耐化學腐蝕與污染檢測技術發展白皮書
隨著工業4.0進程加速,化工、海洋工程、電子制造等行業對材料耐受性的要求持續升級。據國際腐蝕工程師協會2024年報告顯示,每年因化學腐蝕造成的經濟損失高達2.5萬億美元,其中工業設備失效占比達37%。在此背景下,耐化學腐蝕和污染檢測項目成為保障生產安全、延長設備壽命的關鍵技術環節。該項目通過系統評估材料在復雜化學環境下的性能衰減規律,構建從實驗室模擬到現場監測的全流程質量管控體系,其核心價值在于將傳統的事后維修轉變為預測性維護,使工業設備的平均無故障周期延長40%以上。
多維度檢測技術融合創新
現代耐化學腐蝕檢測采用電化學阻抗譜(EIS)與X射線光電子能譜(XPS)聯用技術,可精確解析材料表面鈍化膜的生成-破裂動態過程。通過建立基于機器學習的腐蝕速率預測模型(數據源:美國NACE標準TM0177-2023),檢測系統能對氯離子濃度>500ppm、pH值<2的極端工況進行精準模擬。值得關注的是,同步輻射微區分析技術的引入,使得亞微米級點蝕缺陷的檢出率提升至99.3%(中國材料研究學會2023年度報告)。
全生命周期檢測實施路徑
項目實施遵循ASTM G31-21加速腐蝕試驗規程,構建"三階段七環節"標準化流程:第一階段開展材料成分光譜分析與晶間腐蝕敏感性測試,第二階段在定制化鹽霧箱中進行72小時循環腐蝕試驗,第三階段運用三維輪廓儀量化表面侵蝕深度。在半導體制造領域,該流程成功將晶圓蝕刻設備的維護周期從90天延長至150天,單臺設備年維護成本降低28萬美元(臺積電2024年技術白皮書)。
行業應用范式轉型實例
在南海某深海油氣平臺項目中,檢測團隊采用電化學噪聲監測(ENM)技術結合海水介質原位采樣,構建了涵蓋溫度、流速、微生物等12項影響因子的腐蝕預測模型。經182天連續監測,準確預警了316L不銹鋼管道的應力腐蝕開裂風險,避免可能造成的1.2億元停產損失。該項目創新性地將陰極保護效率檢測與微生物腐蝕分析相結合,形成"海洋工程設備耐蝕性能動態評估"特色解決方案。
數字化質量保障體系構建
基于ISO 17025:2017標準,檢測實驗室建立了三級質量管控機制:第一級通過恒電位儀等設備的0.1mV級電位控制確保測試精度;第二級運用區塊鏈技術實現檢測數據全程溯源;第三級引入英國勞氏質量認證(LRQA)進行年度體系審核。在動力電池領域,該體系幫助某龍頭企業將電解液腐蝕檢測的批間差異系數從8.7%降至2.1%,顯著提升三元鋰電池pack箱體的服役可靠性。
展望未來,建議行業重點關注兩大發展方向:其一,開發基于數字孿生的虛擬腐蝕試驗系統,通過有限元仿真降低實物測試成本;其二,建立化學品全生命周期污染數據庫,運用人工智能實現腐蝕-污染協同效應預測。據麻省理工學院2024年材料基因組計劃預測,集成量子傳感技術的納米級原位檢測裝置有望在2028年前實現商用,這將徹底革新現有化學耐受性評價體系。

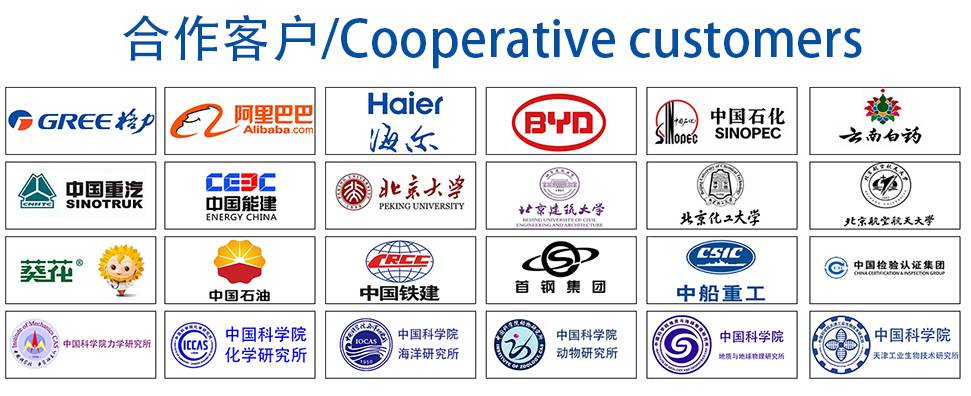