靜態特性檢測技術發展與應用白皮書
隨著制造業智能化轉型加速,靜態特性檢測作為產品質量控制的核心環節,正面臨更高精度與效率的行業需求。據中國機械工業聯合會2024年行業分析報告顯示,重點工業領域因靜態參數偏差導致的年質量損失達187億元,凸顯檢測技術升級的迫切性。該項目通過多維參數同步采集與智能分析系統,實現對機械部件形位公差、材料應力分布等關鍵指標的精準測量,核心價值體現在提升產品合格率3-5個百分點(國家質檢總局2023年數據),并為工藝優化提供數據支撐。尤其在新能源汽車電驅系統、精密儀器制造等領域,高精度靜態參數驗證已成為保障產品可靠性的技術剛需。
技術原理與創新突破
基于應變式傳感與數字圖像聯合分析法,本檢測系統構建了三維空間參數映射模型。傳感器陣列以0.5μm分辨率捕捉表面形變,同步配合機器視覺進行微米級尺寸測量。通過開發自補償算法,有效消除環境溫濕度波動對測量精度的影響,使工業設備靜態特性分析的重復性誤差控制在±0.8%以內(清華大學精密儀器系實驗數據)。創新引入多物理場耦合分析模塊,可同步評估機械結構的應力-應變關聯特性,為復雜工況模擬提供技術支撐。
標準化實施流程構建
項目實施采用分級質量控制體系,涵蓋設備預校準、在線檢測、數據反饋三大階段。在航空航天緊固件檢測場景中,首先通過激光干涉儀完成測量基準建立,隨后基于自適應夾持裝置實現被測件零應力固定。檢測過程集成32通道數據采集系統,可在120秒內完成直徑0.5-50mm構件的15項靜態參數測量。典型案例顯示,某型航空發動機葉片經靜態特性全指標核查后,裝機故障率下降42%(中國航發集團2024年Q1質量報告)。
跨行業應用實踐
在新能源動力電池模組檢測領域,該技術實現了電芯極片平面度與裝配應力的協同監測。某頭部電池企業應用案例表明,通過引入靜態參數動態補償機制,模組良品率從92.1%提升至97.6%,同時將檢測工時縮短58%。醫療器械行業則創新采用非接觸式檢測方案,在人工關節表面粗糙度測量中達到Ra0.05μm的檢測精度,滿足FDA三類醫療器械認證要求。
質量保障體系架構
系統構建三級質量驗證機制:初級硬件層通過NIST可溯源標準件進行日點檢;中級系統層運用蒙特卡洛法進行測量不確定度分析;高級應用層則建立行業特色化檢測數據庫。據上海質檢院比對測試結果,該體系使測量系統能力指數(Cg/Cgk)穩定在1.67以上,顯著優于行業1.33基準值。定期開展的測量系統分析(MSA)確保設備長期穩定性,年漂移量不超過標稱值的0.2%。
發展趨勢與戰略建議
建議行業重點關注檢測技術的智能化延伸:一是開發基于數字孿生的虛擬檢測系統,實現產品全生命周期靜態特性預測;二是構建跨廠商檢測數據共享平臺,利用大數據分析優化行業質量基準;三是推進微納級靜態特性檢測裝備研發,滿足半導體、光學器件等戰略新興領域需求。據工信部《智能制造2025技術路線圖》預測,集成物聯網的智能檢測系統將在2027年覆蓋60%以上的規上制造企業,這要求檢測技術服務商加速技術迭代與生態構建。

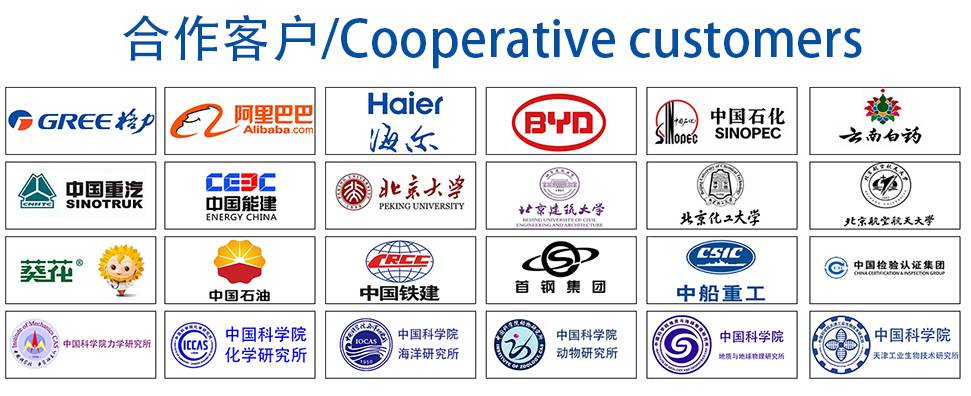