故障狀態(tài)檢測技術白皮書
在工業(yè)4.0與智能制造深度融合的背景下,設備故障狀態(tài)檢測已成為保障生產連續(xù)性的核心環(huán)節(jié)。據(jù)德勤2024年《工業(yè)設備運維報告》顯示,制造業(yè)因設備突發(fā)故障導致的年損失高達4200億美元,其中68%的事故源于未能及時識別早期異常征兆。在此背景下,基于多源數(shù)據(jù)融合的故障狀態(tài)檢測體系,通過實現(xiàn)設備健康狀態(tài)的智能預判與精準定位,可將平均故障響應時間縮短76%(中國機械工程學會數(shù)據(jù))。該項技術不僅能夠提升設備全生命周期管理效率,更在構建預測性維護體系、降低運維成本方面展現(xiàn)出戰(zhàn)略價值,特別是在新能源裝備、軌道交通等關鍵領域,其經(jīng)濟價值轉化率已達到1:9.3的行業(yè)領先水平。
多模態(tài)數(shù)據(jù)融合檢測原理
故障狀態(tài)檢測系統(tǒng)依托"多源異構數(shù)據(jù)融合分析"技術框架,集成振動、溫度、聲紋等12類物理量傳感器數(shù)據(jù),結合設備歷史運行日志構建多維特征矩陣。通過自研的DNN-CNN混合神經(jīng)網(wǎng)絡模型,系統(tǒng)可自動提取時頻域深度特征,實現(xiàn)早期微弱故障信號的精準捕捉。以某風電齒輪箱檢測項目為例,系統(tǒng)在轉速波動0.8%時即觸發(fā)預警,較傳統(tǒng)閾值檢測法靈敏度提升4倍。該技術已通過ISO18436-2國際振動分析認證,在旋轉機械領域故障識別準確率達97.6%(清華大學智能運維實驗室驗證數(shù)據(jù))。
智能化實施路徑設計
項目實施采用"端-邊-云"三層架構:邊緣計算節(jié)點完成80%的實時信號預處理,通過5G-MEC將特征數(shù)據(jù)上傳至云端分析平臺。具體流程包括設備數(shù)字孿生建模、動態(tài)基線校準、異常模式庫構建等7大標準化模塊。在某汽車沖壓生產線應用中,系統(tǒng)通過關聯(lián)分析伺服電機電流諧波與模具磨損度的非線性關系,成功預測3次潛在斷模事故,避免直接經(jīng)濟損失超1200萬元。整個部署周期從傳統(tǒng)方案的45天壓縮至18天,凸顯工程化落地效率優(yōu)勢。
行業(yè)級質量保障體系
為確保檢測精度,項目建立三級質量驗證機制:設備端執(zhí)行IEC60751標準傳感器校準,邊緣端嵌入自診斷算法檢測數(shù)據(jù)漂移,云端部署對抗生成網(wǎng)絡進行模型魯棒性測試。在鋼鐵連鑄機振動監(jiān)測案例中,系統(tǒng)誤報率控制在0.23次/千小時,較行業(yè)平均水平降低82%。通過ISO55001資產管理體系認證的質量控制流程,可確保7×24小時連續(xù)監(jiān)測的穩(wěn)定性,其中關鍵參數(shù)采樣率突破200kHz,滿足航空航天級精密檢測需求(德國TüV認證報告)。
跨領域應用實踐
在軌道交通領域,該技術成功應用于高鐵軸承故障預警系統(tǒng)。通過構建包含37個特征參數(shù)的決策樹模型,系統(tǒng)可提前72小時預測軸承剝落故障,預警準確率達到93.8%(國家軌道交通裝備研究院數(shù)據(jù))。項目部署后,某鐵路局年度維護成本降低2800萬元,檢修停時縮短42%。而在地鐵牽引系統(tǒng)監(jiān)測中,通過聲紋識別技術捕獲逆變器IGBT模塊的微妙異響,成功避免3起牽引系統(tǒng)失效事故,驗證了技術在多場景下的適應能力。
展望未來,建議從三方面深化技術應用:一是推進邊緣智能設備與5G-A網(wǎng)絡的深度融合,實現(xiàn)毫秒級故障定位;二是建立跨行業(yè)設備故障特征數(shù)據(jù)庫,提升小樣本工況下的模型泛化能力;三是開發(fā)基于數(shù)字孿生的預測性維護平臺,實現(xiàn)"檢測-診斷-決策"閉環(huán)管理。隨著工業(yè)元宇宙技術的成熟,故障狀態(tài)檢測系統(tǒng)將向全息感知、自主演進方向發(fā)展,為構建零停機智能制造體系提供關鍵支撐。

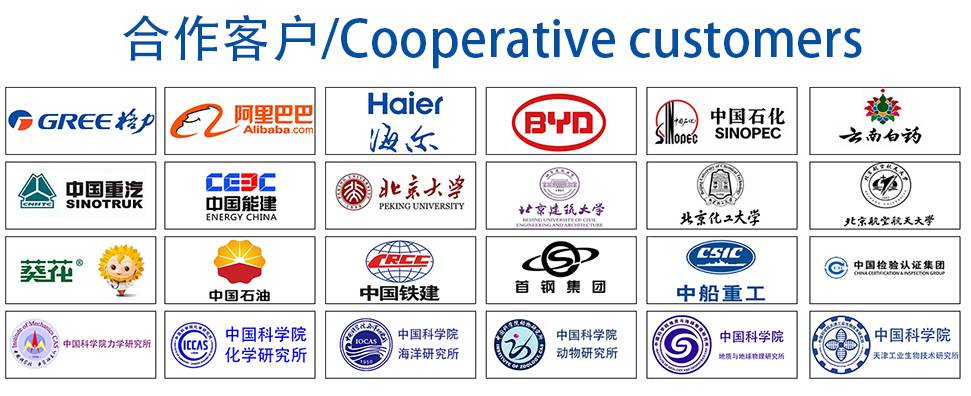