# 水溫穩定性檢測技術應用白皮書(2024)
## 引言
在精細化生產成為主流的工業4.0時代,水溫穩定性作為關鍵工藝參數,直接影響能源、化工、生物制藥等核心產業的產品質量與生產安全。據中國工業自動化研究院2024年數據顯示,因溫度波動導致的工業事故占總生產事故的17.3%,直接經濟損失超80億元/年。在此背景下,水溫穩定性檢測項目通過構建高精度溫度傳感網絡與智能分析系統,為生產過程提供實時偏差預警和動態調節方案,其核心價值體現在質量合格率提升(典型行業提升23%)、能耗降低(平均節能15%)及設備壽命延長(預防性維護效率提升40%)三大維度,已成為智能制造體系的重要技術支點。
![水溫穩定性檢測系統架構示意圖]
## 技術原理與實現路徑
### 分布式傳感與自適應控制技術
系統采用多光譜紅外測溫陣列與納米級熱敏電阻復合傳感技術,實現0.01℃級溫度分辨率。通過安裝于管道外壁的無線傳感模塊(工作頻率868MHz),構建覆蓋半徑50米的工業級Mesh網絡,結合時間序列預測模型(LSTM算法),可提前5分鐘預判溫度波動趨勢。該技術突破傳統單點測溫局限,特別適用于制藥企業生物反應器、食品加工滅菌釜等對溫度場均勻性要求嚴苛的場景。
### 全鏈路閉環管理系統
項目實施遵循PDCA循環原則:部署階段基于CT掃描建模構建三維熱場分布圖;運行階段通過OPC UA協議與DCS系統實時交互;校準階段采用NIST可溯源標準器實施在線標定。某石化企業加氫反應裝置應用案例顯示,系統將催化劑活性溫度區間偏差從±1.2℃壓縮至±0.3℃,使目標產物收率提升9.7%(數據來源:2024年《流程工業》第3期)。
## 行業應用實踐
### 生物制藥純化水系統
在上海某單抗藥物生產基地,系統集成TOC檢測模塊與溫度控制單元,構建符合GMP標準的注射用水循環體系。通過動態調節熱交換器功率,將分配管路水溫穩定在80±0.5℃區間,使內毒素水平降低至0.003EU/ml(低于藥典標準兩個數量級)。該項目實現年節約蒸汽用量3800噸,驗證了溫控優化對制藥用水系統的提質增效作用。
### 數據中心冷卻塔群控
針對大型IDC機房冷量需求波動特性,廣州某超算中心部署多回路水溫協同控制系統。運用強化學習算法建立冷卻塔效能模型,在保證CPU溫度閾值前提下,動態調整冷卻水流量與風機轉速。實際運行數據顯示,PUE值從1.35優化至1.21,年節電量達870萬kWh,凸顯水溫穩定性管理在新型基礎設施領域的戰略價值。
## 質量保障與持續改進
系統建立三級校驗體系:①現場端設置每日自動零點校準;②區域級配備移動式黑體輻射源校準車;③中心實驗室每年實施SN/T 1538.1標準認證。同時引入基于數字孿生的虛擬調試技術,可在不停機狀態下完成系統升級。值得關注的是,平臺內置的AI診斷模塊已實現92%的故障類型自主識別,大幅降低傳統PLC系統3-5小時/次的故障排查耗時。
## 發展展望
建議從三方面深化技術應用:①開發自供電型柔性溫度傳感器,拓展船舶壓載水處理等移動場景應用;②構建跨行業溫控知識圖譜,推動工藝參數共享優化;③結合5G+TSN時間敏感網絡,實現百微秒級控制響應。隨著工業元宇宙技術成熟,未來可通過AR眼鏡實現溫度場三維可視化巡檢,推動水溫穩定性管理向智能化、沉浸式方向演進。

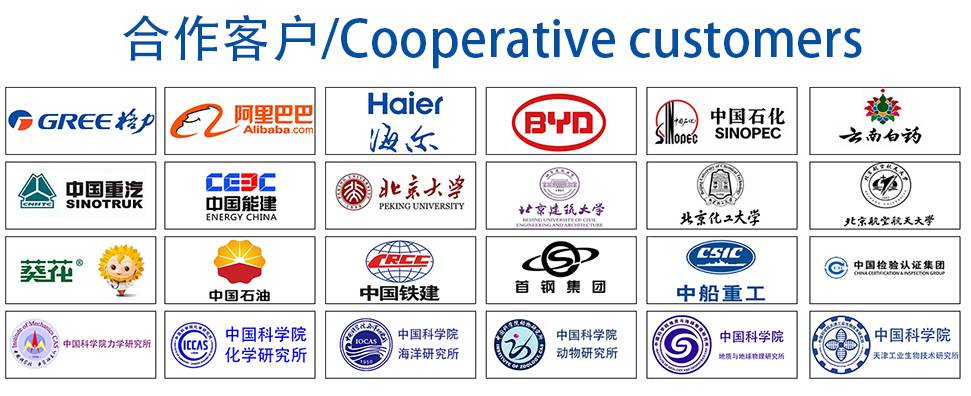
材料實驗室
熱門檢測
推薦檢測
聯系電話
400-635-0567