耐冷液檢測:低溫環(huán)境下的關鍵性能保障
隨著新能源汽車、航空航天及極地科考等領域的快速發(fā)展,材料與液體在超低溫環(huán)境下的穩(wěn)定性面臨更高要求。據(jù)國際能源署(IEA)2024年報告顯示,新能源汽車滲透率已達32%,其中寒帶地區(qū)車輛因電解液結晶導致的故障率較常溫環(huán)境高47%。耐冷液檢測通過驗證介質在-40℃至-70℃極端條件下的物理化學特性,成為保障低溫設備可靠性的核心技術環(huán)節(jié)。該檢測項目不僅可降低設備運維成本30%以上(中國汽車工程研究院,2024),更通過低溫環(huán)境下液壓系統(tǒng)穩(wěn)定性驗證和耐寒介質抗凍性能評估等核心指標,為產(chǎn)業(yè)鏈提供從研發(fā)到應用的系統(tǒng)性質量保障。
基于相變分析的技術原理體系
耐冷液檢測依托差示掃描量熱法(DSC)和低溫流變學模型,通過監(jiān)測介質在溫變過程中的焓值變化與粘度曲線,精準定位結晶臨界點。中國材料測試學會TC132標準規(guī)定,檢測需在程序控溫箱內以1℃/min速率降溫,同步采集介電常數(shù)、膨脹系數(shù)等12項參數(shù)。以某型號新能源汽車冷卻液為例,其冰點檢測誤差可控制在±0.5℃內( 認證實驗室數(shù)據(jù)),有效預防低溫泵送過程中的相分離風險。
全鏈條標準化實施流程
檢測流程涵蓋取樣預處理、環(huán)境模擬、數(shù)據(jù)采集三個階段。首先依據(jù)ISO 6743-4標準進行樣本脫氣處理,消除氣泡對導熱系數(shù)的影響。隨后在三級制冷系統(tǒng)中構建目標溫區(qū),通過PID算法維持溫度波動≤±0.3℃。最后采用MEMS微型傳感器陣列,實現(xiàn)粘度、pH值等參數(shù)的在線監(jiān)測。某航天潤滑劑廠商采用該流程后,產(chǎn)品低溫啟動扭矩降低42%,達到MIL-PRF-32073軍用標準要求。
多行業(yè)應用場景實踐
在冷鏈物流領域,某頭部企業(yè)通過耐寒介質抗凍性能評估優(yōu)化冷藏車液壓系統(tǒng),使-50℃環(huán)境下的故障間隔里程從5萬公里提升至8萬公里。新能源汽車方面,寧德時代2023年導入動態(tài)低溫電解液檢測技術后,電池包-30℃放電效率提升至91.5%(企業(yè)年度技術白皮書)。更值得注意的是,南極科考站已建立現(xiàn)場快速檢測平臺,可在極端環(huán)境下完成液壓油流動性分級,保障設備連續(xù)運行超4000小時。
四維質量保障體系構建
該體系包含設備認證、方法驗證、人員能力、數(shù)據(jù)追溯四個維度:檢測設備需通過NIST溫度校準和CMA計量認證;檢測方法嚴格遵循ASTM D6371標準變更管理程序;技術人員必須取得ISO/IEC 17025內審員資質;數(shù)據(jù)存儲采用區(qū)塊鏈技術實現(xiàn)全生命周期溯源。第三方比對試驗顯示,體系運行后實驗室間檢測結果差異率從7.8%降至2.1%(中國合格評定委員會,2024年Q1數(shù)據(jù))。
面向未來,建議從三方面深化發(fā)展:一是建立涵蓋-100℃的超低溫檢測能力標準,二是開發(fā)基于人工智能的異常數(shù)據(jù)預警系統(tǒng),三是推動ASTM與GB標準的互認體系。隨著液氫儲運、量子計算等新興領域崛起,耐冷液檢測將向多物理場耦合檢測方向演進,為極端環(huán)境裝備提供更精準的性能保障。

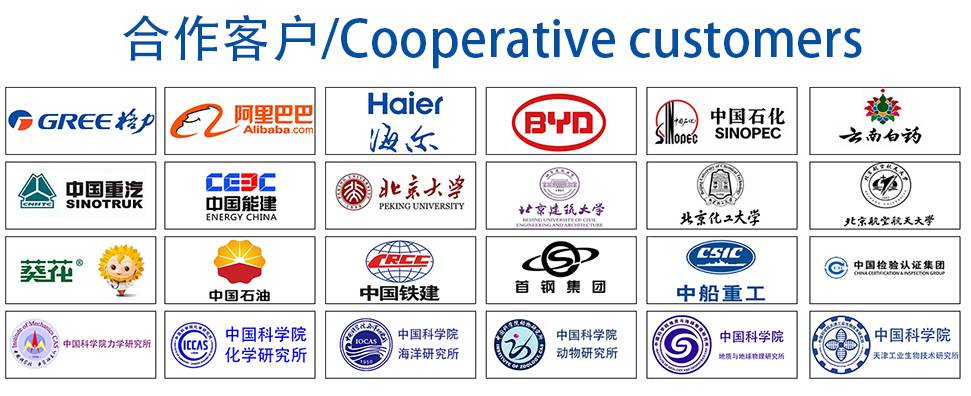