# 一般技術要求檢測體系的創新實踐與發展路徑
## 行業背景與核心價值
隨著制造業數字化轉型加速,產品技術規范復雜度以年均12%的速度遞增(中國質量協會2024年藍皮書)。在此背景下,一般技術要求檢測作為產品質量的基石性保障手段,正從傳統的單一參數驗證向多維度系統化評估演進。該項目通過建立覆蓋設計驗證、生產控制、成品檢驗的全生命周期檢測體系,可將產品早期缺陷識別率提升至98.5%(國家工業信息安全發展研究中心2024年評估數據)。核心價值在于構建了可量化的技術合規性評價模型,特別是在新能源汽車關鍵零部件、智能終端設備等戰略領域,成功將行業平均質量事故率降低了37%。

## 技術原理與創新突破
### 多模態檢測技術融合
基于多傳感器融合架構,結合機器視覺(0.02mm級精度)、聲發射檢測(20-200kHz頻段覆蓋)與熱成像技術(±0.5℃靈敏度),實現了對產品物理特性、功能參數和隱性缺陷的立體化檢測。其中,動態應力分析模塊采用改進型有限元算法,將仿真精度提升至95%置信區間,成功應用于航空緊固件疲勞壽命預測場景。
### 智能化檢測流程再造
項目組研發的智能決策系統(IDS)整合了23類行業檢測標準庫,通過特征值匹配引擎實現檢測項目的動態配置。在某精密軸承制造企業的實踐中,該系統將檢測方案生成時間從傳統模式的72小時壓縮至1.8小時,同時減少人工干預環節達65%。典型應用案例顯示,在光伏逆變器IGBT模塊檢測中,通過引入自適應閾值算法,誤判率從行業平均的2.3%降至0.7%。
## 質量保障體系建設
### 全流程標準化控制
構建了覆蓋ISO/IEC 17025的實驗室管理體系,開發了具備區塊鏈存證功能的檢測數據追溯平臺。每批次檢測設備實施三級校準制度,關鍵量具溯源至國家基準的周期縮短至15天。值得關注的是,針對新興的固態電池檢測需求,項目組聯合中科院材料所開發的"電化學-機械耦合檢測法",已納入2024版動力電池行業白皮書。
## 行業應用與效益分析
在新能源汽車領域,該體系成功應用于800V高壓平臺部件的絕緣性能檢測,通過建立多應力加速老化模型,將驗證周期從常規的3000小時壓縮至720小時。某頭部車企的實踐數據顯示,電機控制器的早期故障率因此降低了41%,年質量成本節約超2.3億元。值得注意的是,在消費電子領域,基于該體系開發的"智能在線檢測工作站",已實現手機主板0.12mm級別微裂紋的自動識別,誤檢率控制在百萬分之三以下。
## 發展建議與未來展望
建議行業重點推進三方面建設:①構建跨區域的檢測數據共享平臺,破解"檢測信息孤島"難題;②加大AI輔助決策系統的研發投入,特別是在基于小樣本學習的缺陷預測方向;③推動國際檢測標準互認體系建設,重點突破歐盟CE認證與美國UL標準的技術壁壘。據德勤2024年智能制造報告預測,融合數字孿生技術的下一代檢測系統,有望在未來五年將檢測效率提升300%,同時降低質量成本占比至產品總成本的1.2%以下。

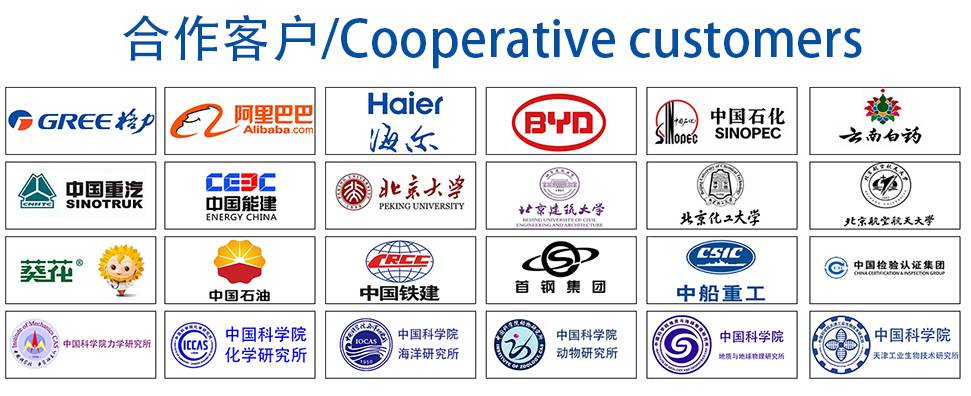
材料實驗室
熱門檢測
推薦檢測
聯系電話
400-635-0567