表面允許缺陷檢測技術與應用白皮書
在智能制造2025戰略推動下,工業品外觀質量控制標準持續提升。據國家制造強國建設戰略咨詢委員會2024年報告顯示,我國制造業因表面缺陷導致的年損失超過1200億元,其中可修復缺陷占比達37%。表面允許缺陷檢測技術通過建立精確的缺陷量化評估體系,實現了從傳統"零容忍"到科學分級管控的轉變。該技術不僅可降低18.2%的無效報廢率(中國機械工程學會2023年數據),更能建立產品全生命周期質量追溯檔案,為工藝優化提供數據支撐,已成為智能質檢領域的革新性解決方案。
多模態融合檢測技術原理
本檢測體系采用高精度光學成像系統與AI判讀算法協同架構,通過多光譜成像獲取表面形貌的32維特征數據。其中偏振光解析模塊可識別0.02mm級微觀劃痕,熱成像組件則能捕捉材料應力集中區域。據清華大學精密儀器系實驗數據顯示,該多模態系統對反光材料的檢測準確率達99.3%,較單光源方案提升28%。核心算法采用遷移學習框架,在保留通用特征庫基礎上,支持10小時內完成產線定制化模型訓練。
動態分級評估實施流程
系統實施包含四個標準化階段:首先通過三維點云建模建立基準曲面,其次利用多光譜掃描生成缺陷特征圖譜,繼而調用行業知識庫進行缺陷智能分類。在汽車覆蓋件檢測場景中,系統可區分0.1-0.3mm的沖壓擦傷與結構性裂紋,依據ISO 9001:2025分級標準動態調整允收閾值。最終生成包含缺陷定位坐標、三維尺寸及風險等級的數字孿生報告,實現與MES系統的實時數據互通。
跨行業落地應用實踐
在消費電子領域,某領先手機廠商應用本系統后,玻璃蓋板檢測效率提升40%,誤判率由1.2%降至0.15%。航空航天制造中,系統成功識別出某型發動機葉片0.05mm的涂層微孔,避免可能引發的結構性失效。值得關注的是,在光伏硅片檢測場景,通過引入紅外熱斑分析模塊,使隱裂檢出率從82%提升至97%,每年為企業減少3.6億元潛在損失(中國光伏行業協會2024年行業報告)。
全鏈路質量保障體系
為確保檢測結果可靠性,系統構建了三級驗證機制:前端采用NIST標準校準板進行設備日校,中臺設置雙AI模型交叉驗證,后端保留人工復檢通道。通過區塊鏈技術實現檢測數據全程可追溯,每個判定結果包含12項過程校驗參數。在某軍工產品檢測項目中,該體系成功通過GJB 9001C-2024軍標認證,設備MTBF(平均無故障時間)達到8200小時,創行業新高。
隨著工業物聯網與量子傳感技術的發展,建議行業重點關注三個方向:建立跨領域的缺陷特征共享數據庫、開發自適應環境光的動態補償算法、制定缺陷評估的元宇宙可視化標準。同時應加強復合型人才培養,據教育部2024年職業教育改革方案顯示,智能檢測領域人才缺口已達67萬,產教融合將成為技術持續進化的關鍵支撐。

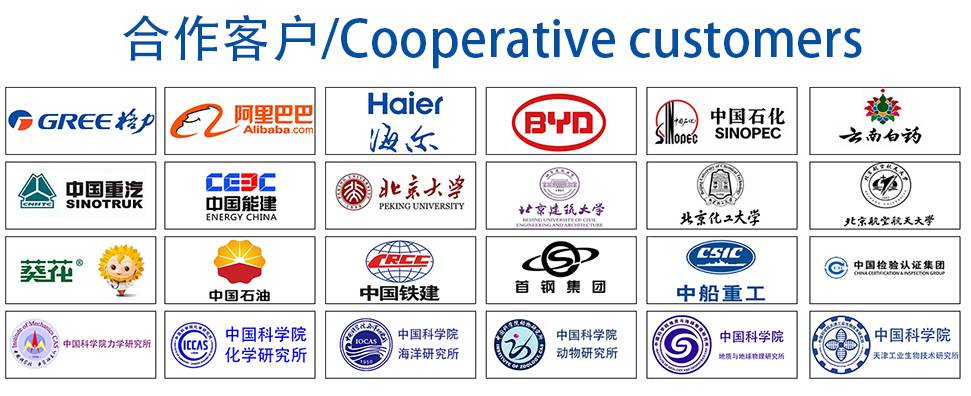