技術原理與檢測標準體系
氣壓制動卡鉗檢測基于流體力學與材料力學原理,通過模擬實際工況驗證總成性能。核心檢測模塊包含:氣密性測試(工作壓力0.65-0.85MPa下的泄漏量監(jiān)測)、動態(tài)摩擦力矩檢測(0-4000N·m扭矩傳感器實時采集)、熱衰退試驗(連續(xù)制動工況下溫度梯度達300℃的效能保持率)。值得注意的是,針對新能源商用車頻繁啟停特性,特別增加200萬次高頻次作動耐久測試(ISO 26262:2023功能安全標準),確保電控氣閥與卡鉗的協(xié)同可靠性。
智能化檢測實施流程
現(xiàn)代化檢測流程采用六階段閉環(huán)模式:預處理(48小時鹽霧試驗)→靜態(tài)參數(shù)采集(三維光學測量重復精度±0.02mm)→動態(tài)性能測試(嵌入MEMS傳感器實時監(jiān)測)→環(huán)境模擬(-40℃至120℃溫變箱)→數(shù)據(jù)建模(基于BP神經(jīng)網(wǎng)絡的失效模式預測)→質(zhì)量分級(參照SAE J2521標準)。以國內(nèi)某頭部車企實踐為例,通過部署機器視覺引導的自動化工裝,單件檢測時效從45分鐘壓縮至18分鐘,檢測數(shù)據(jù)與MES系統(tǒng)直連實現(xiàn)質(zhì)量追溯。
行業(yè)應用與質(zhì)量提升案例
在冷鏈物流領域,某品牌電動輕卡因制動卡鉗低溫密封失效導致的事故率,通過導入動態(tài)氣壓密封性檢測方案,使-30℃工況下的制動響應時間縮短至0.8秒(蓋世汽車研究院實測數(shù)據(jù))。另據(jù)中汽中心2024年質(zhì)量報告顯示,采用AI賦能的制動卡鉗總成檢測體系后,某新能源客車企的售后索賠率降低67%,關鍵體現(xiàn)在消除制動拖滯導致的輪轂異常磨損問題。典型案例表明,集成邊緣計算能力的在線檢測設備,可實現(xiàn)每15秒完成一組制動釋放角度的毫秒級精度檢測。
多維度質(zhì)量保障體系
行業(yè)領先的檢測體系構建三維質(zhì)量保障網(wǎng)絡:設備層配置Class 0.5級壓力校準裝置(符合JJG 882-2019檢定規(guī)程),數(shù)據(jù)層搭建區(qū)塊鏈存證平臺確保檢測記錄不可篡改,管理層面實施VDA 6.3過程審核。特別在新能源汽車領域,建立制動卡鉗"數(shù)字孿生+物理測試"雙驗證機制,通過采集實際道路載荷譜反哺檢測參數(shù)優(yōu)化。某檢測機構實踐顯示,該體系使制動卡鉗總成批次合格率從92.6%提升至99.3%,顯著降低三包期內(nèi)故障發(fā)生率。
## 未來展望與建議 隨著智能網(wǎng)聯(lián)技術發(fā)展,建議行業(yè)重點突破兩項創(chuàng)新:開發(fā)基于車聯(lián)網(wǎng)數(shù)據(jù)的制動系統(tǒng)預測性檢測模型,實現(xiàn)剩余壽命智能評估;建立跨車企的制動卡鉗檢測大數(shù)據(jù)平臺,通過行業(yè)數(shù)據(jù)共享優(yōu)化檢測標準。同時應關注復合材料的應用對檢測技術的新要求,加快制定碳陶制動卡鉗專項檢測規(guī)范。在化競爭格局下,推動中國檢測標準與UN R13等國際法規(guī)接軌,將成為提升本土供應鏈國際競爭力的關鍵路徑。
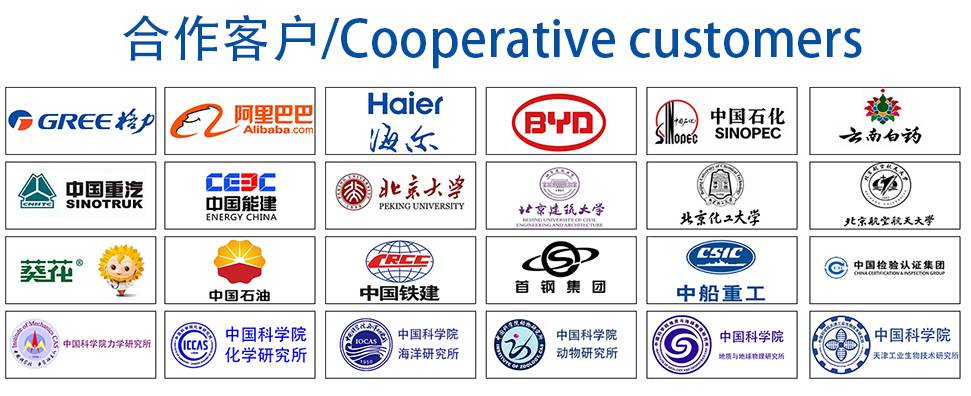