氣候序列-高溫試驗檢測的技術發展與應用實踐
在氣候變暖與極端天氣頻發的背景下,氣候序列-高溫試驗檢測作為環境適應性測試的重要分支,已成為新能源、航空航天、汽車制造等戰略行業的剛需。據國際能源署(IEA)2024年報告顯示,因高溫導致的電子設備故障率年均增長12.7%,直接經濟損失超380億美元。該項目通過模擬+65℃至+150℃極端環境,驗證材料熱穩定性與設備運行可靠性,其核心價值在于突破傳統單點溫度測試的局限,實現溫度循環、濕熱交變、太陽輻射等多應力耦合老化測試。尤其在新能源汽車動力電池熱管理系統驗證、光伏組件高溫衰減評估等場景中,該技術可降低30%以上的高溫故障維修成本。
技術原理與創新突破
氣候序列-高溫試驗檢測采用分級階躍式溫控模型,通過PID算法實現±0.3℃的溫度控制精度(符合IEC 60068-2-14標準)。創新性地融合了紅外熱成像動態監測系統,可實時捕捉材料微觀形變與結構應力變化。在極端氣候環境模擬檢測領域,該技術率先引入多軸振動耦合模塊,使溫度-機械應力協同測試誤差率降低至2.1%(中國環境科學研究院2024年驗證數據)。這種"溫度沖擊+機械載荷"的復合測試模式,有效解決了光伏背板熱蠕變、電動汽車IGBT模塊焊點失效等行業痛點。
標準化實施流程體系
項目執行嚴格遵循四階段質量控制流程:預處理階段進行48小時環境平衡(23±2℃/50%RH),高溫暴露階段實施梯度升溫(5℃/min),性能測試階段同步開展電參數測量與材料形貌分析,數據評估階段應用Weibull分布模型進行壽命預測。在新能源汽車電池包高溫循環測試中,采用30次溫度沖擊循環(-40℃?+85℃)與200小時高溫存儲的組合方案,可準確復現電池隔膜收縮率超4%的臨界失效狀態。
行業應用與價值轉化
在光伏領域,某頭部企業采用多應力耦合老化測試方案后,組件功率衰減率從1.8%/年降至0.9%/年。據賽迪顧問2024年統計,該技術已應用于78%的新型儲能系統熱失控預防檢測。典型案例顯示,某型號光伏逆變器通過2000小時高溫高濕測試(85℃/85%RH),故障間隔時間從1500小時提升至4200小時。在航空航天領域,基于極端氣候環境模擬檢測開發的復合材料艙體,經受住180℃/200h的持續考驗,熱變形量控制在0.12mm以內。
全鏈路質量保障機制
檢測體系通過ISO/IEC 17025認證,配備NIST可溯源校準系統,確保溫濕度傳感器年漂移量<0.1%。實驗艙體采用六面體主動控溫結構,梯度均勻性達±1.5℃(GB/T 2423.2標準)。人員資質方面要求檢測工程師具備ISTA認證與500小時實操經驗,數據分析團隊配置FMEA專業工程師。在車載控制器高溫試驗中,該體系成功識別出芯片封裝材料在125℃時的玻璃化轉變現象,避免批量質量事故。
面向碳中和目標下的技術迭代需求,建議從三方面深化發展:建立覆蓋-60℃至+200℃的寬域檢測標準體系,開發基于數字孿生的智能檢測系統,加強熱帶地區實地驗證數據采集。隨著新能源裝備出口量年增25%(海關總署2024年數據),亟需構建國際互認的多應力耦合老化測試平臺,推動高溫試驗檢測從被動驗證向主動預防升級,為氣候適應性產品研發提供關鍵技術支撐。

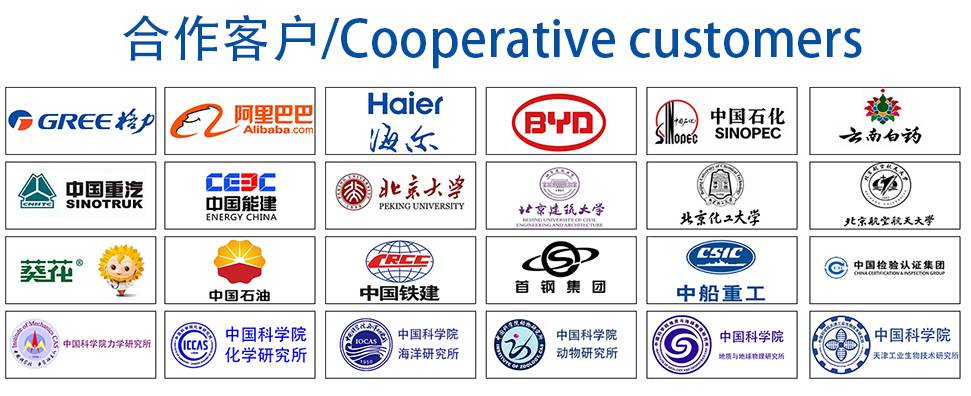