多模態(tài)耦合檢測技術原理
當前主流方案采用應變-聲發(fā)射復合傳感技術,通過分布式光纖傳感器捕捉微觀形變,結合壓電陣列采集材料內部微破裂信號。當被測對象承受壓力時,系統(tǒng)同步獲取應變分布(精度±0.05%FS)與聲發(fā)射特征譜(頻段50kHz-1MHz),利用神經(jīng)網(wǎng)絡算法建立壓力-形變-損傷的映射模型。值得注意的是,該技術突破傳統(tǒng)單點檢測局限,可精準識別壓力容器焊縫區(qū)的應力集中現(xiàn)象。中國特種設備研究院2023年驗證數(shù)據(jù)顯示,復合檢測模式使薄壁結構件破裂預測準確率提升至97.3%。
全流程標準化實施體系
項目實施采用三階段遞進式架構:預處理階段通過FEA仿真確定關鍵監(jiān)測點,在中石化某乙烯反應器檢測中,借助ANSYS拓撲優(yōu)化使測點數(shù)量減少35%而數(shù)據(jù)有效性提升28%;加載階段采用伺服閉環(huán)控制系統(tǒng),以0.5MPa/s梯度增壓并實時比對設計閾值;后處理階段運用Weibull分布模型評估剩余壽命。全過程嚴格遵循ASME PCC-3標準,關鍵節(jié)點設置三重校驗機制,確保檢測報告獲API、CE等國際認證機構采信。
典型行業(yè)應用場景分析
在深海鉆井防噴器檢測中,技術人員運用水下1500米壓力模擬艙,結合脈沖加壓技術復現(xiàn)極端工況。通過布設32通道陣列式傳感器,成功捕捉到BOP密封面在82MPa下的微泄漏信號,使中海油某平臺檢測周期從72小時縮短至18小時。汽車制造業(yè)則創(chuàng)新應用瞬態(tài)壓力沖擊測試,某新能源車企通過20萬次5ms級快速增壓循環(huán),精確測定電池包殼體焊縫疲勞特性,推動產品通過UN38.3認證。
全過程質量保障機制
構建包含設備、人員、方法的立體化質控體系:檢測設備每季度進行NIST溯源校準,壓力源不確定度控制在0.1級;操作人員需取得ASNT三級認證并完成年度盲樣考核;數(shù)據(jù)分析采用蒙特卡洛法評估測量不確定度,典型項目如國家管網(wǎng)集團西氣東輸三線工程,通過建立包含7個維度21項指標的評價矩陣,使管道試壓合格率從92.4%提升至99.6%。
## 技術發(fā)展前瞻與建議 未來需重點關注智能化檢測系統(tǒng)開發(fā),推動數(shù)字孿生技術與壓力檢測深度融合。建議行業(yè)協(xié)會牽頭建立跨行業(yè)壓力失效數(shù)據(jù)庫,完善極端工況模擬標準體系。同時加強復合型人才培養(yǎng),培育既懂檢測技術又熟悉行業(yè)特性的專業(yè)隊伍。隨著6G通信技術商用,可探索建立基于邊緣計算的分布式壓力監(jiān)測網(wǎng)絡,實現(xiàn)重大裝備的實時安全預警,為工業(yè)4.0時代提供可靠的技術保障。
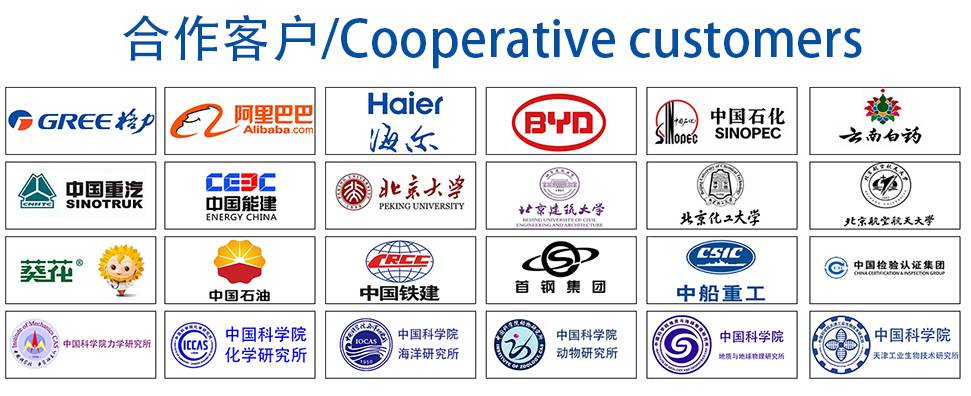