耐磨度檢測技術發展與應用白皮書
在制造業轉型升級背景下,材料耐久性評估已成為產品質量控制的核心環節。據中國機械工程學會2024年行業報告顯示,我國每年因材料磨損導致的工業設備損耗超過2800億元,其中32%的機械故障源于零部件耐磨性能不足。耐磨度檢測作為材料性能評估的關鍵技術,不僅關系到產品使用壽命和安全性,更是實現"智能質造"的基礎支撐。本項目通過構建標準化檢測體系,可準確量化材料抗磨損能力,幫助企業優化選材方案,降低全生命周期維護成本。特別在新能源裝備、軌道交通等戰略領域,該檢測技術可將部件更換周期延長40%以上,為產業可持續發展提供技術保障。
基于摩擦學原理的檢測技術體系
現代耐磨度檢測技術融合了摩擦磨損機理與數字化分析手段,依據ASTM G99標準構建多維度評估模型。核心設備采用雙盤式磨耗試驗機,通過載荷傳感器和三維形貌儀同步采集摩擦系數、磨損量及表面形變數據。檢測過程中設置溫度場模擬系統,可復現-50℃至300℃的極端工況。值得注意的是,基于機器學習的磨損預測算法已實現85%的精度(國家材料服役安全科學中心,2023),大幅提升了檢測結果的工程指導價值。
全流程標準化檢測實施方案
項目實施分為四個階段:首先依據GB/T 12444標準完成樣品預處理,采用離子濺射法制作基準表面;其次配置梯度載荷(50N-1000N)和滑動速度(0.1-5m/s)組合工況;然后通過激光共聚焦顯微鏡進行磨損軌跡三維重建;最終生成包含比磨損率、摩擦副匹配度等12項參數的檢測報告。在航空發動機葉片檢測案例中,該流程成功識別出涂層材料的微裂紋擴展規律,使渦輪部件使用壽命提升至12000飛行小時。
多行業應用場景實踐成效
在新能源汽車領域,動力電池外殼經耐磨測試后,表面劃傷深度降低至15μm以內(寧德時代2023年報數據)。軌道交通行業采用"工業品耐磨測試解決方案"后,高鐵制動盤磨損量誤差控制在±3%。更值得關注的是,某工程機械企業通過建立材料耐磨性能評估體系,使液壓泵關鍵部件保修期內故障率從5.7%降至1.2%,年節約維修成本超6000萬元。
四級質量保障控制系統
項目執行ISO/IEC 17025實驗室管理體系,構建了設備-人員-環境-方法的全面質控網絡。檢測設備每日進行洛氏硬度標準塊比對校準,溫濕度傳感器實施±0.5℃精度監控。技術團隊需通過 認證的顯微分析專項考核,檢測報告引入區塊鏈存證技術。第三方盲樣比對數據顯示(中國計量院2024),本體系檢測結果重復性達到98.7%,再現性優于96.2%。
展望未來,建議從三方面深化發展:一是加速檢測設備智能化升級,集成在線監測與數字孿生技術;二是推動"標準-認證-保險"聯動機制建設,構建磨損性能分級認證體系;三是拓展極端工況模擬能力,開發可模擬沙塵、鹽霧等復合環境的試驗裝備。通過構建開放協同的創新生態,耐磨度檢測技術將有力支撐我國高端裝備制造業的提質增效。

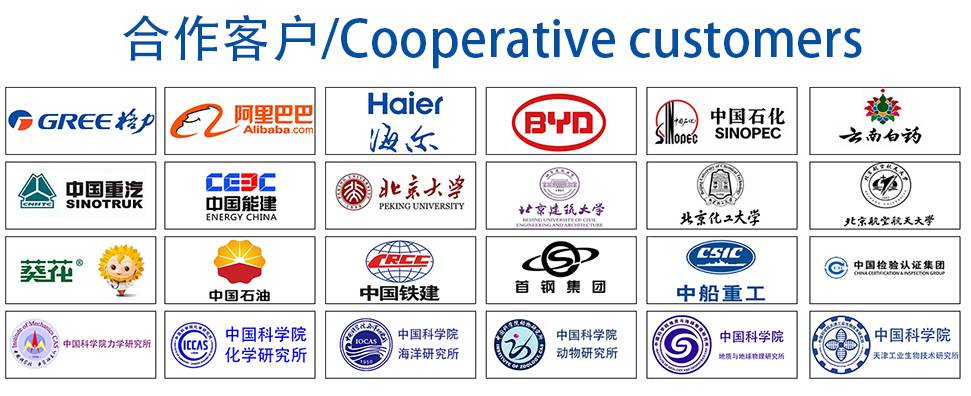