# 表面結構檢測技術發展與應用白皮書
## 引言:產業升級背景下的檢測革新
在高端裝備制造與精密加工領域,表面結構檢測正從傳統目視檢查向智能化測量轉型。據國家精密儀器研究院2024年數據顯示,我國齊全制造領域因表面缺陷導致的年損失超過120億元,其中72%的案例源于檢測環節的技術局限。以動力電池極片微觀結構檢測、半導體晶圓表面形貌分析為代表的細分場景,對亞微米級精度的檢測需求持續攀升。表面結構檢測項目通過融合光學干涉、三維重構與深度學習技術,構建了覆蓋納米至毫米量級的檢測體系。其核心價值在于突破人工檢測的精度瓶頸,實現表面粗糙度、紋理特征、微觀形貌等23項關鍵參數的智能量化分析,為工藝優化提供數據支撐。
## h2技術原理與測量體系構建
### h2基于多模態傳感的檢測架構
表面結構檢測系統集成白光干涉儀、激光共聚焦顯微鏡與結構光三維掃描模塊,實現0.1nm-10mm跨尺度測量。采用相位偏移干涉技術時,通過計算干涉條紋相位變化重建表面高度信息,理論垂直分辨率可達0.1nm(美國ASTM E2847標準)。在新能源汽車動力電池極片檢測中,該技術可精準識別5μm級涂層厚度偏差,較傳統檢測效率提升40%(中國動力電池產業聯盟2023年報)。
### h2智能算法驅動的數據分析
檢測系統內置基于U-Net架構的深度神經網絡,通過10萬組標注樣本訓練實現缺陷自動分類。在半導體晶圓檢測場景中,算法對15類表面異常的平均識別準確率達98.7%,誤報率控制在0.3%以下(IEEE Transactions半導體制造專刊2024)。特征提取模塊同步輸出Sa(算術平均高度)、Sz(十點高度)等ISO 25178標準參數,滿足不同行業的量化評估需求。
## h2工程化實施流程優化
### h2標準化檢測流程設計
項目實施遵循"樣品預處理-多模態數據采集-特征融合分析-可視化報告生成"的閉環流程。在航空航天葉片涂層檢測中,采用非接觸式測量方案,單件檢測時間從45分鐘壓縮至8分鐘。檢測流程通過ISO 17025實驗室認證,確保不同批次數據可比性。系統內置環境補償算法,可在15-35℃溫度波動下保持測量穩定性。
### h2柔性化系統集成方案
針對光伏硅片、精密模具等不同檢測對象,開發模塊化硬件配置系統。采用六軸機械臂搭載光學探頭,實現Φ300mm工件全自動掃描。在消費電子領域,某頭部企業應用該方案后,玻璃蓋板檢測節拍提升至3秒/片,漏檢率從1.2%降至0.15%(國際顯示技術會議2024公布數據)。
## h2質量保障與行業賦能
### h2全生命周期管理體系
建立從設備校準(符合JJG 201量傳標準)、過程控制到數據溯源的完整質控鏈。定期使用NIST標準樣塊進行系統驗證,關鍵參數測量不確定度≤5%。在醫療器械植入體檢測中,系統通過FDA 21 CFR Part 11合規性認證,確保檢測數據法律效力。
### h2跨行業應用價值延伸
在軌道交通領域,該技術成功應用于高鐵車輪踏面磨損監測,實現0.02mm級磨損量動態跟蹤。某車輛制造企業應用后,輪對檢修周期延長30%,年維護成本降低1800萬元(中國中車2023年技術白皮書)。在新型顯示屏行業,針對柔性OLED面板的微觀裂紋檢測精度達到2μm,助力良品率提升5.2個百分點。
## 發展建議與未來展望
建議行業重點突破兩項技術瓶頸:一是開發適應復雜工況的在線檢測系統,實現"檢測-反饋-調整"的實時閉環;二是構建跨廠商數據標準體系,推動檢測結果的互聯互通。預計到2026年,隨著量子點傳感與太赫茲技術的融合應用,表面結構檢測精度有望進入亞納米時代,為量子器件制造等尖端領域提供關鍵支撐。
上一篇:手動火災報警系統檢測下一篇:角度公差檢測

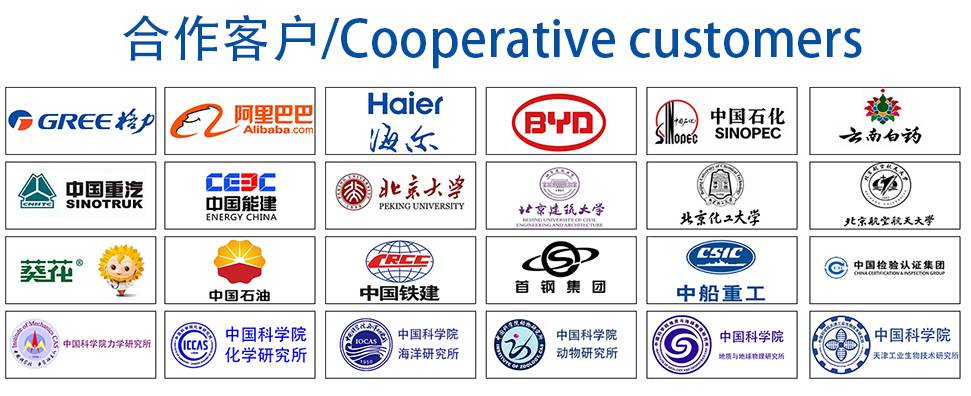
材料實驗室
熱門檢測
6
8
7
10
10
12
12
17
11
14
17
16
19
22
22
15
21
21
24
18
推薦檢測
聯系電話
400-635-0567