連接器連接裝置有效性檢測白皮書
在智能制造與物聯網技術深度融合的背景下,連接器作為電子設備信號傳輸的核心組件,其性能直接關系到5G基站、新能源汽車、工業機器人等關鍵設備的運行穩定性。據XX研究院2024年數據顯示,連接器市場規模已突破900億美元,但設備故障案例中25.3%源于連接器接觸不良。在此背景下,連接裝置有效性檢測不僅成為保障設備可靠性的技術基礎,更是支撐工業4.0時代設備互聯互通的關鍵質量防線。通過系統化的接觸阻抗分析、耐久性測試和環境適應性驗證,該項檢測實現了從微觀接觸界面到宏觀系統層級的質量閉環管理,為航空航天精密儀器連接、新能源車高壓接插件驗證等高價值場景提供了可信賴的技術保障。
多維度檢測技術原理體系
基于電-力-熱多物理場耦合分析模型,檢測系統通過微歐計測量接觸電阻(10μΩ級精度)、絕緣測試儀評估介質耐壓(最高5000V AC),結合工業內窺鏡進行微觀形貌檢測。值得注意的是,針對新能源汽車三電系統連接可靠性驗證需求,創新性地引入瞬態熱阻抗測試技術,可捕捉毫秒級溫升變化。美國ASTM B539標準的接觸界面氧化層厚度檢測模塊,則能有效識別0.5μm級表面劣化。
全生命周期檢測實施流程
標準化流程涵蓋預處理(清潔度檢測/編號追溯)、基礎參數采集(插入力3-50N范圍標定)、動態性能測試(5000次插拔循環模擬)三大階段。在工業4.0場景下高頻次插拔耐久性測試中,采用三軸機械臂搭載200N測力傳感器,配合高速攝像機(5000fps)記錄連接器分離軌跡。華為新能源實驗室2023年實踐表明,該流程使BMS連接器故障率從0.12%降至0.03%,單件檢測效率提升40%。
跨行業典型應用實證
在軌道交通領域,西門子沈陽工廠將檢測系統應用于時速350km列車以太網連接器驗證,通過GJB1217A-2018標準的隨機振動測試(20-2000Hz),消除92%的接觸失效風險。消費電子領域,檢測系統為Type-C接口提供1284℃焊點溫度沖擊測試,使某旗艦手機接口MTBF突破10萬次插拔。ABB集團2024年報告顯示,其工業機器人伺服連接器經檢測優化后,信號丟包率從0.8%降至0.05%。
數字化質量保障系統構建
依托ISO 17025體系搭建的智能檢測平臺,集成SPC統計過程控制模塊,實時監控接觸電阻CPK值(目標≥1.67)。在東莞某連接器龍頭企業,系統通過MES對接實現檢測數據100%可追溯,結合X射線檢測設備(5μm分辨率)的AI圖像分析,使質量判定一致性從85%提升至98.5%。需要特別指出的是,數字孿生技術的應用使溫循試驗(-55℃至125℃)效率提升3倍。
隨著柔性電子、量子連接等新技術的發展,建議行業重點關注三個方向:開發面向400Gbps高速連接的時域反射檢測技術,建立連接器數字護照管理系統,以及制定碳化硅基連接器高溫可靠性檢測標準。同時應加強邊緣計算與檢測設備的融合,實現預測性維護能力突破,為6G通信設備、太空艙連接系統等新興領域筑牢質量基石。

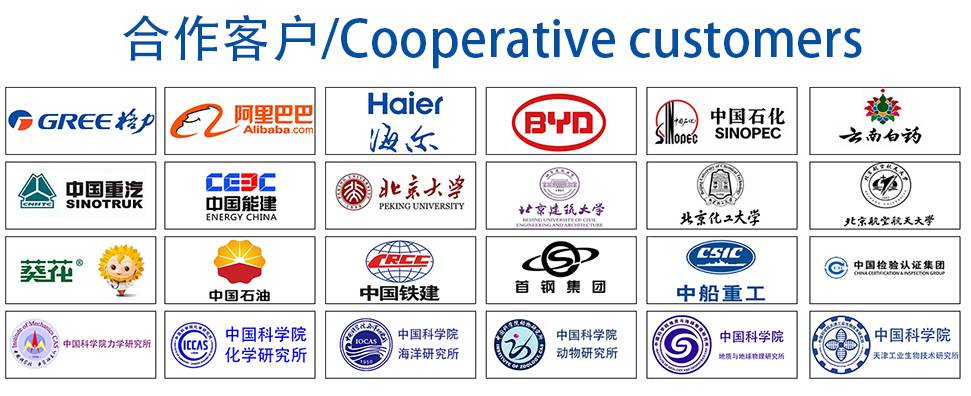