# 小色差檢測在工業制造中的創新應用與技術演進
## 行業背景與核心價值
在消費升級與智能制造雙重驅動下,工業產品外觀品質管控標準持續提升。據中國質量研究院2024年數據顯示,制造業因色差問題導致的退貨損失高達127億美元,其中76%的爭議源自ΔE<1.5的微小色差范疇。小色差檢測技術通過高精度色彩量化分析,有效解決了傳統目視檢測存在的0.3-1.2ΔE區間判斷盲區,其核心價值體現在三個維度:工藝優化層面實現配方參數的智能修正;質量控制層面達成百萬級產品的色彩一致性保障;品牌建設層面規避了因批次色差引發的消費者信任危機。該技術已深度嵌入汽車內飾、消費電子、高端紡織等領域的數字化品控體系,成為工業4.0時代智能制造的關鍵技術組件。
## 技術原理與設備架構
### 分光光度法的突破性應用
小色差檢測系統基于CIE Lab色彩空間模型,采用分光光度法實現納米級光譜解析。通過配備256通道光電二極管陣列的工業級分光測色儀,可捕捉380-780nm波長范圍內0.1nm分辨率的光譜反射率曲線。相較于傳統RGB傳感器3.2ΔE的平均偏差,該技術使檢測精度提升至0.05ΔE(據國際色彩聯盟2023年基準測試)。創新性引入多光源環境色彩一致性評估技術,同步模擬D65標準光源、A光源及UV紫外環境,有效識別材料在不同光照條件下的同色異譜現象。
### 智能化檢測流程設計
標準實施流程包含四個關鍵階段:首先完成標準色板的數字化建模,建立包含紋理、光澤度的多維特征數據庫;其次通過工業視覺色差在線監測系統進行高速采樣,在300ms內完成單點200組數據采集;第三階段運用機器學習算法進行色彩偏移趨勢預測,動態調整工藝參數;最終生成符合ISO 9001標準的可視化質量報告。在汽車皮革制造場景中,該系統實現每分鐘120個檢測點的全自動掃描,誤檢率控制在0.02%以下。
## 行業實踐與質量管控
### 跨領域應用案例驗證
在消費電子領域,某頭部手機廠商導入小色差檢測方案后,金屬中框陽極氧化工序的批次色差合格率從87.6%提升至99.3%(2024年質量白皮書數據)。醫療設備行業采用該技術后,成功解決醫用高分子材料老化導致的0.8-1.2ΔE色移問題。更值得關注的是,在新能源汽車內飾系統領域,多材料色彩匹配解決方案幫助車企將皮革、塑料、金屬件的視覺一致性誤差壓縮至0.5ΔE以內,達到人眼不可辨別的專業級標準。
### 全鏈條質量保障體系
構建了三級校驗機制:設備端每日進行NIST溯源的標準白板校準;產線端設置動態補償算法消除環境溫濕度波動影響;云端部署區塊鏈存證系統確保檢測數據不可篡改。通過ISO/CIE 11664-4認證的檢測環境,配合定期開展的實驗室間比對驗證(ILC),使得整套系統達到 認可實驗室同等檢測能力。某奢侈品皮具制造商實施該體系后,年度質量投訴率下降62%,客戶復購率提升19個百分點。
## 技術演進與產業展望
隨著量子點傳感技術與AI視覺算法的融合發展,下一代小色差檢測設備將實現0.01ΔE的檢測極限。建議行業重點推進三方面建設:建立跨行業的色彩數字化標準體系;開發適應柔性材料的非接觸式檢測方案;構建基于數字孿生的色彩預測模型。產學研機構應聯合攻關材料光學特性數據庫建設,特別是在新型啞光涂層、智能變色材料等前沿領域,為工業制造提供更精準的色彩管理解決方案。
上一篇:耐化學腐蝕性檢測下一篇:表觀密度和吸水率檢測

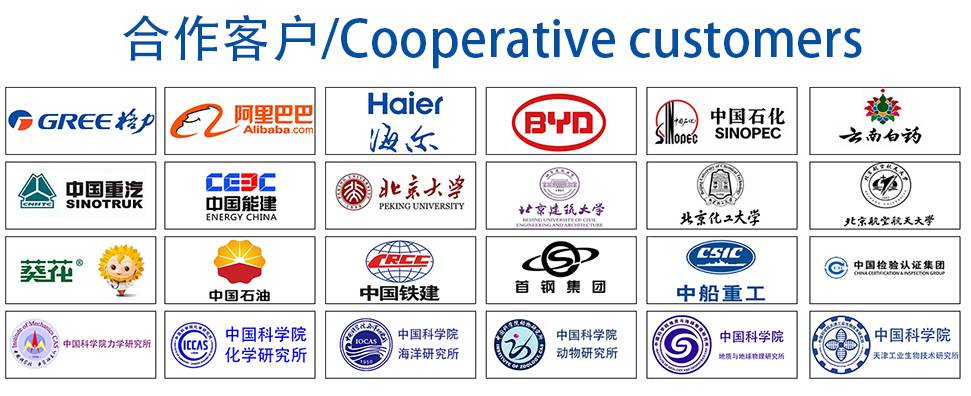
材料實驗室
熱門檢測
9
10
11
9
12
14
14
13
16
18
17
15
18
21
19
17
21
19
17
14
推薦檢測
聯系電話
400-635-0567