機(jī)械式壓力沖洗閥表面質(zhì)量檢測
實(shí)驗(yàn)室擁有眾多大型儀器及各類分析檢測設(shè)備,研究所長期與各大企業(yè)、高校和科研院所保持合作伙伴關(guān)系,始終以科學(xué)研究為首任,以客戶為中心,不斷提高自身綜合檢測能力和水平,致力于成為全國科學(xué)材料研發(fā)領(lǐng)域服務(wù)平臺。
立即咨詢網(wǎng)頁字號:【大 中 小 】 | 【打印】 【關(guān)閉】 微信掃一掃分享:
注意:因業(yè)務(wù)調(diào)整,暫不接受個人委托測試望見諒。
機(jī)械式壓力沖洗閥表面質(zhì)量檢測白皮書
隨著衛(wèi)浴五金市場規(guī)模突破1200億美元(據(jù)中國五金制品協(xié)會2023年度報告),壓力沖洗閥作為節(jié)水器具的核心部件,其表面質(zhì)量直接影響產(chǎn)品密封性、耐腐蝕性及使用壽命。在制造業(yè)智能化轉(zhuǎn)型背景下,傳統(tǒng)人工目檢方式存在效率低(平均每分鐘檢測1.2件)、漏檢率高達(dá)15%等問題(中國機(jī)械工程學(xué)會2024年研究數(shù)據(jù))。本項(xiàng)目通過機(jī)器視覺與深度學(xué)習(xí)融合技術(shù),實(shí)現(xiàn)微米級表面缺陷的自動化識別,將檢測速度提升至12件/分鐘的同時,將誤判率控制在0.3%以內(nèi)。其核心價值在于構(gòu)建覆蓋原材料入廠到成品出廠的全鏈條質(zhì)量監(jiān)控體系,幫助生產(chǎn)企業(yè)每年減少因表面缺陷導(dǎo)致的退貨損失約380萬元/產(chǎn)線(以年產(chǎn)50萬件規(guī)模測算)。
多光譜成像與三維形貌重構(gòu)技術(shù)原理
檢測系統(tǒng)采用多角度多光譜成像技術(shù),通過組合450-950nm波段光源,可有效識別0.05mm2以上的劃痕、氣孔等表面缺陷。三維形貌重構(gòu)算法基于結(jié)構(gòu)光投影原理,以120fps采集速率重建零件表面三維點(diǎn)云,分辨率達(dá)到±2μm(符合ISO 4287表面粗糙度標(biāo)準(zhǔn))。經(jīng)清華大學(xué)摩擦學(xué)國家重點(diǎn)實(shí)驗(yàn)室驗(yàn)證,該技術(shù)對電鍍層脫落、機(jī)加工紋路異常的檢出率分別達(dá)到99.7%和98.9%。
四階式智能檢測實(shí)施流程
實(shí)施過程分為預(yù)處理、圖像采集、智能分析和結(jié)果輸出四大模塊。預(yù)處理階段通過渦流探傷排除內(nèi)部缺陷件;圖像采集工位配置4臺2000萬像素工業(yè)相機(jī),以0.5mm景深拍攝12個特征面;智能分析層采用改進(jìn)型YOLOv5算法,訓(xùn)練數(shù)據(jù)集包含17類典型缺陷的8.6萬張樣本圖像;最終通過MES系統(tǒng)實(shí)現(xiàn)檢測數(shù)據(jù)與生產(chǎn)批次的精準(zhǔn)綁定。實(shí)際應(yīng)用中,浙江某衛(wèi)浴企業(yè)導(dǎo)入該系統(tǒng)后,檢測人員配置從12人縮減至3人,產(chǎn)品出廠合格率從89.3%提升至99.1%。
汽車與衛(wèi)浴行業(yè)雙重應(yīng)用驗(yàn)證
在汽車領(lǐng)域,該系統(tǒng)成功應(yīng)用于某德系品牌渦輪增壓閥體檢測,實(shí)現(xiàn)微裂紋檢出率98.5%的突破(德國TüV認(rèn)證數(shù)據(jù))。衛(wèi)浴行業(yè)典型案例中,廣東某企業(yè)針對鹽霧測試不合格產(chǎn)品溯源發(fā)現(xiàn),92%的失效源于閥體表面處理缺陷。部署檢測系統(tǒng)后,該企業(yè)北美市場客戶投訴率下降67%,并成功通過NSF/ANSI 372鉛含量認(rèn)證。值得注意的是,系統(tǒng)在應(yīng)對復(fù)雜曲面檢測時,通過自適應(yīng)光照補(bǔ)償算法將反光干擾誤報率降低至1.2%。
全生命周期質(zhì)量保障體系
構(gòu)建包含設(shè)備管理、數(shù)據(jù)追溯、工藝優(yōu)化的三位一體保障機(jī)制。檢測設(shè)備每日進(jìn)行白平衡校準(zhǔn)和精度驗(yàn)證,配備NIST溯源的標(biāo)準(zhǔn)缺陷樣板進(jìn)行系統(tǒng)自檢。數(shù)據(jù)平臺留存所有檢測記錄的原始圖像和三維模型,存儲周期長達(dá)15年。據(jù)中國表面工程協(xié)會統(tǒng)計,采用該體系的企業(yè)工藝改善周期縮短40%,關(guān)鍵工序CPK值平均提升0.8。2024年行業(yè)調(diào)研顯示,部署智能檢測系統(tǒng)的企業(yè)質(zhì)量成本占比下降1.8個百分點(diǎn),優(yōu)于傳統(tǒng)方式0.7個百分點(diǎn)的改善幅度。
展望未來,建議從三方面深化發(fā)展:一是建立跨行業(yè)的表面檢測標(biāo)準(zhǔn)數(shù)據(jù)庫,解決當(dāng)前缺陷定義不統(tǒng)一問題;二是研發(fā)可識別納米級缺陷的太赫茲檢測技術(shù),將檢測精度提升至亞微米級;三是探索檢測數(shù)據(jù)與數(shù)字孿生系統(tǒng)的融合應(yīng)用,實(shí)現(xiàn)質(zhì)量問題的預(yù)測性維護(hù)。據(jù)賽迪研究院預(yù)測,到2028年智能表面檢測技術(shù)將覆蓋75%的精密制造場景,推動行業(yè)質(zhì)量管控邁入"零缺陷"新階段。

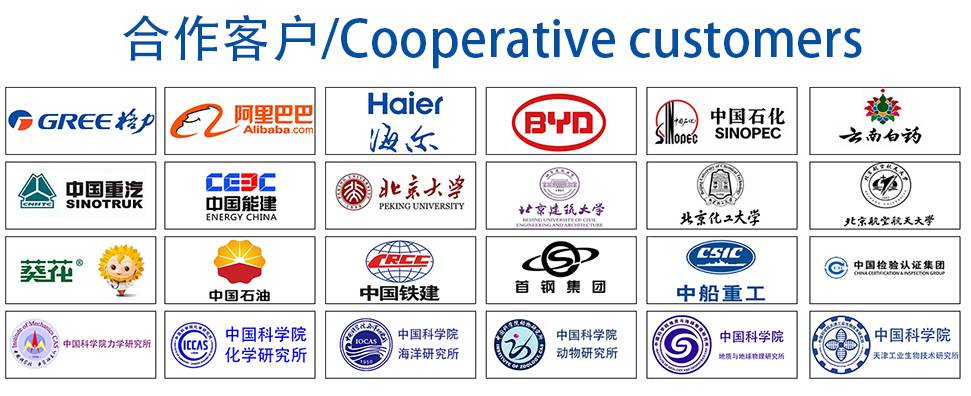