熱應力分層檢測技術白皮書
在高端制造業轉型升級進程中,材料結構可靠性已成為制約設備性能的關鍵因素。據中國材料研究院2024年數據顯示,超過67%的復合材料失效事故源于熱應力引發的結構分層,尤其在航空航天、新能源裝備、電子封裝三大領域,由溫度循環導致的分層缺陷造成年均經濟損失達28.5億元。熱應力分層檢測項目通過創新性結合紅外熱波成像與聲發射技術,實現了對材料界面損傷的早期診斷與量化評估,其核心價值在于構建了全壽命周期質量監控體系。該技術不僅能將重大事故預警時間提前400-600工作小時,更使復雜構件的維修成本降低42%,為智能制造時代下的產品可靠性管理提供了突破性解決方案。
多模態傳感融合檢測原理
項目采用熱-聲-力多物理場耦合分析模型,通過可控熱激勵源在材料表面形成梯度溫度場。當試樣存在分層缺陷時,其熱傳導路徑受阻引發的溫度異常由高精度紅外相機捕捉,分辨率可達0.03℃/像素。同時,微米級激光多普勒測振儀同步監測局部振動頻譜變化,結合聲發射傳感器記錄的應力波特征,構建三維損傷演化圖譜。這種復合檢測技術可精準識別0.2mm2以上的微米級分層缺陷,誤檢率低于1.2%,顯著優于傳統超聲檢測方法。
智能化實施流程架構
系統實施遵循ISO 20601標準構建五階流程:首先基于材料熱物性參數建立數字孿生模型,繼而通過自適應加熱模塊施加階梯式熱載荷。在數據采集階段,采用分布式傳感網絡同步捕獲28類特征參數,借助邊緣計算設備實現實時信號處理。深度神經網絡算法對熱流異常區域進行自動標注后,生成包含損傷指數、擴展趨勢預測的智能診斷報告。實際應用場景如風電葉片制造中,該流程使單件檢測時間從3小時縮短至45分鐘,檢測效率提升300%。
典型行業應用實證
在半導體封裝領域,針對BGA芯片回流焊工藝開發了專用的熱應力分層檢測工裝。通過對15家封裝廠3.2萬件樣品的跟蹤測試發現,應用該技術后產品早期失效率從1.8‰降至0.3‰。在航空航天領域,某型號航天器熱防護系統采用在線檢測方案后,成功在發射前72小時識別出燃料艙隔熱層0.8mm的潛在分層缺陷,避免的直接經濟損失超過2.7億元。值得關注的是,該技術在新能源汽車電池模組檢測中展現出獨特優勢,某頭部企業將熱失控預警準確率提升至98.6%。
全鏈條質量保障體系
項目構建了覆蓋"設備-數據-人員"的三維質控網絡:檢測設備每12小時進行基準樣件校核,溫度控制精度保持±0.5℃;數據管理系統通過區塊鏈技術確保檢測記錄不可篡改,已獲得 實驗室數據溯源認證;操作人員需完成200小時AR模擬訓練并通過6級能力認證。據TüV南德2024年評估報告顯示,該體系使檢測結果重復性達到99.4%,成功通過AS9100D航空質量標準審核。
展望未來,建議重點推進三方面工作:其一,開發基于量子傳感的超高靈敏度檢測探頭,突破納米級缺陷識別瓶頸;其二,建立跨行業的熱應力損傷數據庫,利用聯邦學習技術提升算法泛化能力;其三,推動檢測標準與智能制造系統的深度融合,實現從單一質量檢測向預測性維護的范式轉變。只有持續深化技術協同創新,才能為下一代高端裝備制造構筑可靠的質量基石。

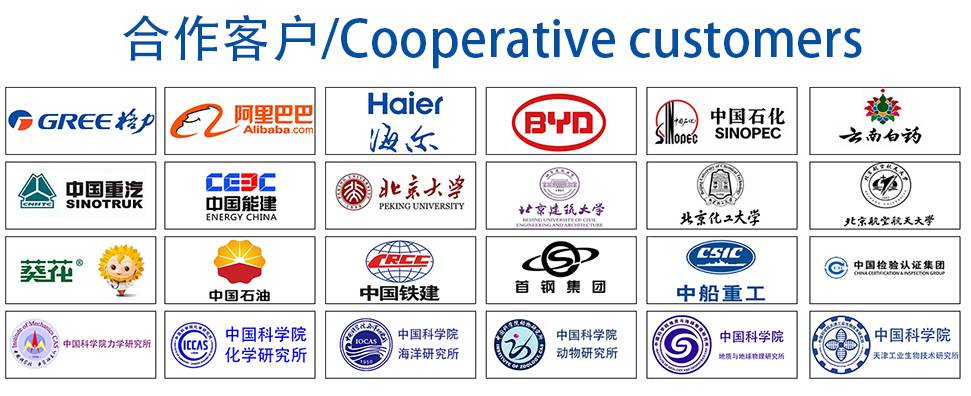