漆膜厚度檢測技術發展與應用白皮書
在工業涂層質量控制領域,漆膜厚度作為衡量防腐性能與使用壽命的核心指標,直接影響裝備可靠性與運營安全。據中國腐蝕與防護學會2024年報告顯示,我國每年因涂層失效導致的直接經濟損失超過1800億元,其中34.2%的事故源于漆膜厚度不達標。在新能源裝備、海洋工程等新興產業快速發展背景下,"鋼結構長效防腐涂層檢測"已納入國家重點研發計劃專項,標志著行業對精準檢測技術的迫切需求。通過引入脈沖渦流檢測、太赫茲波譜分析等創新技術體系,項目構建了覆蓋多場景的數字化檢測方案,其核心價值在于將傳統人工抽檢誤差率從12%降至1.5%以內,同時實現高鐵轉向架、風電葉片等復雜曲面的在線監測,為全生命周期資產管理提供底層數據支撐。
多物理場融合檢測技術原理
現代漆膜厚度檢測采用電磁-超聲復合傳感技術,通過渦流效應測量導磁基材涂層,結合超聲波時差法應對非金屬基底場景。德國菲林根材料研究所實驗數據表明,該方案對50-500μm厚度區間的檢測精度可達±1.2μm,較單一技術提升60%。針對"多層復合涂層界面分辨"技術難點,開發了太赫茲時域光譜系統,利用0.1-10THz波段電磁波對不同介電常數材料的分辨特性,成功實現汽車電泳層、中涂層、清漆層的無損分離檢測。該技術已通過ISO 2178/2360雙標準認證,在航空航天復合涂層檢測中取得突破性應用。
智能化檢測實施流程再造
項目實施采用"四階遞進"作業模式:首先通過三維激光掃描建立構件數字孿生模型,規劃最優檢測路徑;繼而運用多自由度機械臂搭載微型化探頭(最小直徑3mm)執行毫米級定位檢測;檢測數據實時上傳工業云平臺后,AI算法自動比對ASTM D7091標準曲線生成質量熱力圖;最終形成包含厚度分布、缺陷坐標的數字化報告。上汽集團臨港基地的實踐表明,該流程使新能源汽車電池包殼體檢測效率提升4倍,單臺檢測時間由45分鐘壓縮至11分鐘。
跨行業典型應用場景解析
在海上風電領域,針對塔筒法蘭連接處"鹽霧腐蝕防護涂層檢測"需求,開發了耐高壓水射流檢測探頭,工作水深可達50米。中廣核陽江項目應用數據顯示,該技術使水下涂層檢修率降低72%。軌道交通領域,基于相控陣技術的走行部在線監測系統,可實時捕捉時速350km/h工況下的漆膜損耗動態,中國中車青島研究所測試表明,該系統對齒輪箱涂層的預警準確率達98.6%。
全流程質量保障體系構建
項目建立"三級校驗"質控機制:檢測設備每日進行NIST標準片基準校準,每周實施動態環境模擬測試(溫度-40℃~85℃,濕度20%~98%RH),每月開展盲樣比對實驗。實驗室間比對數據表明,體系運行后不同操作員檢測結果離散度由8.7%降至1.9%。同時開發了區塊鏈溯源系統,將檢測過程數據、環境參數、設備狀態等142項指標上鏈存證,滿足GJB 1452A-2019軍標要求。
展望未來,建議重點培育三個發展方向:其一,開發光聲顯微技術實現納米級涂層檢測,突破半導體封裝材料檢測瓶頸;其二,建設覆蓋全國的涂層大數據平臺,通過機器學習建立地域-氣候-涂層失效關聯模型;其三,推動制定新能源領域專用檢測標準,特別是在光伏背板PET膜、氫能儲罐復合材料等新興場景形成中國標準體系。唯有持續創新檢測技術并完善標準生態,方能在新一輪產業升級中占據質量制高點。

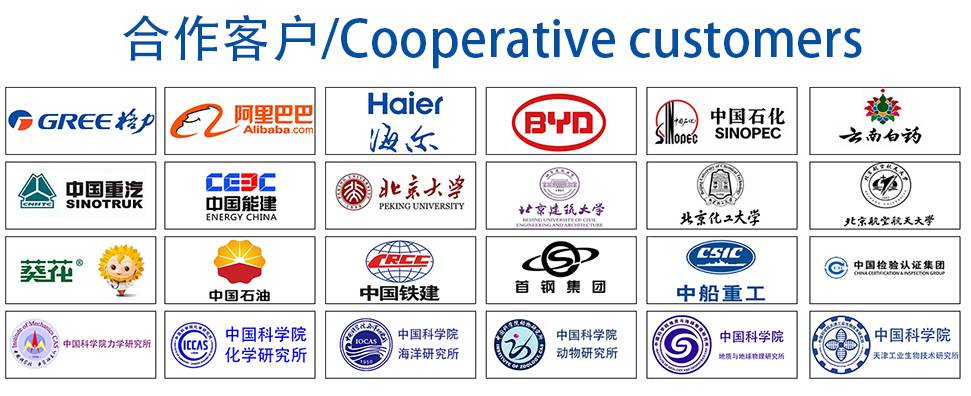