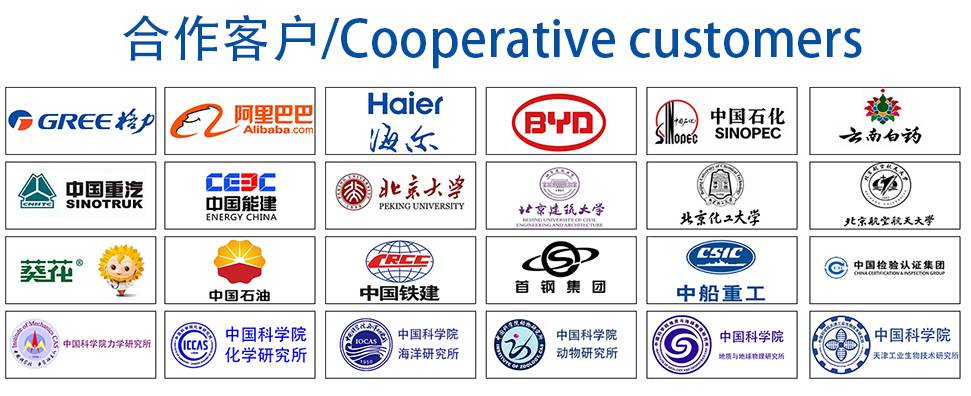