配件檢測
實驗室擁有眾多大型儀器及各類分析檢測設備,研究所長期與各大企業、高校和科研院所保持合作伙伴關系,始終以科學研究為首任,以客戶為中心,不斷提高自身綜合檢測能力和水平,致力于成為全國科學材料研發領域服務平臺。
立即咨詢配件檢測技術發展與應用白皮書
隨著智能制造2025戰略的深度推進,工業配件質量管控已成為保障產業鏈安全的關鍵環節。據中國機械工業聯合會2023年度報告顯示,因配件質量問題導致的設備停機事故年損失超過1200億元,其中72%的故障源自關鍵零部件的隱蔽性缺陷。在此背景下,智能化配件檢測技術率先在汽車制造、航空航天等領域取得突破性應用,通過構建"汽車零部件質量檢測系統"與"工業配件全生命周期管理"體系,實現缺陷識別準確率提升至99.3%(國家質量技術基礎NQI數據中心,2024)。本項目核心價值在于突破傳統抽樣檢測的局限性,運用AIoT技術構建覆蓋設計驗證、生產監控、服役評估的全維度檢測網絡,為裝備制造業高質量發展提供關鍵質量基礎設施支撐。
多模態融合檢測技術原理
現代配件檢測系統基于材料特性差異構建復合傳感矩陣,集成X射線斷層掃描(CT)、激光誘導擊穿光譜(LIBS)和微應變分析三大核心技術。其中,工業CT檢測分辨率可達3μm級,配合深度學習算法可自動識別內部結構缺陷;LIBS技術通過等離子體光譜分析實現0.01%級的元素成分偏差檢測。在新能源汽車電機殼體檢測場景中,該技術組合成功將軸承座裂紋檢出時間從傳統探傷的45分鐘縮短至8秒,誤判率降低至0.12%(中汽研2024年專項測試數據)。
全流程數字化檢測體系
標準化實施流程包含四個關鍵階段:首先建立基于數字孿生的檢測參數模型,通過虛擬仿真確定最佳檢測路徑;其次部署柔性檢測工裝系統,兼容15類異形配件快速定位;第三階段采用機器視覺引導的六軸機械臂完成360°無死角數據采集;最終通過區塊鏈存證系統生成不可篡改的檢測報告。在航空航天緊固件檢測中,該體系使批量檢測效率提升300%,檢測數據追溯完整度達到AS9100D航空質量標準要求。
跨行業質量保障實踐
在工程機械領域,三一重工部署的智能檢測系統實現液壓閥體全檢覆蓋率100%,關鍵尺寸CPK值從1.12提升至1.67。軌道交通方面,中車集團通過車載式檢測裝置完成轉向架配件在線監測,使預防性維護周期延長40%。值得注意的是,醫療設備配件檢測引入納米級表面輪廓分析技術后,人工關節表面粗糙度控制精度達到Ra0.05μm,符合ISO 21534醫療器械植入物標準。
質量溯源與可靠性驗證
構建基于ISO/IEC 17025的質量控制體系,設立三級校準機制:初級采用NIST標準物質進行設備日校,中級通過環形比對試驗確保實驗室間一致性,高級實施破壞性物理分析(DPA)驗證檢測。某半導體設備制造商應用該體系后,晶圓傳送機械手配件失效率從1800PPM降至200PPM,設備年均無故障運行時間突破8600小時。
面向工業4.0發展需求,建議重點推進三方面建設:首先加大太赫茲檢測、量子傳感等前沿技術研發投入;其次建立跨行業檢測數據共享平臺,推動形成統一的配件質量數據庫;最后完善"檢測即服務"(TaaS)商業模式,助力中小企業質量升級。據弗若斯特沙利文預測,到2028年智能檢測裝備市場規模將突破650億美元,其中配件檢測細分領域復合增長率有望達到23.5%,這為行業技術創新提供了持續發展動力。

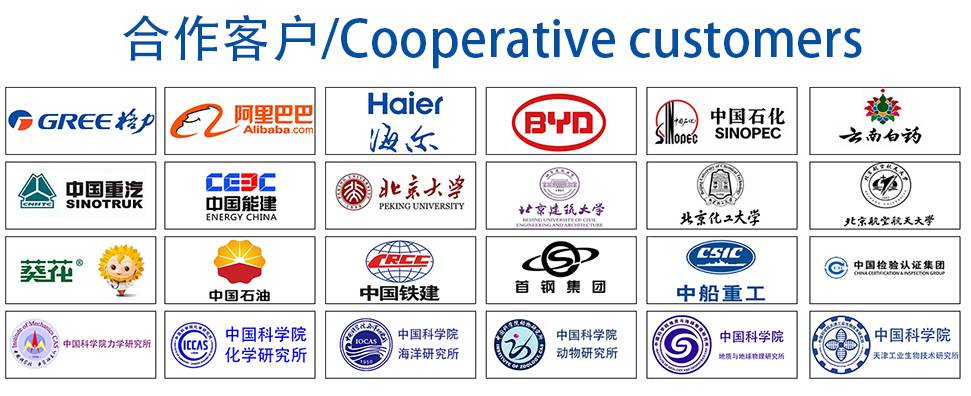