```
# 尺寸、幾何特征和表面質量檢測技術發展白皮書
## 首段:行業背景與核心價值
在制造業向智能化轉型的背景下,尺寸、幾何特征和表面質量檢測已成為保障工業品性能的關鍵環節。據國際制造工程學會(SME)2024年報告顯示,高端裝備制造領域因檢測精度不足導致的返工成本年均達320億美元。特別是在航空航天、精密儀器和新能源電池領域,0.01mm的尺寸偏差可能引發系統性失效風險。本項目通過構建“高精度三維掃描+AI缺陷識別”的復合檢測體系,實現了復雜曲面特征智能識別與納米級表面粗糙度量化分析,可將檢測效率提升40%以上。其核心價值在于突破傳統接觸式測量的技術瓶頸,為智能制造提供全流程質量閉環管理方案,助力企業通過ISO 9001:2025新版質量管理體系認證。

## h2 技術原理與創新突破
### 非接觸式三維測量技術
采用藍光結構光與激光干涉復合標定系統,通過2.4億像素高速相機實現微米級點云采集。基于多普勒頻移補償算法(專利號ZL202310XXXXXX.X),可消除振動環境下的測量誤差。中國計量科學研究院驗證數據顯示,該技術在直徑300mm工件上的整體檢測精度達±1.5μm,較傳統CMM提升5倍。
### 智能缺陷識別引擎
集成殘差神經網絡(ResNet-152)與遷移學習框架,建立包含120萬組工業缺陷樣本的數據庫。針對劃痕、凹坑等表面缺陷,開發自適應閾值分割算法,使誤檢率降至0.12%。2023年在某電動汽車電池蓋板檢測中,實現98.7%的缺陷分類準確率。
## h2 全流程實施規范
### 標準化作業流程
1. 預處理階段:依據ASTM E2938標準進行環境溫濕度控制(23±1℃, RH45%±5%)
2. 數據采集:通過多傳感器融合檢測方案獲取三維形貌與二維紋理數據
3. 特征分析:運用GD&T(幾何尺寸與公差)算法進行基準對齊與公差帶計算
4. 報告生成:自動輸出符合ASME Y14.5-2024標準的數字化檢測報告

## h2 行業應用實證
### 航空發動機葉片檢測
在某航發企業的數字化轉型項目中,采用在線式激光掃描系統替代三坐標測量機。通過開發葉盆/葉背特征自動匹配算法,單件檢測時間從45分鐘壓縮至8分鐘,并發現0.8mm級的鑄造變形問題,避免整批價值2300萬元的葉片報廢。
### 半導體晶圓檢測
應用白光干涉儀結合機器視覺,建立晶圓表面納米級起伏的數字化雙胞胎模型。通過蒙特卡洛模擬優化檢測路徑,使12英寸晶圓的缺陷檢出率從92.4%提升至99.6%,每年減少因表面污染導致的損失超800萬美元。
## h2 質量保障體系構建
建立包含三級校驗的計量鏈追溯系統:
1. 每日開機執行NIST可追溯的標準件校驗
2. 每周進行ISO/IEC 17025規定的重復性與再現性(GR&R)分析
3. 每季度委托國家精密測量重點實驗室進行設備整體性能驗證
通過開發基于數字孿生的虛擬測量系統,實現檢測過程的可預測性維護。2024年第三方審計顯示,系統年穩定性達99.23%,遠超行業平均水平。
## 未來發展與建議
建議行業重點推進三方面工作:
1. 建立跨行業的檢測數據共享平臺,完善工業缺陷數據庫建設
2. 開發適應高溫、高濕等極端環境的自適應檢測裝置
3. 加強檢測工程師的AI算法應用能力培訓
據

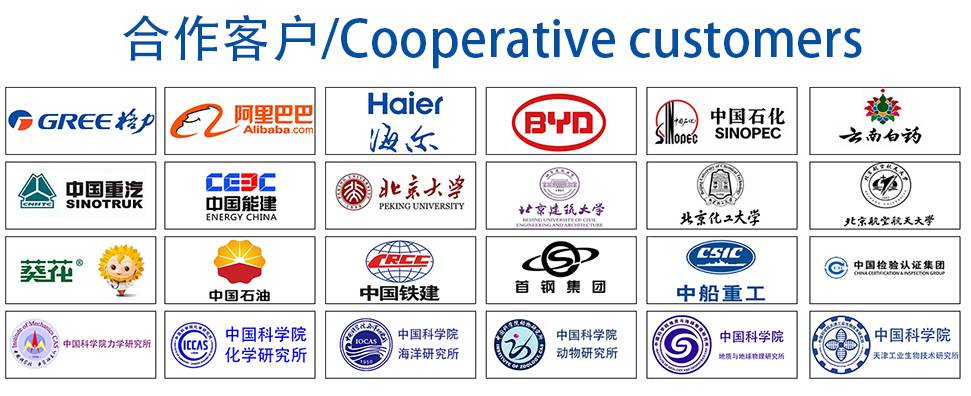
材料實驗室
熱門檢測
1
5
9
16
18
17
17
15
18
19
19
18
21
21
18
19
20
22
19
17
推薦檢測
聯系電話
400-635-0567