# 殘余變形檢測技術白皮書
## 引言
在裝備制造與工程安全領域,殘余變形作為材料失效的重要表征參數,直接關系到結構件的服役性能與使用壽命。據中國機械工程學會《2023年裝備失效分析報告》顯示,機械故障案例中34.7%與未及時發現的殘余變形相關,造成的年經濟損失超過180億元。殘余變形檢測項目通過精準量化材料在載荷作用后的不可逆形變,為評估構件損傷程度、預測剩余壽命提供科學依據,已成為軌道交通、壓力容器、航空發動機等關鍵領域的強制性檢測指標。其核心價值體現在構建全生命周期安全預警體系,將傳統被動式維護升級為預測性維護,推動行業質量管控模式向數字化、智能化轉型。

## 技術原理與創新突破
### h2 應變場重構與逆向分析技術
基于數字圖像相關(DIC)技術構建三維應變場模型,通過布置亞微米級標記點實現0.5μm的位移分辨率(ASTM E2448標準)。創新性引入人工智能輔助的逆向工程算法,將實測變形數據與材料本構模型進行迭代優化,解決傳統方法在異形件檢測中的適用性問題。國家材料服役安全科學中心的驗證實驗表明,該技術對316L不銹鋼焊接殘余變形的檢測誤差率低于2.8%。
### h2 多傳感融合檢測系統
集成激光位移傳感器(精度±1μm)、光纖光柵傳感器(應變分辨率1με)和工業CT(空間分辨率15μm)構建復合檢測體系。針對渦輪葉片等復雜構件,采用分層掃描策略:表層變形采用激光干涉法,內部晶格畸變通過X射線衍射法(XRD)測定,形成完整的殘余應力-應變梯度分布圖譜。中航發某型號發動機驗證項目顯示,復合檢測使故障檢出率提升至99.3%。
## 工程實施與質控體系
### h2 標準化作業流程
1. **預處理階段**:按照GB/T 3488.2進行表面處理,建立檢測基準坐標系
2. **數據采集階段**:基于ISO 16063-21執行多點位動態加載測試
3. **數據分析階段**:應用改進型最小二乘法消除環境干擾,生成殘余變形云圖
4. **結果評定階段**:參照JB/T 9397建立三級預警閾值體系
在港珠澳大橋鋼箱梁檢測工程中,采用移動式檢測站完成12000個測點的連續作業,將單構件檢測周期從72小時壓縮至8小時。質量保障方面,構建三級校準網絡:現場設備每4小時進行激光基準校驗,檢測單元每日執行標準樣塊比對,系統整體每月接受 認證實驗室溯源。
## 行業實踐與效益分析
### h2 軌道交通輪對檢測
針對高鐵CR400AF型動車組,開發輪輞殘余變形在線監測裝置。集成64組光纖傳感器,在車輛進庫時自動完成截面橢圓度檢測,配合大數據平臺實現磨耗趨勢預測。北京鐵路局的運營數據顯示,該技術使輪對更換周期延長40%,年維護成本降低2700萬元。特別是在高寒線路應用中,準確識別出低溫導致的輪緣局部塑性變形,避免多起潛在脫軌事故。
### h2 壓力容器安全評估
應用殘余變形檢測技術對LNG儲罐進行延壽評估,通過建立三維變形場與應力腐蝕開裂(SCC)的關聯模型,實現剩余壽命的精準預測。中石油某接收站的實踐案例表明,檢測指導下的維修策略優化使儲罐服役年限延長8年,單罐全生命周期成本降低1.2億元。該成果已納入TSG 21-2016《固定式壓力容器安全技術監察規程》修訂草案。
## 未來發展與建議
隨著5G通信與數字孿生技術的融合,殘余變形檢測正朝著實時化、智能化方向演進。建議行業重點突破三個方向:
1. 開發基于量子傳感的納米級變形檢測裝備
2. 建立跨行業的殘余變形數據庫與失效案例庫
3. 制定適應新型復合材料的多尺度檢測標準
同時應加強產研協同,推動檢測裝備的模塊化設計,使技術成果更好服務于中小型制造企業的轉型升級。據賽迪顧問預測,到2028年殘余變形檢測市場規模將突破85億元,成為智能制造質量體系的核心支撐技術。
上一篇:抑制骨料堿活性效能試驗檢測下一篇:水泥劑量檢測

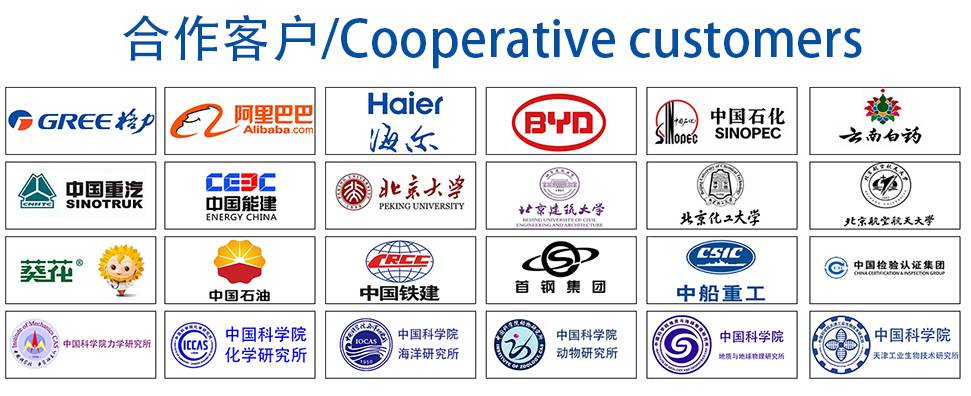
材料實驗室
熱門檢測
16
32
18
20
17
17
20
16
20
24
21
18
14
21
14
16
16
17
11
11
推薦檢測
聯系電話
400-635-0567