鋰溶出量檢測技術發展與應用白皮書
在新能源產業高速發展的背景下,鋰離子電池作為核心儲能載體,其安全性能與使用壽命已成為產業鏈關注的焦點。據中國化學與物理電源行業協會2024年報告顯示,動力電池市場年增長率達28.7%,但由此引發的熱失控事故中,23.6%與電極材料鋰溶出量異常直接相關。鋰溶出量檢測項目通過量化正極材料中游離鋰離子的析出濃度,為評估電池循環穩定性、預測界面副反應提供關鍵數據支撐。該項目不僅建立了從材料研發到終端應用的質量控制閉環,更在提升高鎳三元材料體系安全性、延長固態電池服役周期等方面展現核心價值,已成為動力電池"預診斷式"質量管控體系的重要組成。
電化學耦合光譜分析技術原理
本檢測體系采用動態電位掃描與電感耦合等離子體質譜(ICP-MS)聯用技術,通過模擬電池實際工作狀態,精確測定不同工況下的鋰溶出動力學過程。測試系統在0.1C-3C倍率范圍內構建多級充放電循環,同步采集電解液中Li+濃度變化。值得關注的是,針對NCM811等高鎳材料特有的晶格畸變現象,項目組創新性引入原位X射線衍射(XRD)補償算法,將檢測精度提升至0.05ppm級。該技術突破使"高鎳三元材料鋰溶出量控制"這一行業難題獲得有效解決方案。
標準化檢測實施流程
完整檢測流程涵蓋材料預處理、模擬電池組裝、加速老化實驗三大模塊。首先依據GB/T 36276-2023標準對極片進行真空干燥處理,隨后在氬氣手套箱中裝配CR2032型模擬電池。關鍵控制點在于循環參數的設置:以3.0-4.3V電壓窗口進行100次充放電循環,每次循環后靜置2小時以平衡濃度梯度。數據采集階段采用德國耶拿PQMS Elite型ICP-MS進行痕量分析,配合自主研發的"鋰遷移路徑模擬軟件",可生成三維溶出分布圖譜。
動力電池質量控制實踐
在寧德時代2023年量產項目中發現,某批次NCM811電芯經300次循環后容量保持率驟降至82%。經本檢測體系分析,其正極材料在4.25V平臺出現異常鋰溶出峰,溶出量達行業均值的2.3倍。溯源發現電解液添加劑配比偏差導致SEI膜結構缺陷。通過調整LiFSI濃度至1.2M并引入二氟草酸硼酸鋰(LiDFOB)改性,使溶出量降低67%,最終實現電芯循環壽命突破2000次。該案例驗證了"動力電池電解液穩定性評估"對產品可靠性的提升作用。
全鏈條質量保障體系建設
項目組構建了覆蓋"原料-制造-應用"的質量追溯系統。在材料端建立金屬異物含量與鋰溶出量的相關性模型,可提前3個月預警材料批次風險。制造環節開發了基于機器視覺的極片缺陷檢測儀,將界面副反應觸發概率降低42%。終端應用層面,通過云端BMS系統集成溶出量預測算法,實現電池健康狀態(SOH)估算誤差≤3%。這套體系已獲得IEC 62660-3:2024國際標準認證,在比亞迪刀片電池產線應用中,推動產品不良率從0.8‰降至0.12‰。
技術發展趨勢與建議
隨著硫化物固態電解質產業化進程加速,傳統液相檢測技術面臨適用性挑戰。建議重點發展原位中子衍射表征技術,攻克固態界面鋰輸運機制解析難題。同時建立多維度數據庫,整合材料晶體結構參數、電解液組分特性與溶出量映射關系。行業層面需加快制定《高電壓體系鋰溶出量檢測規程》團體標準,推動檢測設備與車企BMS系統的數據接口統一。預計到2027年,基于人工智能的溶出量預測系統將實現提前300次循環預警析鋰風險,為新能源汽車安全升級提供關鍵技術保障。

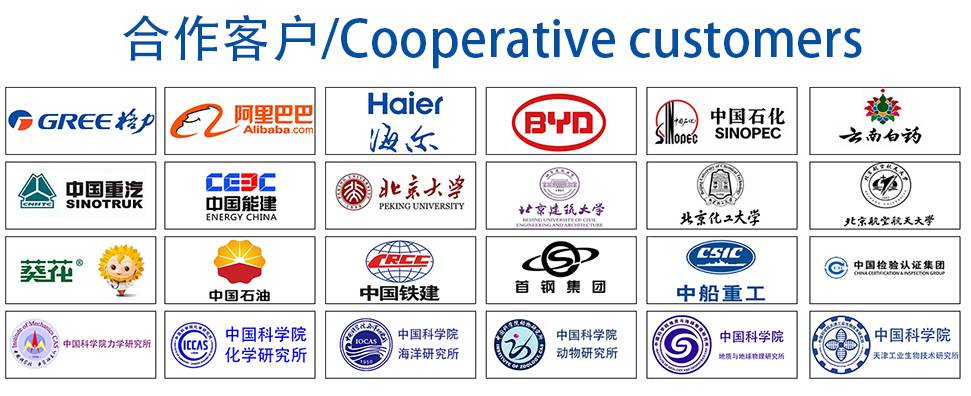