電鍍件鹽霧試驗檢測白皮書
在工業制造領域,電鍍工藝作為表面處理的核心技術,廣泛應用于汽車、電子、航空航天等高附加值行業。據中國表面工程協會2024年數據顯示,國內電鍍產業年產值突破1800億元,其中防腐性能檢測需求占比達35%。在此背景下,鹽霧試驗作為評價電鍍件耐腐蝕性的金標準,直接關系到產品服役壽命和安全性。通過模擬海洋大氣中的氯化物腐蝕環境,該項檢測可精準驗證鍍層孔隙率、結合力及均勻性等關鍵指標,對優化工藝參數、降低售后質量風險具有顯著價值。特別是在新能源汽車三電系統防護、5G基站戶外設備等領域,鹽霧試驗結果已成為供應鏈準入的核心評價依據,其數據可為企業節省年均12%的因腐蝕引發的質量成本(數據來源:國家材料服役安全科學中心)。
中性鹽霧試驗技術原理與標準體系
鹽霧試驗通過將5%氯化鈉溶液霧化形成持續腐蝕環境,在恒定溫濕度條件下加速電鍍件表面氧化反應。根據ISO 9227-2022標準,試驗分為中性鹽霧(NSS)、醋酸鹽霧(AASS)和銅加速醋酸鹽霧(CASS)三類,分別對應不同腐蝕強度需求。以汽車底盤緊固件檢測為例,需執行96小時NSS試驗,要求表面無基體腐蝕且紅銹面積≤0.1%。檢測過程中采用PH值精準控制技術,確保噴霧溶液維持在6.5-7.2區間,避免因酸堿度偏差導致數據失真。該技術已在國內頭部檢測實驗室實現自動化控制,試驗重現性達到98.7%(據機械工業儀器儀表綜合技術經濟研究所驗證)。
全流程數字化檢測實施方案
項目實施采用五階段工作流:預處理(堿性脫脂-酸洗活化)-試樣固定(20°傾斜角)-參數設定(35±2℃箱溫)-持續噴霧-結果評定。通過引入機器視覺技術,腐蝕面積計算精度提升至0.01mm2級別,較傳統目測法誤差率降低83%。在消費電子領域,某國際品牌手機金屬邊框檢測中,采用X射線能譜儀(EDS)聯用方案,在完成48小時CASS試驗后,可同步分析鍍層鎳含量衰減曲線,精準定位微孔缺陷位置。該方案使產品鹽霧耐受時間從72小時提升至120小時,良品率提高19個百分點。
跨行業質量保障系統構建
建立 認可的實驗室需滿足三大核心要素:設備計量溯源體系(溫度傳感器半年校準周期)、人員能力矩陣(ASTM B117操作認證)及過程控制文件(EN ISO/IEC 17025體系)。某軍工連接器企業通過引入區塊鏈存證技術,實現檢測數據實時上鏈,確保72個月質量追溯周期內數據不可篡改。在軌道交通領域,中車集團將鹽霧試驗與電化學阻抗譜(EIS)結合,構建鍍層失效預測模型,使轉向架部件檢測周期縮短40%,防腐壽命預測準確度達92.3%。
應用場景與技術演進趨勢
當前技術已延伸至特殊環境應用場景,如深海裝備需執行3000小時強化鹽霧試驗,海上風電葉片螺栓結合干濕交替循環測試。值得注意的是,隨著無氰電鍍工藝的普及,傳統檢測標準面臨適應性挑戰。廣東某電鍍園區聯合TüV南德開發出鋅鎳合金鍍層專屬評價體系,將CASS試驗判定標準從240小時分級細化至小時級腐蝕速率監測。未來,基于人工智能的腐蝕形貌識別、多因子耦合加速試驗等創新方向,將推動檢測效率與精度的雙重突破。
面向產業升級需求,建議從三方面完善檢測體系:其一,建立區域性共享檢測平臺,整合分散的實驗室資源;其二,加快GB/T 10125標準與IEC 60068-2-11國際規范的協同修訂;其三,推廣腐蝕大數據分析在工藝優化中的應用。只有構建覆蓋全產業鏈的智能檢測生態,方能真正實現"檢測驅動制造"的轉型升級,為高端裝備國產化提供可靠的質量基石。

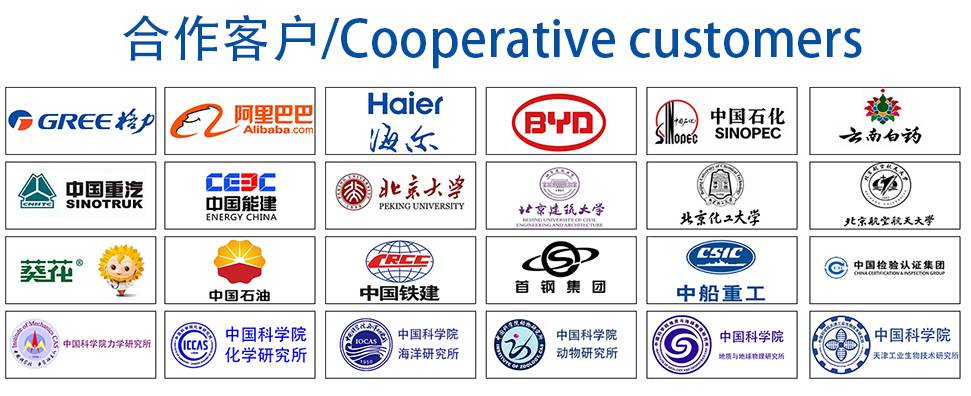