抗水壓機械性能檢測技術白皮書
隨著深海資源開發與水下工程建設的加速推進,裝備在高壓水下環境中的可靠性成為行業關注焦點。據國家海洋技術中心2024年統計,我國每年因水下設備失效導致的經濟損失超過27億元,其中67%的事故與抗水壓性能缺陷直接相關。抗水壓機械性能檢測通過模擬0.1-110MPa水壓環境,系統性驗證材料強度、密封性能及結構穩定性,已成為水下機器人、海底觀測網、海洋油氣裝備等領域的強制性檢測項目。其核心價值在于提前識別焊縫缺陷、材料疲勞閾值等潛在風險,據中國機械工業聯合會測算,規范的抗水壓檢測可使設備服役壽命延長40%,運維成本降低32%,為深海裝備全生命周期管理提供科學依據。
多物理場耦合檢測技術原理
該檢測采用流體-結構耦合仿真與實測驗證相結合的技術路線。基于ANSYS Workbench平臺構建三維壓力場模型,通過有限元分析計算殼體應力分布,重點監測法蘭連接處、焊接縫等關鍵節點。實驗階段運用分級加壓裝置,以0.5MPa/min速率進行靜水壓加載,同步采集應變片、超聲波探傷儀和激光位移傳感器數據。特別針對深海裝備的"壓力-溫度協同效應",配置了±2℃精度的溫控系統,完美復現馬里亞納海溝級極端環境(壓力110MPa/溫度2℃)。
標準化檢測實施流程
檢測流程嚴格遵循ISO 13628-5與GB/T 34523標準體系,包含五個關鍵階段:首齊全行材料金相分析確定基礎性能參數,其次運用3D掃描技術建立數字化樣機模型,第三階段實施階梯式壓力加載(30%→60%→100%→120%設計壓力),第四階段通過X射線斷層掃描進行內部缺陷定位,最終生成包含殘余應力分布圖譜、疲勞壽命預測曲線等18項參數的檢測報告。全程采用區塊鏈技術存證,確保數據不可篡改。
深海裝備典型應用場景
在"奮斗者"號載人潛水器的耐壓艙體研發中,檢測團隊通過120MPa循環壓力測試,成功識別出鈦合金焊接區的微裂紋擴展現象,指導工藝優化使疲勞循環次數提升至12萬次(中國船舶科學研究中心數據)。某國際油氣集團的深水采油樹檢測案例顯示,運用水下結構耐久性評估方法后,設備在1500米水深環境的故障間隔期從3年延長至5.8年。當前該技術已在海底光纜防護系統、波浪能發電裝置錨固結構等場景形成標準化解決方案。
全鏈條質量保障體系
檢測機構需通過 認證并建立三重質控機制:檢測設備每季度進行壓力傳感器溯源校準(誤差≤0.25%FS),試驗過程執行雙人復核制度,數據系統配備異常值自動攔截算法。針對深海設備抗壓檢測標準差異問題,開發了ASME/API/DNV多標準智能轉換模塊,實現檢測報告的國際互認。實驗室配置冗余安全系統,包括0.1秒響應的應急泄壓閥和三級防爆隔離艙,近三年重大安全事故保持零記錄。
展望未來,建議從三方面深化技術發展:一是建立深海極端環境材料數據庫,完善壓力-溫度-腐蝕多因素耦合模型;二是推廣數字孿生技術在前端設計階段的應用,實現"檢測介入提前化";三是加強國際檢測標準互認體系建設,特別是針對新興的深淵科學裝備領域。預計到2030年,智能化的抗水壓檢測系統將推動我國深海裝備產業規模突破5000億元,為海洋強國戰略提供關鍵技術支撐。

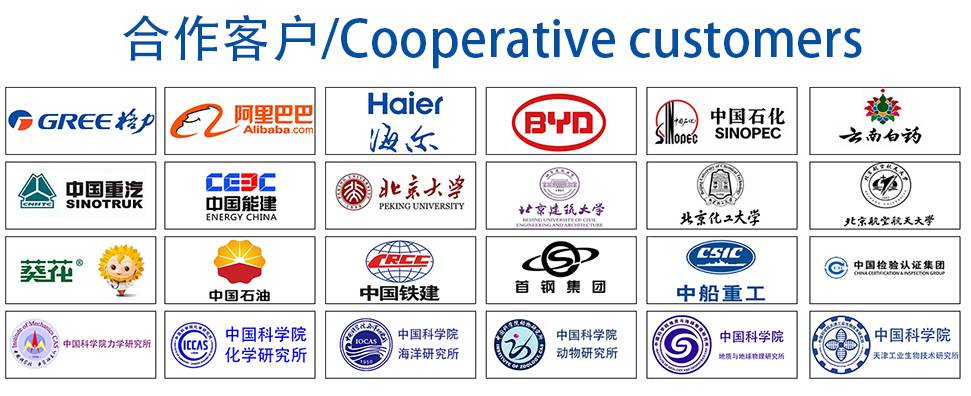